Vi beger oss till Malmö, parkernas stad. Så många parker ser vi inte, då vi styr vår redaktionella penna till Fosie industriområde och Kantyxegatan, där ett högteknologiskt svenskt företag har startat en tillväxtresa där man håller på att växa in i sin nisch med den unika Corebontekniken.
– Vi har uppfunnit och utvecklat världens snabbaste produktionsprocesser för fiberförstärkta kompositer, ofta tio gånger snabbare än konventionell teknik. Samtidigt drar den en bråkdel så mycket energi, med besparingar upp till 95 % vilket resulterar i nya högre standarder för material och delar till lägre kostnad.
– Alla tillverkningsprocesser av fiberkomposit beror på värme; vi erbjuder överlägsna värme- och tillverkningslösningar med jämn och styrbar temperatur från rumstemperatur till + 425 ° C utan begränsningar i storlek. Tekniken är tillämplig inom kompressionsgjutning, vakuuminjicering, fiberlindning, autoklavhärdning, induktionssvetsning och limning, säger vd Erik Ringdahl.
Nu är vi på redaktionen ute på djupt vatten och högteknologi är inte riktigt tidningens starkaste sida och skall så inte vara heller men vi är och blir nyfikna och ber om lite mer information från Erik;
Den energieffektiva tekniken hos skånska Corebon kom till tack vare utförsåkning och ett intresse från några skidentusiaster att utveckla nya material och metoder för kolfiberanvändning för effektivare skidor. Nu efterfrågas den applicerbara tekniken av fordonsindustrin, flygplanstillverkare och telekombolag.
Företaget är ett relativt ungt företag som grundades 2003. Idag är man ett högteknologiskt materialprocesslösningsföretag som utvecklar metoder för tillverkning av komponenter i fiberförstärkt plast baserat på induktionsvärmning. Tekniken är patenterad och möjliggör kostnadseffektiv tillverkning av lättviktsmaterial såsom glas- och kolfiberkomposit.
– Vårt huvudområde är processlösningar med värmning i fokus, men vi erbjuder även prototyp- och volymproduktion.. Kunden äger ritningen som vi tillverkar från. Vi hjälper även till med materialval, vi bistår i hela kedjan, säger vd Erik Ringdahl.
Het teknik och en tillväxtresa
De senaste fyra åren har bolaget gjort en fantastisk resa både gällande utvecklingen av den egna tekniken och en omsättningsökning som går att mäta i tusentals procent.
– Efter många år av utveckling och certifiering så är vi nu igång och levererar system till våra kunder på riktigt. Det kan handla om en viss position i en tillverkningslina, om ett enskilt verktyg, eller om en hel nyckelfärdig lina, säger han.
Men det hela började i de franska alpernas skidbackar. Skidfantaster började experimentera med tunna, lätta och slitstarka skidor i kolfiberkomposit, mest på kul.
I samband med skidutvecklingen upptäckte man att produktionstekniken utöver kraftigt reducerad cykeltid även kunde minska mängden plast i kompositmaterialet.
Exempel på skräddarsydda produkter, säger Erik, är radartransparenta väderskydd (radomer) till telekomsektorn, som tillverkas i en sandwichkonstruktion av olika plaster. Här ingår ingen kolfiber eftersom materialet inte får vara elektriskt ledande, samtidigt som det ska klara temperaturer mellan minus 50 och plus 80 grader utan att påverkas.
Fler exempel handlar om att elektrifieringen i bilindustrin öppnar en stor potential för Corebons kompositmaterial.
– På grund av de tunga batterierna måste de få ner fordonsvikten på annat håll. Där vill vi komma till nytta genom att sänka vikten på chassi och kaross, säger Erik.
Flygindustrin är en annan viktig sektor. För att nämna ett par exempel är både den senaste versionen av Boeings 787 Dreamliner, och den nya Airbus som lanserades i vintras, till cirka 50 procent byggda i kolfiberkomposit så här finns mycket att erbjuda.
– Vi vill att kompositindustrin från fibertillverkning till kompositåtervinning ska använda våra processer för att få ner produktionskostnaderna och energiförbrukningen, avslutar vd Erik Ringdahl.
