Motala har genom åren drabbats hårt av industrinedläggningar. Vi kan nämna Luxor/Nokia som lades ner 2002, den sista produkten som tillverkades var digitalboxar och vem minns inte bandspelarna och stereoanläggningarna. Electrolux spisfabrik lades ned 2011 och Dometic kylskåpsfabrik 2010.
– I Dometicfabriken tillverkade man närmare 1 400 kylskåp om dagen, när det var som mest tryck i försäljningen. Det mesta exporterades till USA, säger Stefan Westin som minns de dagarna när nedläggningarna var ett faktum.
Jag minns också torpedtillverkningen. Flera tusen jobb försvann under en tioårsperiod. Det händer saker i en stad eller på en ort när större industrier flyttar tillverkningen eller lägger ner verksamheter. Motala har varit nere på knä men kamplusten har varit stark. Och idag är företagarna nöjda med klimatet i Motala och man har en stark framtidstro igen. Men man måste räkna in fler jobb genom att titta i ett större perspektiv och geografiskt område.
Idag är det positiva vindar som blåser i hela regionen med ledande företag som Väderstad, BT i Mjölby men också Motala Verkstad Group. Vi är nu på besök hos Motala Hissar som fått en intressant nystart efter att finska KONE (som ägt bolaget sedan 1990), sålt bolaget till svenska LATOUR.
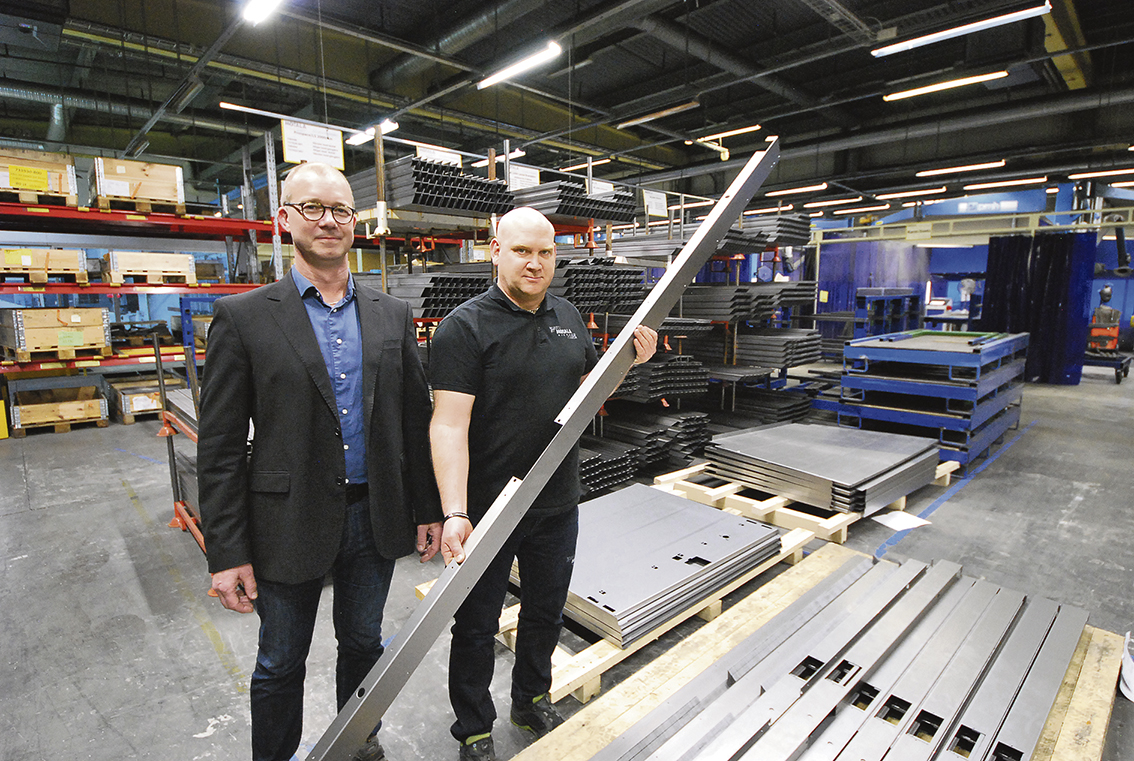
– Vår plan är att vara igång med produktion under maj 2022.
