På fotot ser vi Frank Salazar Diaz, Joakim Öberg och Josef Axelsson
Scania introducerar nästa nivå av helelektriska nollemissionslastbilar, lösningar som passar för regionala tillämpningar. Med en installerad batterikapacitet på 624 kWh tillhandahåller Scania lösningar som ger förut¬sättningarna för att använda elektriska lastbilar även i regionala drifter och lastvikter upp till 64 ton. Det här tillskottet öppnar stora möjligheter för de åkerier som vill sätta sig i förarsätet och styra mot nollemissioner med en totalekonomi som matchar diesellastbilarnas prestanda. Och samtidigt kommer olika drivtekniker att utvecklas parallellt under lång tid framåt.
Ständiga förbättringsprojekt
avlöser varandra i produktionen.
För efterfrågan ökar inom transportsektorn.
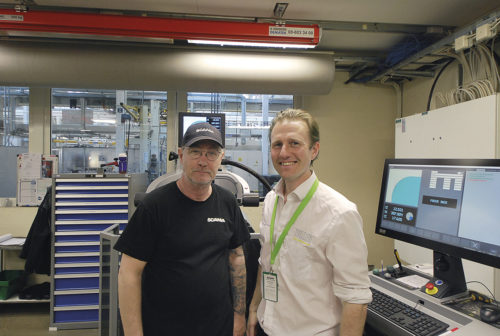
Scanias produktionssystem får anses vara en föregångare till många av de moderna tankegångarna som figurerar ute i den globala fordonsindustrin. Och man är kända för sina modulbaserade konstruktioner som ger kunderna stor valfrihet i sina inköp av produkter. Scania arbetar hårt med ständiga förbättringar som en del av sin företagsfilosofi, Scania Production System (SPS).
Dagens ämne i artikeln handlar om ett projekt drivet av Scania genom projektledare Joakim Öberg och ett team av fabrikstekniker. Förbättringsarbetet började för ett år sedan och handlar om att Scania bestämt sig för att införa en ny process – hårdfräsning – vilket krävde nya verktygslösningar och då vill man införa en optimal mätmetod för att säkerställa och kontrollera att skären alltid håller toleranserna i process och man vill också dokumentera alla mått och mätresultat i teknisk mjukvara, vilket ger mätteknikerna och produktionen rätt information för en optimal bearbetning utan ytproblem på vevaxeln.
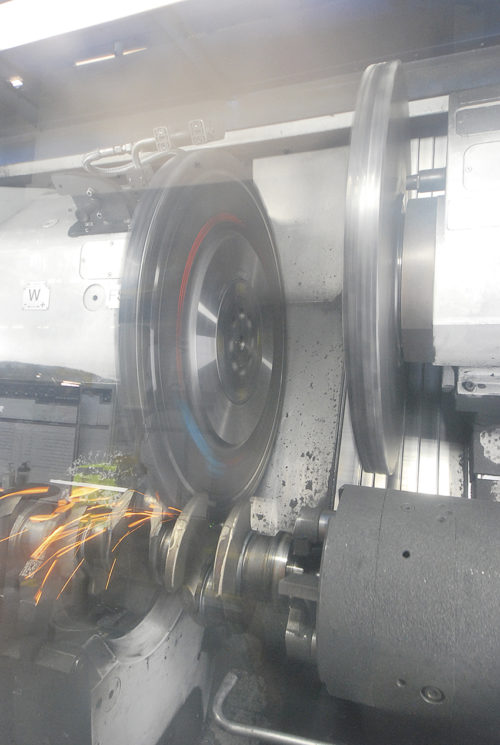
– Det är som du säger och krasst kan man säga att hittar man ett skär som är fel så behöver man byta alla skär på skivfräsen, det är beroende av de tuffa krav som vi lever med i fordonsindustrin, säger Joakim Öberg.
Och så går man också från bearbetningsmetod – mjukfräsning till hårdfräsning, vad är anledningen till det.
– Allt handlar om att man har gjort en designförändring på vevaxlarna, vilket handlar om att man tidigare fräste axlarna och sedan härdade man. Man har nu bestämt sig för att härda före fräsning och då resulterar detta i en ny hårdfräsningsprocess som ger ett bättre och starkare ytskikt på vevaxlarna, förklarar Joakim Öberg.
– Och för att kunna kontrollera skärens effektivitet och undvika skärbrott, så kan vi nu på ett snabbt och effektivt sätt arbeta med förinställningen och mäta in skären på skivfräsarna på ett optimalt sätt, säger en mycket nöjd mättekniker/operatör Peter Barbalics som säger;
– Vi har fått ner både ställtider och antalet ställ väsentligt. Och det sparar tid i kvalitetskontrollen.