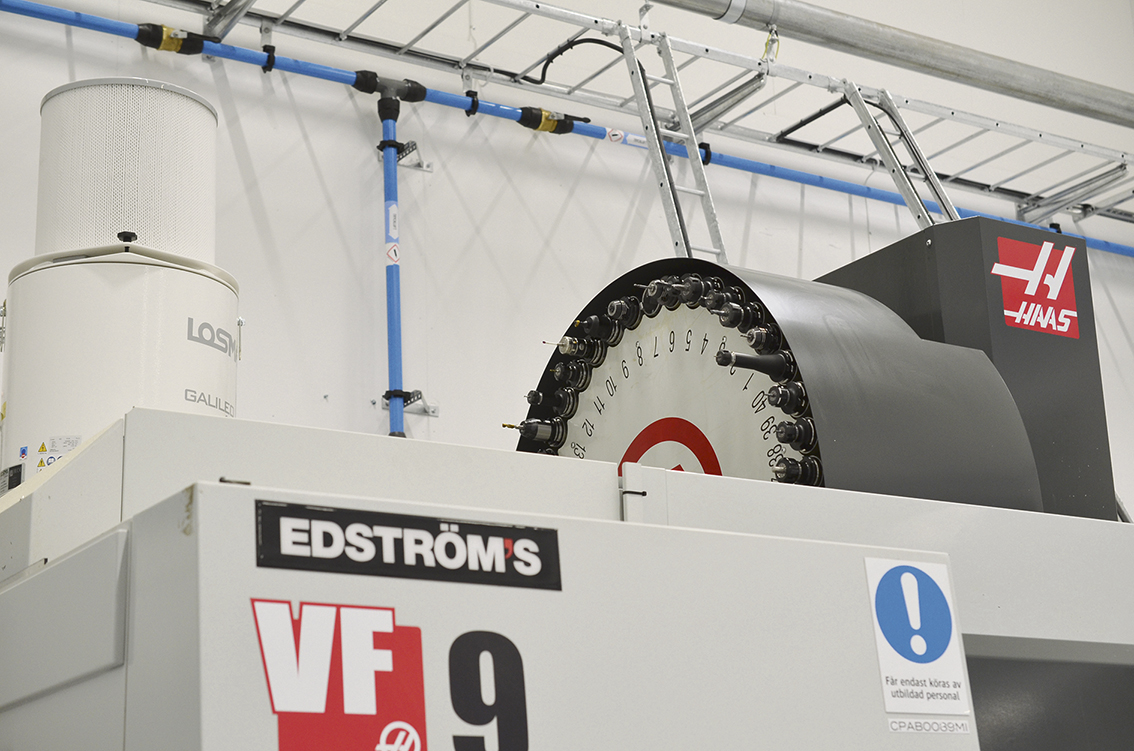
Riccardo Luzi
Italienare från Florens och nu arbetande som maskinoperatör/ställare/tekniker, sedan två år på Corebon AB.
– Jag kan köra alla maskiner, då jag har trettio års erfarenhet av manuella och CNC-styrda verktygsmaskiner. Jag är en utdöende art, för snart finns ingen kvar som kan köra manuella maskiner. Att köra CNC-maskiner är lätt, säger Riccardo lite skämtsamt.
– Idag har vi några manuella maskiner kvar i vår verkstad men företaget har sedan två år tillbaka investerat
i en fleroperationsmaskin HAAS VF 9.
– Maskinen har ett arbetsområde på 2 000 x 1 000 mm, så vi får plats med stora verktyg. Pratar vi stora verktyg så kan det vara körning en hel helg så då gäller det att ha pålitlig utrustning.
Vi skall prata arbetsmiljö med Riccardo och här får vi information om att man nu har, sedan ett år tillbaka, kompletterat sin CNC-maskin med produkter från LOSMA. Vad det handlar om specifikt skall vi få experthjälp av Stefan Thuresson som arbetar med arbetsmiljöprodukter på Chuckcenter.