Nu blir det omstart för hisstillverkaren och man gör en mycket expansiv 5 års plan
Sedan juni 2021 ägs Motala Hissar AB numera av Latour Industries och ingår i Aritco Group AB. Latour är ett av de största investeringsföretagen i Sverige. Latours övergripande affärsidé är att investera långsiktigt i bolag med egna produkter och varumärken med stor utvecklingspotential. Filosofin går ut på att köpa eller investera i företag och få dem att växa på lång sikt.
– Vi är glada över att ha en ny ägare med ekonomiska muskler som tror på oss, våra produkter och som är villiga att investera i vår framtid, säger VD Stefan Westin.
Motala Hissar startade 1972 med tillverkning av garagedörrsautomatik som ledde vidare till tillverkning av varuhissar. Sedan 80-talet har företaget främst fokuserat på plattformshissar och smal-hissar som till övervägande del används för tillgänglighetsanpassning av byggnader. Verksamheten innefattar produktutvecklingen, tillverkning, support, export och inhemsk försäljning av hissar och reservdelar. Över 10 000 hissar har hittills levererats till kunder över hela världen. Omkring 70% av produktionen exporteras.
9 000 kvm produktionsyta
– Vi tillverkar det mesta här in-house, vilket är mycket viktigt för oss, det är vår teknikdrivna produktionsfilosofi. Full kontroll över hela produktionskedjan från råmaterial in till montering i egen regi. Vi tillverkar inga standardhissar utan i princip så ser alla våra hissar olika ut, så all konstruktion och produktion sker här i Motala, berättar Stefan Westin.
Är det svårt att tillverka hissar?
– Svaret på din fråga är ja, men allt är lätt om man kan det, skrattar Stefan, nej skämt åsido, så krävs mycket arbete från start till mål. Vi har lagar och förordningar att följa i fråga om olika säkerhetsklasser och funktioner -tester. De är även olika i olika länder.
– Men det finns en stor marknad för våra produkter och marknaden blir allt större. Tittar vi på Europa så ser vi ett ökat behov från flera länder, där det finns många fastigheter som har behov av hissar.
Det betyder en begränsning av hyresgäster då äldre och handikappade inte kan bo i dessa fastigheter. Och världen har en allt äldre växande befolkning så det betyder att fastighetsägare behöver bygga in hissar i redan befintliga hus och det är här som vi kommer in i bilden, säger Stefan Westin.
– Så vi är inte främst på den marknad där man bygger helt nya hus, utan vi är på plats med våra hissar där man behöver bygga in hissar eller bygga om befintliga byggnader beroende på förändrade regler, lagar och förordningar, tillgänglighet-, handikapps-anpassningar osv.
