Att ge bilens hjärta – batteripaketet – ett bra skydd är ett viktigt mål för alla elbilstillverkare. Samtidigt finns alltid en strävan efter att spara vikt. Så hur ser den optimala lösningen egentligen ut?
– I dag kan batterifack tillverkas i stål, aluminium, SMC-material eller en kombination av flera material för att möta kraven på kostnadseffektivitet, låg vikt och säkerhet, berättar Dr. Michael Machhammer, manager för Development of Forming Processes & Tooling på AP&T.
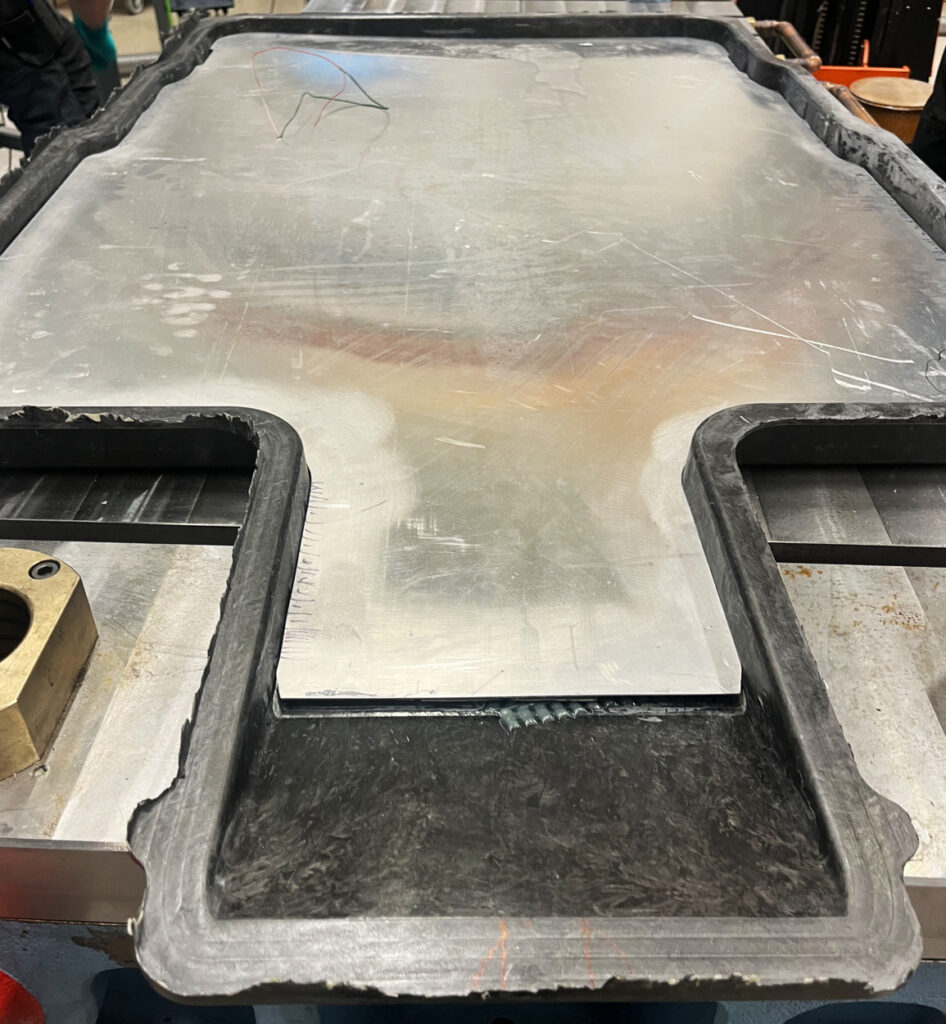
Den lösning som parterna i samarbetsprojektet har utvecklat förenar många av de egenskaper som biltillverkarna efterfrågar. Jämfört med det batterifack i stålplåt som använts som referens har de uppnått en viktminskning på 18 procent. Dessutom är krocksäkerheten betydlig bättre. Vid sidokollisioner visade simuleringarna 75 procent mindre materialdeformation och vid islag underifrån (så kallat bollard-test) noterades en förbättring på cirka 30 procent.