– Allt högre bearbetningshastigheter gör också att verktygen ”slår sönder” skärvätskan och oljedimma bildas. Vi tillverkar formar/verktyg i maskinen och det handlar om material av aluminium, verktygsstål, plaster och olika kompositer som kräver rening av skärvätskan efter bearbetning från spånor och komposit-”mjöl” (kan liknas mer som babypuder), säger Riccardo.
– Det är väldigt viktigt att ha en ren arbetsmiljö och då behövs utrustningar som experter som Stefan på Chuckcenter säljer/installerar. Så vi kontaktade Chuckcenter via deras återförsäljare Malmö Maskin AB som också hjälpt till och vi har fått installerat riktigt bra grejer.
– För det är det som man inte ser som är farligt för människan, säger Riccardo.
Stefan Thuresson
Att regelbundet jobba med förbättringar i arbetsmiljön är inte bara ett lagkrav utan ger framför allt effektivare verksamhet och friskare anställda. Man påverkas av den luft man andas. Om man upplever luften som frisk mår personalen bra. En bra ventilation behövs för att föra bort luftföroreningar som i detta fall handlar om oljedimma men också fukt och dålig lukt.
– En verkstad utan bakterier och dålig luft. Det är målsättningen för mitt dagliga arbete ute på svenska verkstäder. LOSMA grundades 1974 av italienaren GianCarlo (med samma efternamn) för att utveckla och producera system för oljedimavskiljare och filtrering av skärvätskor för verktygsmaskiner. Redan från början var affärsidén att verka inom området hälsa och miljö. LOSMA reningsprogram för luft och vätskor har funnits i Chuckcenters sortiment sedan 2018. I båda segmenten finns ett antal produkter som kompletterar varandra väl vad det gäller funktionalitet och nytta, berättar Chuckcenters Stefan Thuresson som har lång erfarenhet av arbetsmiljöprodukter.
Detta har Corebon installerat.
– Två stycken Losma Galileo Plus GP2000 Oljedimavskiljare med Hepa H13 efterfilter. Luftflöde: 2160 m3/h per enhet.
Ett Losma DTE150 Skärvätskefilter med bandpappersfilter, reningsgrad 10 µm. Tankkapacitet: 445 liter. Filtreringskapacitet: Emulsion: 150 liter/min. Rak olja: 75 liter/min.
– Corebons behov var dels att få bukt med oljedimman, då deras nya maskin är placerad i ett begränsat utrymme, men även att rena skärvätskan från partiklar som uppstår vid bearbetning av deras speciella material.
– Lösningen blev Losmas oljedimavskiljare Galileo Plus och deras reningssystem för skärvätska, Losma DTE, bandpappersfilter med ett flottörsystem som interagerar med maskinens befintliga skärvätskesystem.
Luftreningen:
– Losma Galileo Plus är ett centrifugalfilter för oljedimma skapad av emulsion och raka oljor vid bearbetning i maskinen. Filtret finns i 5 olika modeller med flöde från 325 till 3 500 m3/h. Reningsgraden är 95 %, med ett Hepafilter H13 ökar den till 99,97 %.
– Det som oftast avgör valet av filter är storleken på bearbetningsrummet, men även typ av skärvätska, bearbetningsmaterial, typ av bearbetning och längden på cykeltider.
– I denna typ av maskin behövs det oftast två utsugspunkter på grund av att det är ett stort bearbetningsrum med mycket volymer på båda sidor om spindeln. Risken finns om man har enbart en utsugspunkt vid ena sidan om spindeln, att oljedimman passera dörren till maskinen. När den öppnas, åker oljedimman rakt ut i lokalen i stället för att passera filtret först.
– I Losmas sortiment finns även Darwin-serien, som också är ett centrifugalfilter. Detta är vinklingsbart i tre olika lägen för att förenkla monteringen vid behov. Finns i 4 olika modeller med flöde från 600 m3/h till 3 000 m3/h. Reningsgraden är 95 %, med ett Hepafilter H13 ökar den till 99,97 %.
– Behöver man ett större filter eller rentav en centralanläggning finns Argos Pro som har flöden från 3 000 m3/h till 15 000 m3/h. Dessa finns även med Hepa H13-filter och kolfilter för att ta bort dålig lukt.
