Ett gäng pigga enkla experter i Köping med nya möjligheter för mekaniska konstruktioner. Med fyra rörlasrar i produktionen försörjer man stora delar av Sverige med rör idag under ledstjärnan – Snabbare på stålämnen.
Repaykoncernen, som startades i slutet på 1990 talet är idag en av Sveriges största och snabbast växande leverantörer av skurna rör och stålämnen. – Vi är bäst på att skära och kapa, berättar Joakim Klinga, Platsansvarig på Repay i Köping och vi skär med laser, gas och plasma på våra olika orter. Ledningen sitter i Skellefteå och vi har produktion i Kiruna, Gällivare, Skellefteå, Strömsund, Ludvika, Sala, Köping och Uddevalla. På Repay i Köping har man centraliserat rörbearbetningen. I dag har man fyra rörlasrar från TRUMPF – två stycken TruLaser Tube 5000 och två stycken TruLaser Tube 7000 från 2008 resp 2016.
Det var två killar från Skellefteå som 2001 startade med rörskärning i Arboga. Under åren har verksamheten vuxit och även flyttat till Köping. Med det geografiska läget säkerställer man snabba och kostnadseffektiva leveranser av både insatsmaterial och färdigskurna detaljer till kunder runt om i hela landet.
Snabb och prisvärd skärning för mekaniska konstruktioner
Rörlasertekniken öppnar helt nya möjligheter för mekaniska konstruktioner där man ofta kan minska antalet ingående detaljer i en ram genom att bygga in lösningar direkt i röret.
På så sätt blir produkten mer kostnadseffektiv och monteringen enklare.
Snabbhet och effektivitet genomsyrar tydligt hela företaget. Genom att tillverka sina produkter med kort ledtid på 10 – 14 dagar, minimera ställtid och ha ett högt materialutnyttjande ökar man konstant i omsättning och på de sista åren har den mer än fördubblats.
En vanlig artikel är tex rak-kapad med ett genomgående hål men det finns en oändlig mängd konstruktionsmöjligheter inom rör och så mycket mer man kan göra i en rörlaser än man tror.
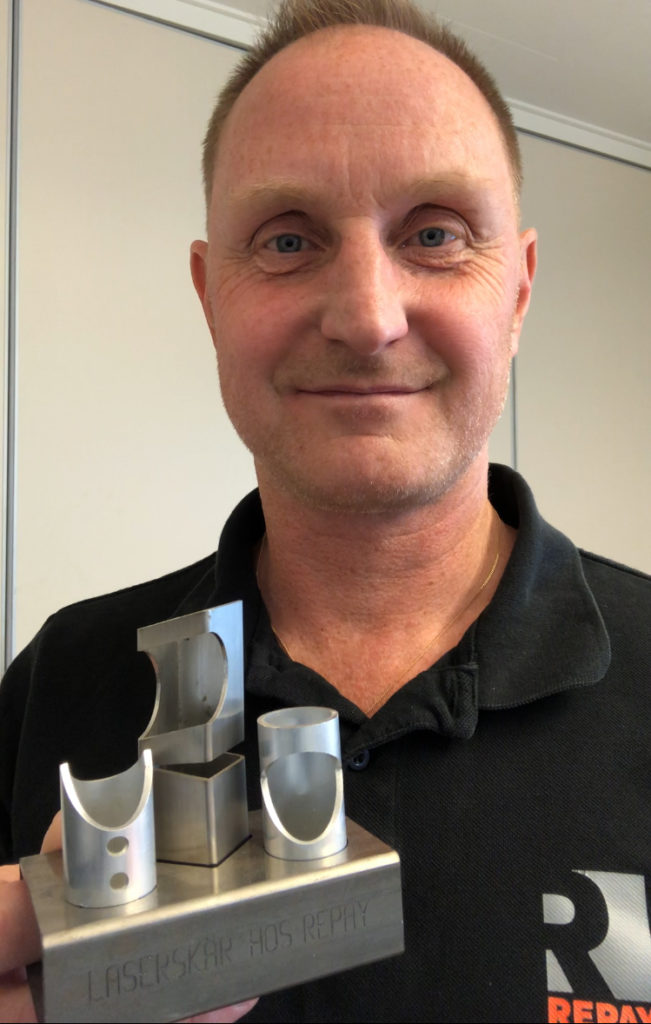
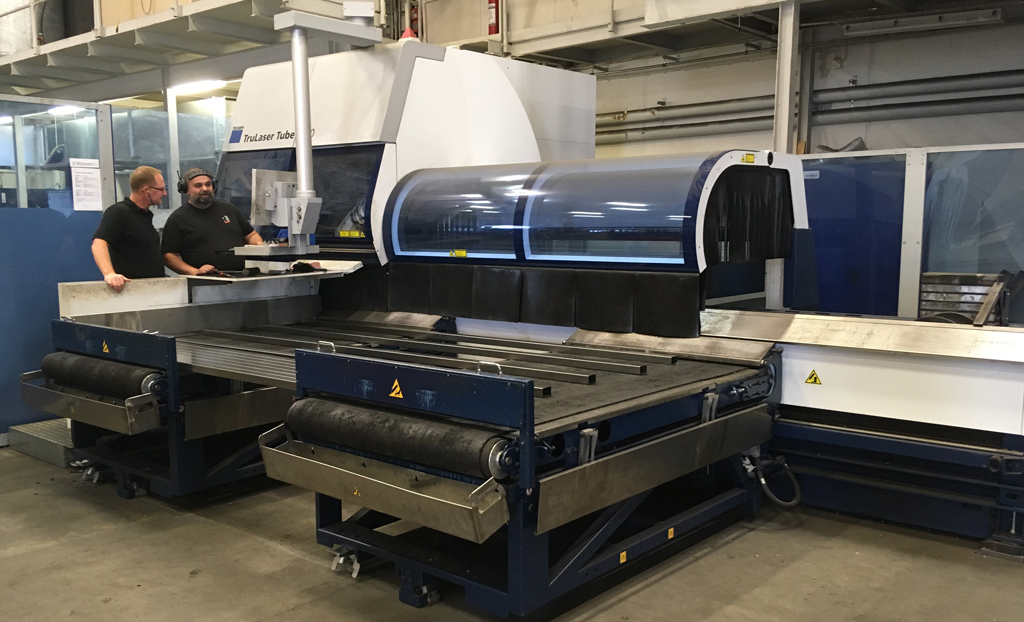
