Mastec är en småländsk industrikoncern som är redo att serva sina kunder så att de vinner sitt race. När det gäller större industriprojekt har man som helhetsleverantör ett helt team bakom sig, från idé och produktutveckling till serietillverkning och montering. När man från företagets sida säger sitt mantra ”Passion for production” är det inte bara tomma ord. Alla företagets medarbetare älskar utmaningen i krävande uppdrag när toleranserna är snäva och leveranstiden odiskutabel.
Besök på Mastec Components i Ulricehamn
Med ett stort antal fleroperationsmaskiner är man redo att utföra komplicerade uppdrag i aluminium, stål, rostfritt och plast men även i mer högteknologiska specialmaterial.
– Vi förfogar över avancerad testutrustning där vi säkerställer att både prototyper och serieproducerade komponenter håller rätt prestanda för att uppfylla olika kvalitets- och branschcertifieringar. Våra produkter möter höga krav i bland annat försvars-, entreprenad, olja och gas samt medicin- och livsmedelsindustrin, säger Per Selskog marknads- och försäljningschef för Mastec koncernen.
– Jag kom till Mastec Components i Ulricehamn hösten 2013. Maskinparken var lite eftersatt och hade gått många produktionstimmar och vad jag förstod då så hade våra konkurrenter investerat i nya maskiner och ny teknik, så vi kände att vi behövde se över vår verkstad. Då hade vi svårt att få fram ett relevant mätetal på hur vi utnyttjade vår maskinpark så bestämde vi oss för att börja mäta för att få reda på hur vi utnyttjade våra resurser, säger fabrikschef Lars-Erik Larsson.
– I samarbete med högskolan i Jönköping gjorde en av skolans studenter sitt examensarbete här och tillsammans med produktionsansvariga genomfördes en noggrann analys där målet var att se om mer avancerade maskiner kopplade till automation kunde göra oss mer konkurrenskraftiga, säger Lars -Erik Larsson.
– Vår ambition är att vara världsledande på skärande bearbetning med automationslösningar och den resan började vi för ett år sedan och nu levererades och installerades de första maskinerna här som var kopplat till automation.
– Vi såg att vi började tappa i konkurrenskraft, det blev allt svårare att vinna nya affärer och det blev en utmaning för oss att behålla affärer också så koncernledningen beslöt att skjuta till pengar för att snabbt skapa ett incitament för en rejäl satsning på ny produktionsteknik, säger Per Selskog och berättar att man nu tog kontakt med ett antal leverantörer för att starta en dialog och få till förslag på hur man kunde utveckla sin produktion med nya strategiska beslut och få till ett nytänkande som allt i ett kunde leda vägen till att få en lösning att kunna erbjuda en produktion i världsklass.
Några krav var att hitta en standardiserad automationslösning som man skulle kunna utnyttja maximalt vid bl.a. parallell produktion. Små serier med snabba växlingar mellan olika artiklar, längre serieproduktion obemannad körning och ibland låta en maskin kopplas från robotcellen och köra manuell körning och den andra maskinen i automationscellen fortsätter med sina körningar, alltså en helt oberoende flexibilitet som kunde öka maskinutnyttjandegraden maximalt och framförallt minska ställtiderna rejält.
Efter noggrann analys av marknaden så fastnade man för en funktionell helhetslösning som DMG MORI Sweden och System 3R presenterade tillsammans och vi får här förklarat lite från maskinleverantören, automationstillverkaren och med Mastec som kund, hur allt utformades.
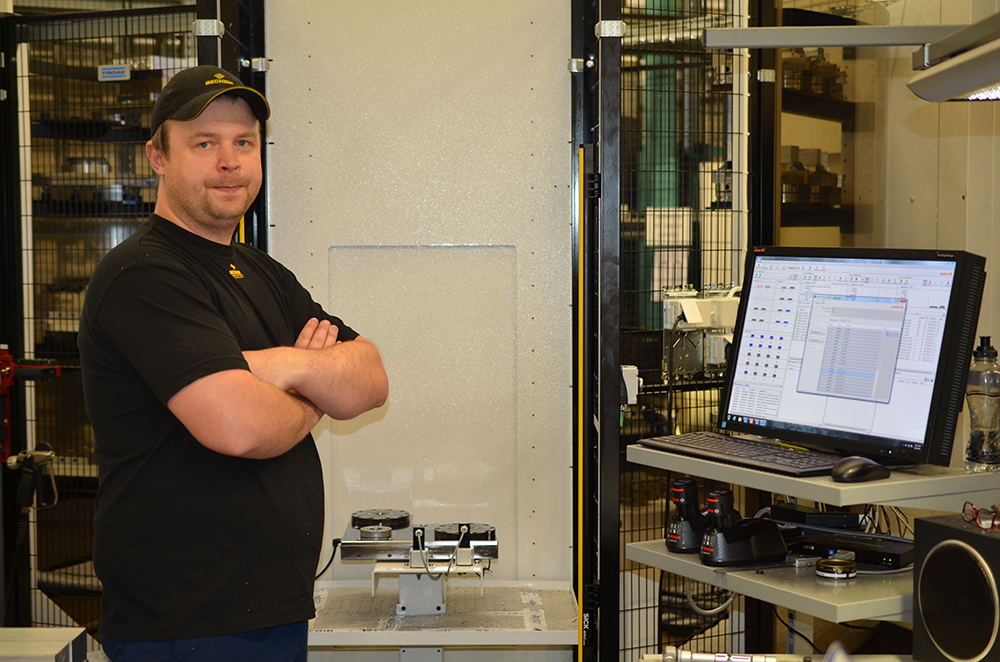
Peter Smith ansvarig säljare på DMG MORI Sweden berättar om vad man valt för maskiner.