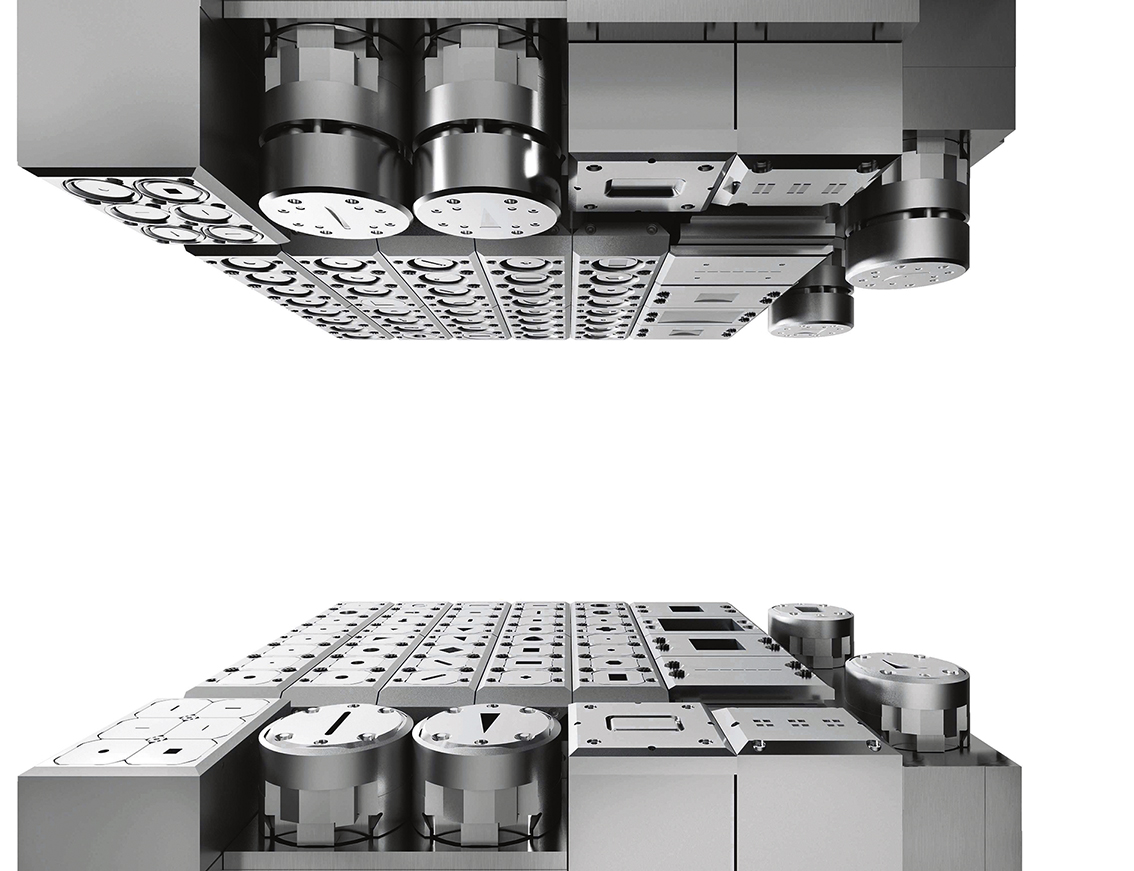
Äldre maskinteknik ut, ny maskinteknik in.
– Så varför står det nu en helautomatisk plåtformningscell från Salvagnini på plats idag. Jo, vår tidigare maskin var halvautomatiskt, vilket betyder att vi nu tar nästa steg inom automation men det främsta skälet var att den behövde bytas ut av åldersskäl. Att vi nu valde Salvagnini beror på att deras maskinkoncept med s.k KIT produktion passar vår produktionsfilosofi, att utveckla verksamheten mot att gå ifrån batch produktion till kundorderstyrd produktion, förklarar produktionschef Emil Eriksson.
Nu under 2022 har installationen påbörjats (och tidningens redaktör är på plats), av den nya helautomatiska S4Xe.30 från Salvagnini, vilket kommer innebära mer än en fördubbling av stanskapaciteten och framförallt ett första steg mot en helautomatisk produktionslinje.
– S4Xe.30 är fullt utrustad med MD lagertorn där Motala Hissar kommer ha en frihet att köra enstycks ämnen från 15 olika fack med en ladd tid på mindre än 30 sekunder. Varje plåt är dessutom förberedd på ladd bordet, så all ställtid minimeras till någon enstaka sekund, säger maskinsäljaren Erik Arden.
– Det unika multi presshuvudet (se foto sidan 6), kan ha upp till 96 verktyg, där samtliga stansar alltid är förberedda och fungerar enligt principen, som ett tangentbord. Salvagninis mjukvara STREAM och OPTI optimerar stansningen, så att den stans som är närmast, slår nästa hål och det ger maximalt utnyttjande av plåtämnena och minimalt med skrot. Tillsammans med vinkelsaxen optimeras stansningen ytterligare och behovet av skrotningsverktyg minimeras samt att skelettet klipps ner automatisk i skrotlådan. Allt detta gör att S4Xe.30 har en mycket intressant kapacitetsökning mot traditionella stansmaskiner.