Beroende på vad hålen ska användas till skär man på en mängd olika sätt – ex med bevelcut (vinklat skärhuvud i 45 grader). Hålen kan skäras koniska, planskurna, vi skär tårbitsfunktioner som gör att man kan ”böja” röret, vi gör sidoanpassningar, kopplingar, styrtappar. Joakim visar en mängd olika demodetaljer. – Vi skär i ’svart’ kolstål, rostfritt och aluminium och kan skära upp till 250 mm i diameter där max vikten på rör är 37 kg / m, berättar Joakim. De minsta rör vi skär är 15 mm i diameter.
Delaktighet a och o
De skurna detaljerna märks och packas så att de kan levereras direkt in i kundens verksamhet. Kunderna idag är spridda från norr till söder i alla olika branscher, från ”att det rullar och går” till något som ska vara i en butik eller i en gruva, säger Joakim, och det är roligt och utvecklande. Joakim har varit med i företaget sedan 2005. – Vi är ett trivsamt gäng där alla hjälps åt och bidrar till att skapa en god Repay anda som vi hoppas smittar av sig till våra kunder. Vi har kul på jobbet och tack vare hårt jobb går det just nu bra i Köping, vi har även ett bra stöd från Repay centralt, säger han. Vår styrka är vår nyfikenhet, snabbhet och kostnadsmedvetenhet. Vi skär rör, kostnader och tid åt våra kunder.
Varje dag utvärderar vi produktionen och analyserar hur vi kan optimera flöde och teknik. Och vi alla är lika delaktiga i allt vi gör. Alla medarbetare har samma information och vi uppmuntrar verkligen till egna förslag och initiativ till förbättringar. Det är tillsammans som vi är starka. Med bra system kan vi följa varje maskin och inköpen är optimerade så vi vet exakt hur många artiklar vi kan skära ut från ett rör så att det blir minimalt med spill. Vi har en maskinpark som vi servar och underhåller själva så långt det bara går, vi har en mycket god planering av beläggningen där vi ser hur mycket jobb vi kan belägga i maskinerna, säger Joakim.
Det är ofta man är med redan i tidigt utvecklingsarbete hos kunden. Våra beredare är vanligt förekommande på kundbesöken så att vi kan skapa idéer gemensamt, säger Joakim. Det är så vi vill jobba så att kunden verkligen får vad de vill ha i slutändan. Snabbheten har vi i allt vi gör – inte bara leveranser utan även i att snabbt lämna offerter och ge feedback. Kunden ska alltid ha snabba besked så de kan planera sin egen produktion.
