Att göra bilar lättare, energieffektivare och säkrare är en utmaning för hela fordonsindustrin. Amerikanska elbilstillverkaren Lucid Motors valde en ny, innovativ teknologi för att ta sig an uppgiften. I Lucid Air, som lanserades 2021, används ett flertal unika lättviktskomponenter av varmformad höghållfast aluminium, konstruerade, tillverkade och industrialiserade i samarbete med AP&T och fischer Group.
– Vi är oerhört stolta över att ha fått möjlighet att bidra till förverkligandet av den här fantastiska bilen. Lucid Motors är en av de första fordonstillverkarna i världen som använder komponenter av varmformad höghållfast aluminium framställda med vår teknologi. Det gör deras framgång till en viktig milstolpe även för oss, säger Dr. Christian Koroschetz, Chief Sales Officer på AP&T.
2015 sökte Lucid efter ny teknologi som skulle kunde användas för tillverkningen av kollisionskritiska fordonsdelar, som dörringar, B-stolpar och skyddshöljen till batteripaket, och vände sig då till AP&T.
En spännande utmaning
Lucid presenterade ett antal komponent- och processkrav, vilket gav AP&T incitament att söka nya, avancerade processer, som skulle göra det möjligt att tillverka produkter med låg vikt, hög formbarhet och hög styrka, i stora volymer.
Samtidigt var AP&T djupt involverat i innovationsprojekt som just fokuserade på att undersöka hur höghållfast aluminium skulle kunna användas för att producera bilkomponenter med låg vikt och hög styrka. Det var avgörande för Lucids val av AP&T som leverantör till Lucid Air.
– AP&T presenterade en lovande ny teknologi. De potentiella fördelarna var betydande, eftersom varmformningen gjorde det möjligt att tillverka delar med komplex geometri i höghållfast aluminium. Tack vare kombinationen av hög formbarhet, hög styrka och låg vikt kunde komponeternas konstruktion verkligen optimeras. Det gjorde att det tillgängliga utrymmet kunde utnyttjas på ett effektivare sätt samtidigt som vi kunde uppnå både hög krocksäkerhet och låg energiförbrukning – allt till till fördel för slutkunden, säger Eric Bach, Senior Vice President of Product and Chief Engineer på Lucid.
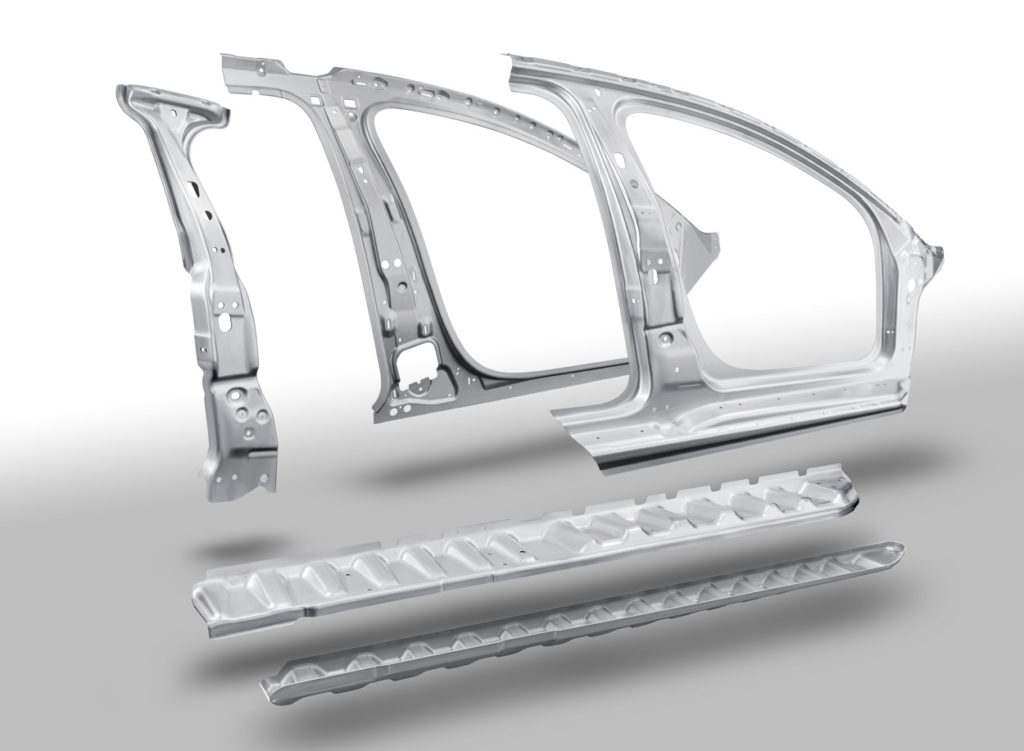
Lösningen utvecklas med simuleringar och prototypverktyg
Under 2017 intensifierades utvecklingsarbetet med hjälp av CAE-analyser (Computer Aided Engineering). AP&T:s formningsexperter använde FEM-simuleringar för att upptäcka eventuella risker för sprickbildning i plåten under formningsprocessen. Lucids ingenjörer använde sedan simuleringsresultaten för den fortsatta utvecklingen av karosskomponenternas konstruktion.