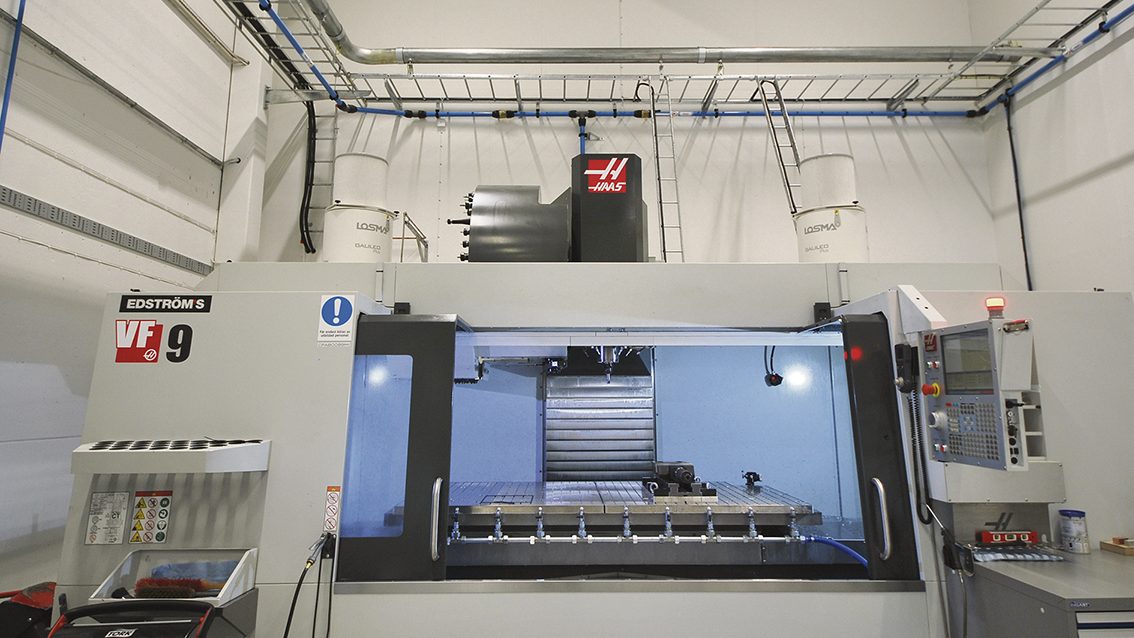
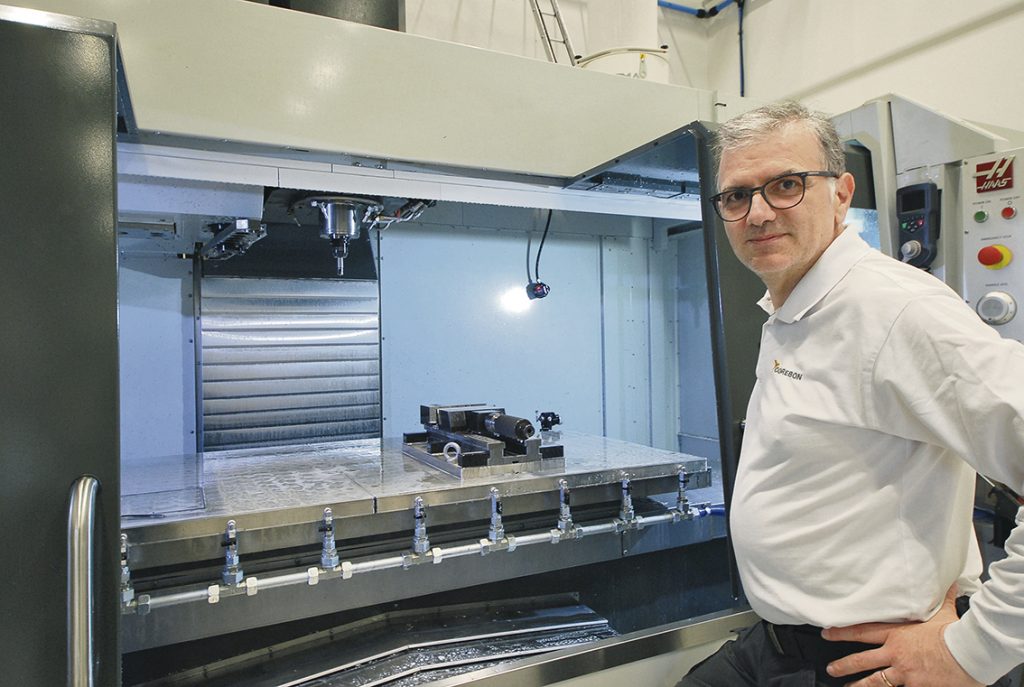
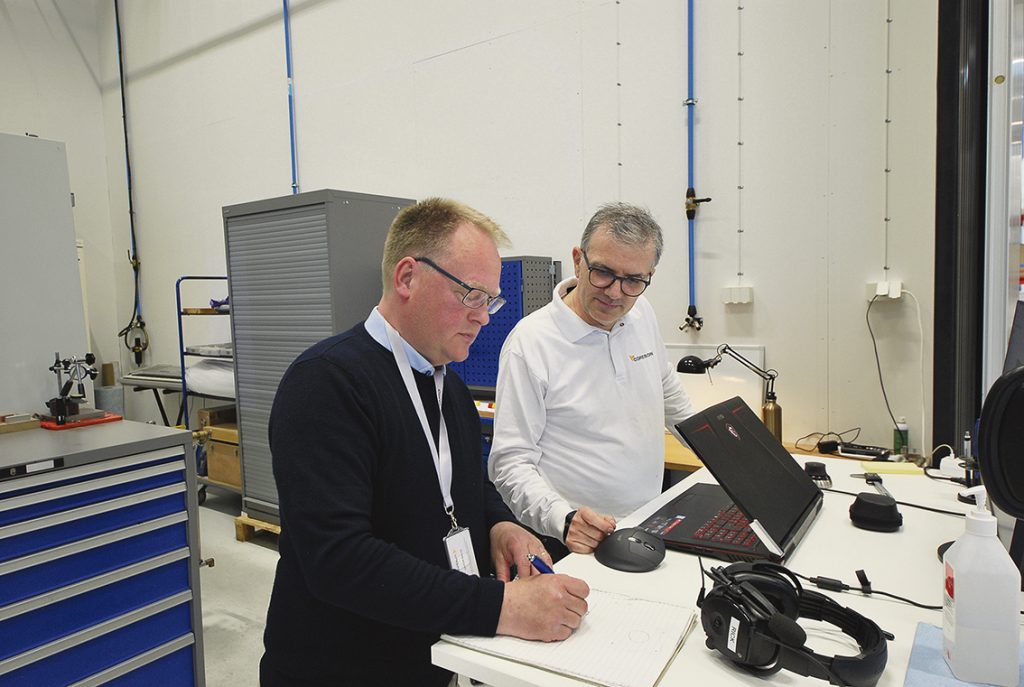
Skärvätskereningen:
– Losma DTE 150 skärvätskefilter är ett bandpappersfilter med en tankstorlek på 445 liter med en filtreringskapacitet på 150 liter/min. (emulsion), 75 liter/min. (raka oljor).
– Vid installationer som hos Corebon, placerar man DTE-tanken bredvid maskinen och maskinens befintliga skärvätskepumpar flyttas över till denna tank som kommer att fungera som rentank. I maskinens skärvätsketank installerar man en evakueringspump med tillhörande flottörsystem som håller koll på nivåerna, härifrån pumpas den smutsiga skärvätskan till Losmas DTE-filter.
Vätskan hamnar på ett filtermedia bestående av, en filterduk med (i Corebons fall) en reningsgrad på 10 µm. När filterduken mättats av smutsen, stiger vätskenivån och flottören skickar en signal till filtermotorn att mata fram nytt papper så att vätskan faller igenom. Förbrukat filterpapper samlas upp i en behållare.
– Losmas DTE-serie finns som enbart tank, för att sedan kunna byggas på med bandpappersfilter, magnetfilter oljeskimmers, skärvätskekylare m.m. DTE-serien finns i tankstorlekar från 50 till 1 400 liter. Detta system fungerar även utmärkt till att rena tvättvätskor från industritvättar.