Två skift i maskinerna
12 personer arbetar i Köping och här kör man två skift. Beläggningen just nu är god och man har även bra samarbetspartners eller så finns möjligheten att gå upp ett skift till vid ytterligare behov. – Vi kan ju inte flytta våra jobb inom Repay som övriga koncernenen kan så vi har sett till att ha en bra backup till hands här, säger Joakim. År 2008 flyttade man in i nya större och bättre anpassade lokaler med ett genomtänkt flöde och bra genomfart. De fyra rörlasrarna står på rad med två traverser ovanför som förser dem med mtrl. TRUMPF maskiner finns det ett flertal inom Repay koncernen och TRUMPF rörlasrar har vi valt för att det är riktigt bra maskiner först och främst, säger Joakim. Det är bra programmeringssystem och det underlättar så klart med ett och samma system och en och samma serviceorganisation till hela verksamheten.
Maskinerna är stabila och med utvecklingen i de olika generationernas rörlasrar har vi lärt oss med tiden vad vi föredrar. Designen har ändrats lite under åren, exempelvis vad gäller utmatningen. Helt klart är vi mest nöjda med den sista TruLaser Tube 7000. Här är allt rätt. Smidig inmatning och utmatning och toppkvalitet i skärning. Den har maximal flexibilitet för stora rör. Vid den senaste maskininvesteringen står den först anställda av alla maskinoperatörer – Serif Saliji som varit i bolaget sedan 2001. Han är mycket nöjd med den senaste maskinen. – Den är snabbare än sin föregångare, det är kortare ställtider och vi kan göra så mycket mer i den. Utmatningen är väldigt bra. Maskinen är dessutom mer ergonomisk och användarvänlig på alla sätt.
Framtiden innehåller ljus och förhoppning med inslag av både mer personal, ännu bättre teknik och mer digitalisering. Vi vill naturligtvis in på mer digitalisering i framtiden, säger Joakim, vi vill ju utnyttja tekniken så optimalt man kan. – Vi vill bli effektivare i det vi gör hela tiden.
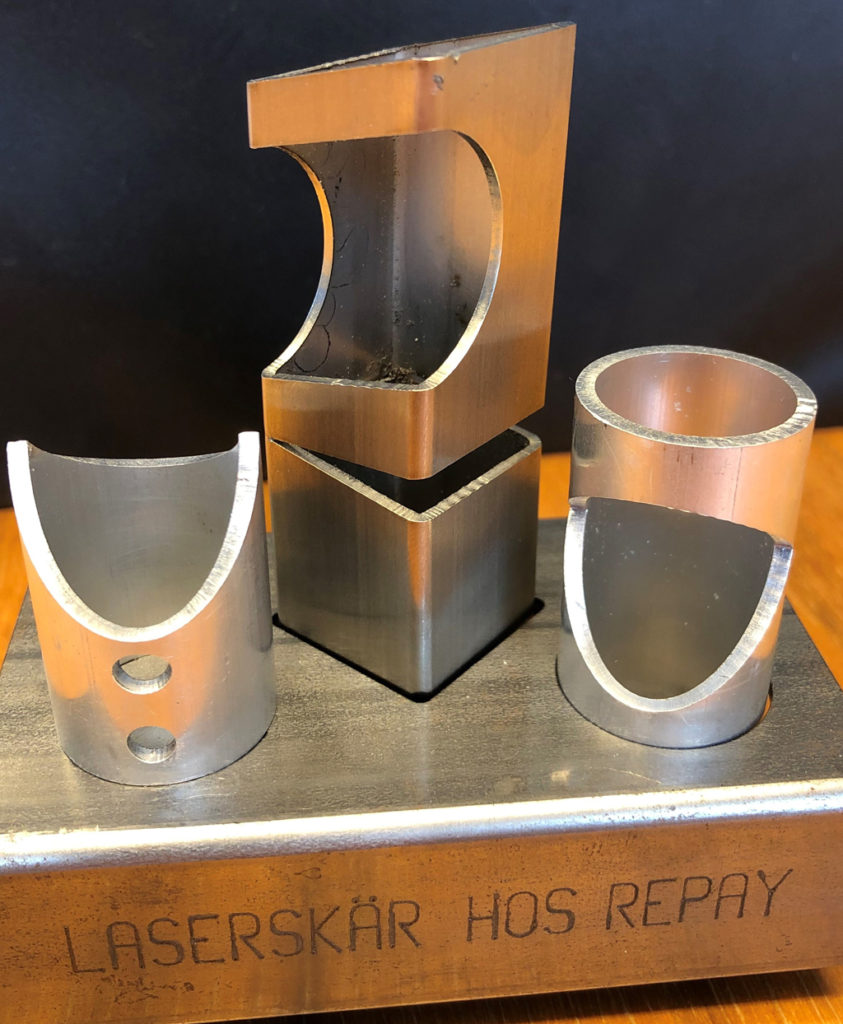