Samma år presenterade AP&T den första fullskaliga produktionslinjen för varmformning av höghållfast aluminium för att demonstrera den nya teknologins potential. Innovationen belönades med den prestigefulla utmärkelsen Altair Enlighten Award. Ett erkännande som bekräftade att AP&T var på rätt väg och gav extra momentum till samarbetet med Lucid Motors.
Under 2019 och 2020 genomfördes ett rad prov för att validera formningsprocessens stabilitet och få fram testdata. Eftersom komponenternas konstruktion är avgörande för att uppfylla de krocksäkerhetskrav som ställs på fordonet, spelar också styrka, töjning, material och deformationsmönster en kritisk roll. Lucids materialingenjörer och karosskonstruktörer samarbetade med AP&T:s processingenjörer och identifierade de material som bäst skulle kunna möta de krav som ställdes på komponenternas egenskaper.
Ett stort antal tester av olika höghållfasta aluminiumlegeringar från olika leverantörer genomfördes i AP&T:s testlinje i Ulricehamn, där de parametrar som materialleverantörerna rekommenderade implementerades i produktionsprocessen. I den här fasen av projektet definierades det optimala materialet, den optimala formningsprocessen och de optimala parametrarna för värmebehandling. Processens stabilitet vailderades genom en experimentell studie som inkluderade materialtester i leverantörernas laboratorier och omfattande komponenttester genomförda av Lucids materialingenjörer. De materialmodeller som behövdes för att genomföra FEM-simuleringar av kollisioner granskades av Lucids utvecklingsingenjörer. För att kalibrera modellerna fick Lucid materialprover från testtillverkade delar, som genomgått hela processen i AP&T:s produktionslinje.
Efter att de material som visat sig ha de bästa egenskaper valts ut tog AP&T fram prototypverktyg. Prototypdelar till Lucids Beta-prototyp och Release Candidate Cars som användes för ingående komponent- och fordonstester formades i AP&T:s produktionslinje. Delarna uppfyllde förväntningarna och AP&T fick förtroendet att gå vidare och fokusera på industrialiseringen av teknologin.
– Tack vare att vi använde våra FEM-simuleringsmodeller kunde vi snabbt ta steget till produktion. Simuleringsmodellerna, som optimerats i en rad forskningsprojekt, gjorde det möjligt att korta tiden för utprovning av verktyg radikalt. Det innebar i sin tur att vi kunde ta fram produktionsverktyg inom en mycket snäv tidsram, säger Dr. Michael Machhammer, Manager of Development Forming Processes & Tooling på AP&T.
Storskalig produktion – fischer Group engageras i samarbetet
Frågan var nu vem som kunde stå för den storskaliga komponenttillverkningen. Med goda erfarenheter av tidigare samarbeten, rekommenderade AP&T fischer Group, som en tillverkningspartner som kunde möta Lucids produktionskrav.