Kostnadseffektiv tillverkning
För att en ny konstruktionslösning ska bli verklighet är en viktig förutsättning att den kan produceras i en rationell och kostnadseffektiv process. Också här har projektet levererat. Hela komponenten tillverkas i ett enda formningssteg, där C-SMC-material appliceras på aluminiumskumkompositen tillsammans med specialdesignade sensorer från FiberCheck. För att säkerställa hög precision vid formningen används en servohydraulisk press och ett dedikerat verktyg. De integrerade sensorerna mäter temperatur, luftfuktighet och en rad andra parametrar i batteripaketet som kan påverka battericellernas kapacitet och livslängd.
– Våra resultat visar hur nästa generations optimerade batterifack kan konstrueras och tillverkas. Nu ser vi fram emot att ta vår lösning vidare i dialog med intresserade OEM:er och Tier 1-leverantörer, säger Michael Machhammer.
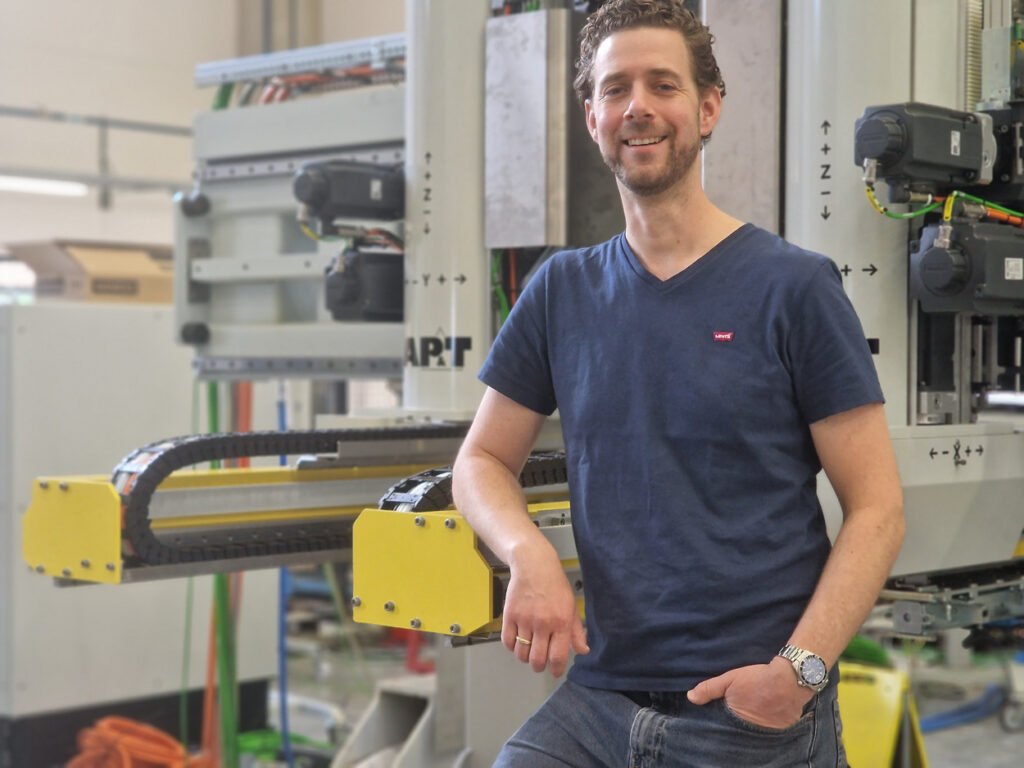
Vem har gjort vad i projektet?
- AP&T konstruerade och tillverkade verktyget, och demonstratorkomponenten tillverkades av RISE med en servohydraulisk press från AP&T.
- RISE tillverkade demonstratorkomponenten vid sin testanläggning i Piteå, Sverige.
- Fraunhofer IWU designade och genomförde simuleringar av komponenten.
- FiberCheck designade och tillverkade sensorerna som integrerades i hybridstrukturen av C-SMC och aluminiumskum under formpressningen vid RISE.
- Vinnova, Sveriges innovationsmyndighet, bidrog med finansiering.
AP&T
Box 32, SE-523 21 Ulricehamn
Rönnåsgatan 3A, SE-523 38 Ulricehamn
Sweden
Phone: +46 10 471 3858
Mobile: +46 708 31 75 48
Switchboard: +46 10 471 3500
E-mail:helen.sallander@aptgroup.com