Historien om S4:an sträcker sig tillbaka till 1977 då den första panelbocken P4 visades. Problemet som fanns då var att det fanns ingen stansmaskin som hade en kapacitet att förse en P4 med så mycket plåtämne som den svalde. Då kom iden med ett multipresshuvud där samtliga stansar alltid är stansförbredda detta tillsammans med en vinkelsax som kunde skrota ner skelettdelarna och få ett flöde mellan S4 & P4. 1978 visades den 1:a S4:an och året efter 1979 så var Salvagninis varumärke S4+P4 linjen på plats. Denna princip har vi på Salvagnini i vårt DNA att producera i linje där det är ett måste med en S4 som har en kapacitet som kan matcha en P4 både gällande hastighet men framförallt flexibiliteten för att undvika verktygsväxlingar som tar tid.
Genom åren har Salvagnini utvecklat både maskiner och mjukvara för en balansering och optimering i flödet som vi idag har Stackmodus och Packmodus. Där vi kan buffra ner och plocka upp material för att både optimera plåtutnyttjandet och vidare flödet i efterföljande produktion. Exempel om vi har ett efterföljande montagetempo så vill vi ha rätt plåt till montören i rätt ordning i blandade material kvaliteter utan att behöva mellanlagra i ett pallställ. Då har vi MD-tornet som kan hantera 15 olika material för ett färdigt kit, och då kan vi inte ha ställtider i maskinen som skapar flaskhalsar.
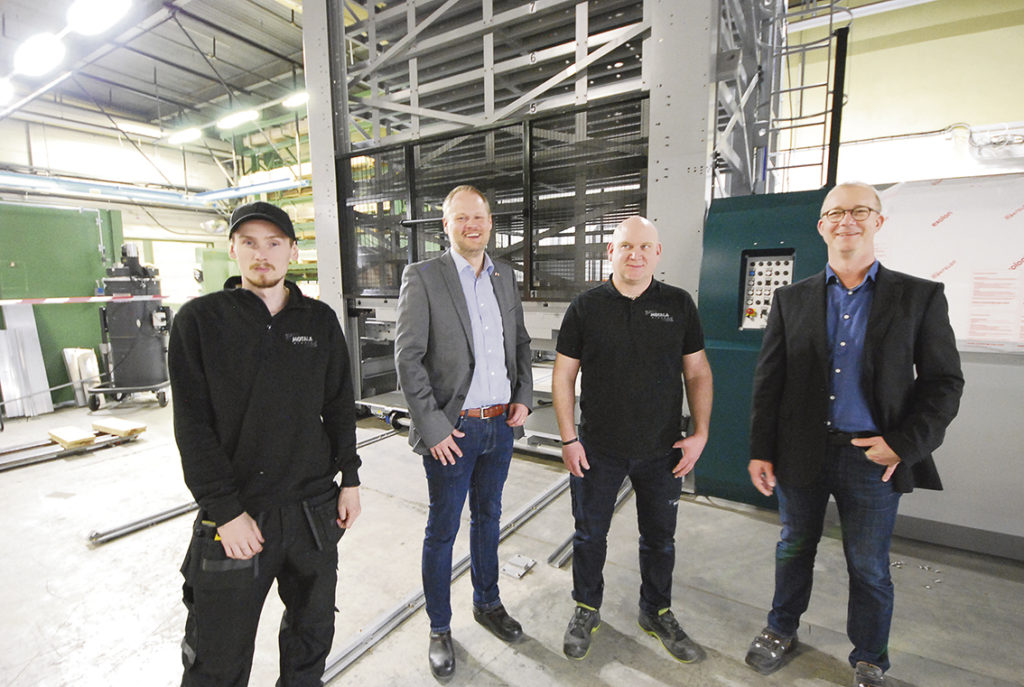