– Vår relation med AP&T sträcker sig 20 år tillbaka i tiden och vi utbyter ofta innovativa idéer om formningsprocesser med deras R&D-team. För ungefär sex år sedan presenterade AP&T fördelarna med varmformad aluminium vilket väckte vårt intresse för att dyka djupare in i teknologin. Vi letar kontinuerligt efter nya områden och applikationer där vi kan bidra med vår kunskap inom verktygsbaserad formning och vår expertis som leverantör till fordonsindustrin. Nu fick vi en möjlighet att göra precis det, säger Dr.-Ing. Stefan Geißler, Managing Director för fischer Hydroforming och Key Account Manager för samarbetet med AP&T och Lucid.
Med rätt partners på plats började AP&T och fischer Group planera för industriell produktion av Lucids komponenter vid fischers anläggning i Achern i södra Tyskland. Samtidigt som AP&T flyttade sin befintliga servohydrauliska press och verktyg till Achern, startade tillverkningen vid anläggningen i Ulricehamn för att hålla tempot uppe i projektet under överföringsperioden.
Lucid och AP&T arbetade också tillsammans med fischer för att modifiera vissa aspekter av värmebehandlingsparametrarna. Detta för att säkerställa att komponenterna skulle uppfylla specifikationerna och samtidigt vara möjliga att tillverka i stora volymer.
– AP&T:s och vårt team gjorde ett fantastiskt arbete tillsammans. I april 2021 hade vi ökat produktionskapaciteten i Ulricehamn till en nivå som gjorde möjligt att tillverka 1500 satser med dörringar, B-stolpar och batteripaketsskydd för Lucid Air, berättar Thorsten Junge, Head of Business Development på fischer Hydroforming.
Parallellt arbetade man intensivt med att förbereda anläggningen i Achern för installationen av den nya linjen och tillhörande utrustning för 3D-trimning, åldring och rengöring. En helt ny byggnad uppfördes för att få plats med allt.
– Vi såg också över inköpen av råmaterial. Även om det var en utmaning, blev slutresultatet en stor framgång. Linjen överfördes från Ulricehamn till Achern under sommaren och driftsattes i december 2021, säger Thorsten Junge.
Framtiden för hållbar mobilitet
När Lucid Air, en av de mest tekniskt sofistikerade elbilarna i världen, började levereras till kunderna i oktober 2021 fanns det anledning att fira, inte bara vid Lucids globala huvudkontor i Newark, Kalifornien, utan också i Achern och Ulricehamn.
Samarbetet mellan Lucid, AP&T och fischer Group blev en succé. En innovativ och lovande teknologi transformerades till en kommersiellt gångbar lösning, som skapar nya möjligheter för hela fordonsindustrin när det gäller att minska vikt och öka säkerhet.
Efter den framgångsrika lanseringen är efterfrågan på Lucid Air fortsatt stor, vilket också har ökat efterfrågan på komponenter i varmformad höghållfast aluminium.
– Nu handlar det om att fortsätta att optimera produktionsprocessen och öka tillverkningsvolymerna, vilket också kommer att ha en positiv effekt på lönsamheten, säger Robert Walton, Director of Purchasing på Lucid.
För att möta Lucids behov, har fischer långtgående planer på att starta tillverkning av höghållfasta aluminiumdelar med hjälp av innovativa formningsteknologier nära Lucids anläggning i Casa Grande, Arizona.
– Det är fantastiskt att få vara med på Lucids spännande resa och att våra tre företag tillsammans har förverkligat den första tillämpningen i världen i industriell skala av den här formningsteknologin, säger Stefan Geißler.
– Som etablerad partner till många aktörer inom automotiveindustrin möjliggör vi utvecklingen av en mer hållbar transportsektor med säkrare, energieffektivare fordon med lägre miljöpåverkan. Den här gången gör vi det med en innovativ teknologi i samarbete med en mycket framsynt biltillverkare. Det är stort, säger Christian Koroschetz.
Läs mer om Lucid Air
https://www.lucidmotors.com
Läs mer om AP&T:s lösning för varmformning av höghållfast aluminium
https://aptgroup.com/solutions/automotive/forming-high-strength-aluminum
Läs mer om fischer groups produkter av varmformad aluminium
https://www.fischer-group.com/en/products/aluminum-hotforming