– Filterpapperet som finns i alla olika storlekar och som passar till alla filterenheter oavsett fabrikat, finns med reningsgrad från 70 µm ned till 10 µm.
Förutom DTE-filterna finns Master-serien som är så kallade gravitationsfilter, med samma princip för rening som DTE-filtret. Dessa filter kan byggas mer på höjden om det är lite plats i verkstaden.
Losma Spring och Spring Compact är så kallade trumfilter som är självrengörande. I dessa filter använder man ett finmaskigt metallnät med reningsgrad ned till 25 µm och därmed slipper man all förbrukning av filterpapper. Principen är den samma som för DTE och Master-filterna, att smutspartiklarna samlas på filterytan, och när vätskan stiger matas filtret fram. Som option kan man utrusta dessa filter med Auto Clean System som kontinuerligt tvättar filtertrumman med jetstrålar. Losma Spring och Spring Compact passar bäst för centralsystem eller större maskiner, som tillbehör kan nämnas slamkomprimator, magnetfilter och skimmers.
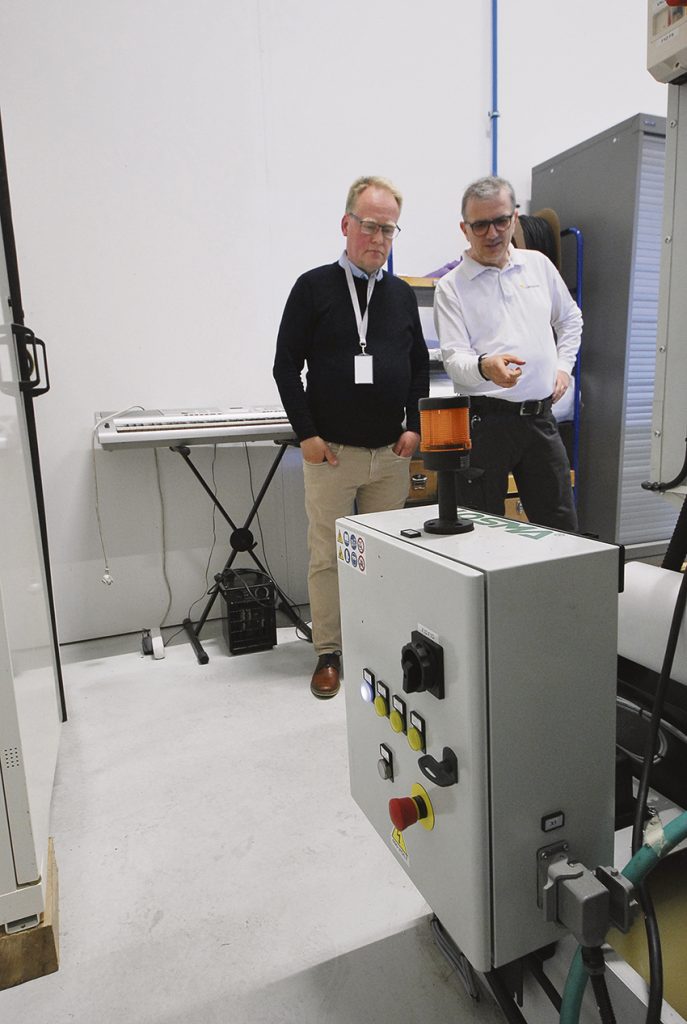
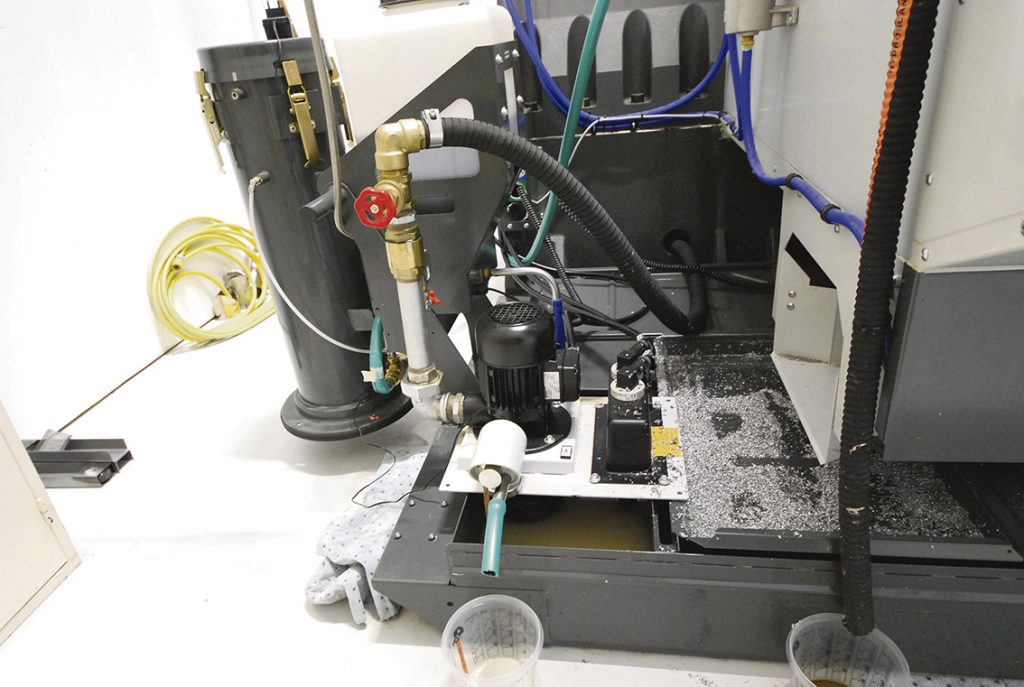
Har man mycket magnetiska små partiklar i skärvätskan som inte fastnar i bandpappersfiltret, kan man komplettera med LOSMA magnetfilter DMD/DMD-P med roterande magnetiska diskar, berättar Stefan Thuresson på Chuckcenter.
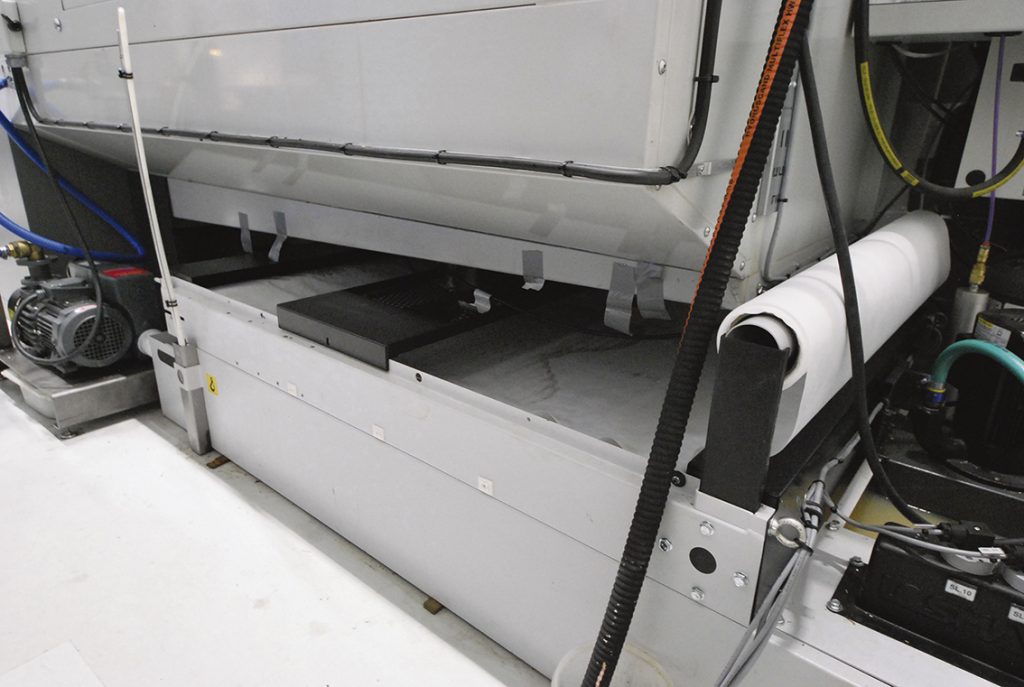