– Mastec har valt 2 stycken modell DMU 60 eVo , 5-axlig vertikal fräsmaskiner med samma optionsval på både. Det ger en flexibel produktionscell där samma jobb kan köras är både maskiner.
DMU 60 eVo lämpar sig särskilt bra till automatisering tack vare palettladdning från sidan som betyder att robotcellen jobbar vidare vid t.ex. riggning av en maskin.
Bordsstorlek diameter 630 mm ger ett bra arbetsområde som täcker Mastec:s behov.
Verktygsmagasin med 120 verktygsplatser ger möjlighet till ett permanent verktygsuppsättning som är likadant i både maskiner.
All programmering sker i ett CAM system och program kontrolleras med en virtuell simulering. Det innebär NOLL riggtid vid maskinen.
Mastec upptäckte snabbt det faktum att DMU 60 Evo är en extremt måttstabil maskin, vilket betyder att man får ut första bit med rätt mått direkt. Det är mycket uppskattat bland alla, mätfrekvenserna har minskat rejält och kvalitén på tillverkningen har förbättrats.
DMG MORI’s CELOS kontroll är också en nyhet för operatörer och tekniker på Mastec som är mycket uppskattad. Kontrollen ger nya möjligheter för operatören att få en helhets överblick på maskinens status.
Maskinerna står som sagts spegelvända mot varandra med automationen från System 3R i mitten, med laddning från sidan och inte kanske som brukligt framifrån. Detta ger operatörerna mycket god åtkomst i maskinen och ger en ergonomiskt mycket bra lösning. Anläggningen installerades i under våren 2016 och man har redan 80 nya program/artiklar i cellen vilket betyder att kunderna har reagerat positivt på Mastec´s investering och på vilka kapacitetsnivåer man nu rör sig i och mot.
Vi vänder oss till Lars Westin som representerar den andra integratören i automationscellen och han ger sin syn på System 3R :s roll.
– Vi samarbetar ofta med maskinåterförsäljare och detta var ett av flera projekt med DMG MORI som integrerar våra produkter på ett mycket bra sätt med en flexibilitet och en lösning som Mastec Components i Ulricehamn är mycket nöjda med i det här fallet. Vårt automationskoncept är modulärt och ger kunden möjligheten att bygga ut sin robotcell i flera steg om och när det blir önskvärt.
– Roboten är av typen System 3R Transformer 1500/150 med 150kg:s lyftkapacitet, 2 palettstorlekar baserat på referenssystemet Delphin, också från System 3R. Antal palettplatser är för närvarande 14 st stora paletter och 20 st små. Varje palett har ett ID-chip för identifiering. Palettstorlekar: 400 x 400 mm för möjlighet att hantera stora arbetsstycken och diameter 156 mm för bästa åtkomlighet vid 5-axlig bearbetning.
– Referenssystemet Delphin är ett modulärt system i sig självt och byggs upp efter aktuellt projekt. Mastec har en basplatta med 4 st chuckar i varje maskin som hanterar den stora paletten direkt och den lilla via chuckadapter som roboten automatiskt laddar in vid behov. Chuckadaptern är i princip en specialpalett med en uppbyggd och centrerad Delphin singelchuck som kan hantera de små paletterna. Varje chuck har 6 tons hållkraft och systemet repeterar på 5 tusendelars millimeter.
– Alla paletter har någon typ av fixtur monterad på sig, ett eller flera skruvstycken eller egentillverkad fixturering oavsett så är det viktigt att operatören spänner fast rätt detalj på paletten. (se bild sid 107).
Här kan operatören se ett foto på bildskärmen som visar detaljens läge i skruvstycket – detta läggs till ställbladet så att man får rätt fastspänning varje gång för annars kan det bli problem…
– Hela robotcellen körs med hjälp av System 3R:s mjukvara WorkShopManager som är utvecklat för maximal flexibilitet vid automatisering av få stycksproduktion. Mjukvaran kan hantera både stora och små serier ända ner till en styck – man behöver inte köra en artikel i taget utan kan fritt blanda olika jobb lite som det passar. Hos Mastec brukar det ofta handla om ett 10-tal olika artiklar som hanteras i robotcellen samtidigt, berättar Lars Westin på System 3R.
– För oss handlade det inte så mycket om cykeltid utan det primära är ställtiderna och få en optimal flexibilitet i våra operationer där det ofta handlar om små serier runt 20 detaljer. Här har vi nu fått en lösning som vi kan växa med och vi lär oss mer och mer. Och vi ser en helhet i och runt automationen där vi jobbar med ständiga förbättringar och här ser vi också hur våra operatörer växer i sin roll både kompetensmässigt och hur man praktiskt sköter t.ex. logistiken runt omkring anläggningen. Praktiskt hur man förbereder jobben med laddning av artiklar och plundring av färdiga komponenter, vi har fått ett riktigt lyft tekniskt och kvalitén har förbättrats, säger Lars-Erik Larsson fabrikschef på Mastec Components i Ulricehamn och avslutar med att konstatera att företagets produktionstekniker som tidigare var upptagna med olika produktionstekniska problem och beredning/programmering, nu fått mer tid över till att ligga ett antal steg före, förhindra problem innan de uppstår vilket är en mycket positiv effekt av vår nya automationscell.