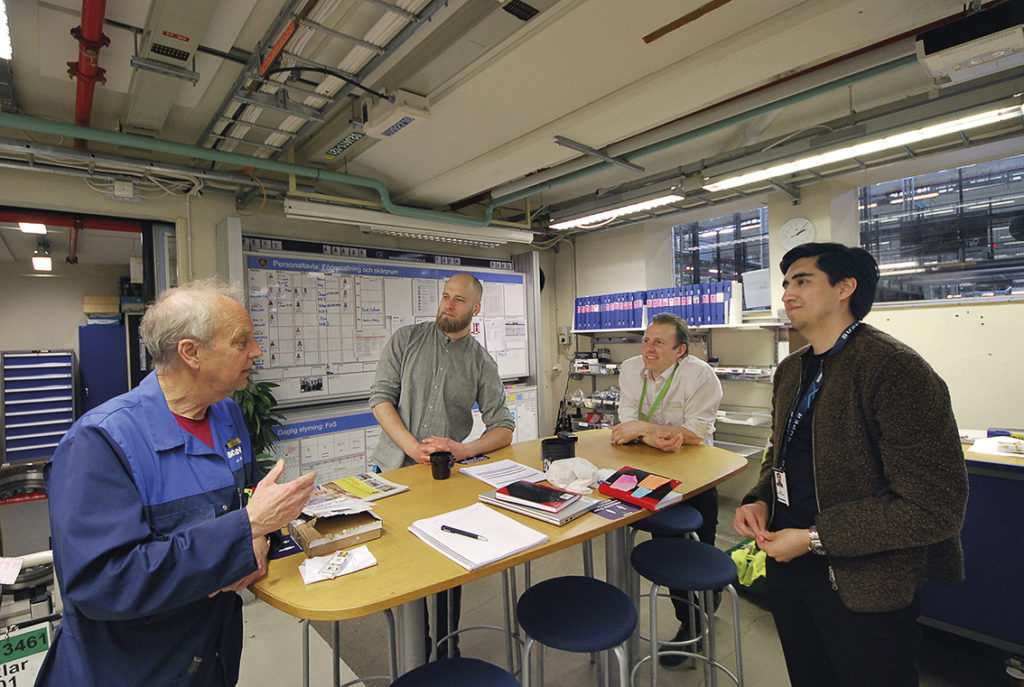
Massproduktionen tittar alltid mot klockan
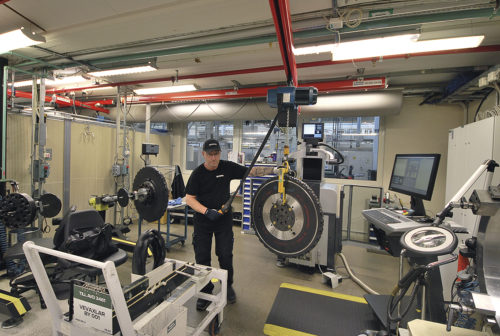
Vi hälsar i detta reportage på hos fordonsindustrin, vilket för mig som redaktör är en spännande värld av ny teknik som man inte alltid får inblick i. Mitt kontaktnät öppnar dörrar, så idag får vi åter möjligheten att besöka Scania i Södertälje. Många menar att det är främst fordonsindustri som driver på, när det handlar om utveckling av verktyg, maskinsystem och processer. Så för de företag som verkar i fordonsindustrin är det högsta teknikväxeln som gäller alla dagar i veckan och lite till.
Den snabba teknik- och samhällsutvecklingen gör att fordonsindustrin har att göra med en alltmer ökande komplexitet som leder till nya behov i form av utökade tekniska kunskaper inom de flesta teknikområden, utveckling av nya affärsmodeller och förändringar av organisationer och arbetssätt. Och som i sin tur leder till osäkerhet samtidigt som man måste veta vad man skall göra och ligga ett steg före när det bland annat handlar om framtidens drivsystem. Fordonsindustrin i Sverige behöver därför, för att kunna behålla sin internationella ställning, genomgå en kompetensomställning bland sina medarbetare. Och här konstaterar vi att Scania ligger bland de främsta i ledet.
På alla fabriker och verkstäder finns det alltid något att förbättra, stort som smått. När vi pratar riktigt stora tillverkningskomplex som Scania i Södertälje, så är det i kontinuitet, ständiga förbättringsprocesser igång och en utväxling i produktivitet som är imponerande. Men man kan inte hålla igång alla problemlösningar på en gång, det finns det inte personal eller resurser för, utan man måste ta akuta problem direkt, sedan får andra men identifierade problem, lösas efter hand som man har resurser.
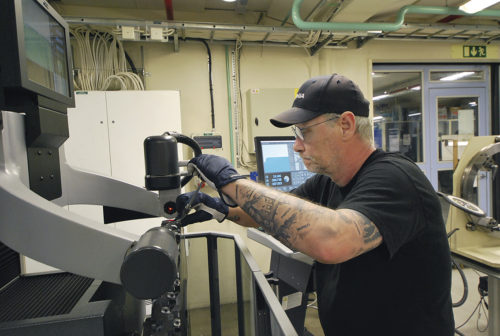
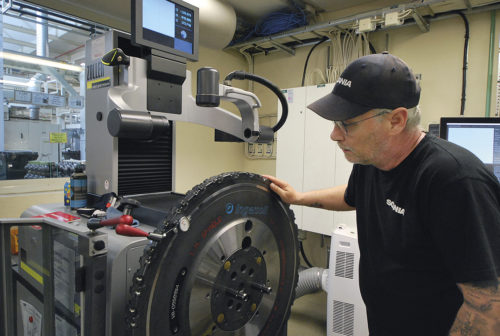
Ute i produktionen springer vi på ett känt ansikte, nämligen Lars Persé, den ständige förbättringsgeneralen med över 50 år i produktionen hos Scania. Det han inte vet om skärande bearbetning och processer, det tar han reda på.
– Vi lär oss nya saker varje dag och projekten avlöser varandra, så är vardagen i fordonsindustrin, högt tempo och utmanande målsättningar. Nya material och ny design och konstruktioner, gör att vi konstant behöver utforska nya processer för att bli bättre, snabbare och kostnadseffektiva, för tillverkning och produktion är levande och dynamiken ger produktivitetsförbättringar, konstaterar Lars och tillägger;
– Scania är ett fantastiskt företag att arbeta för och man satsar verkligen på produktion i Sverige till stora delar. Ta som här i Södertälje, där vi har flera produktionsenheter för tillverkning av vitala komponenter till lastbilarna.
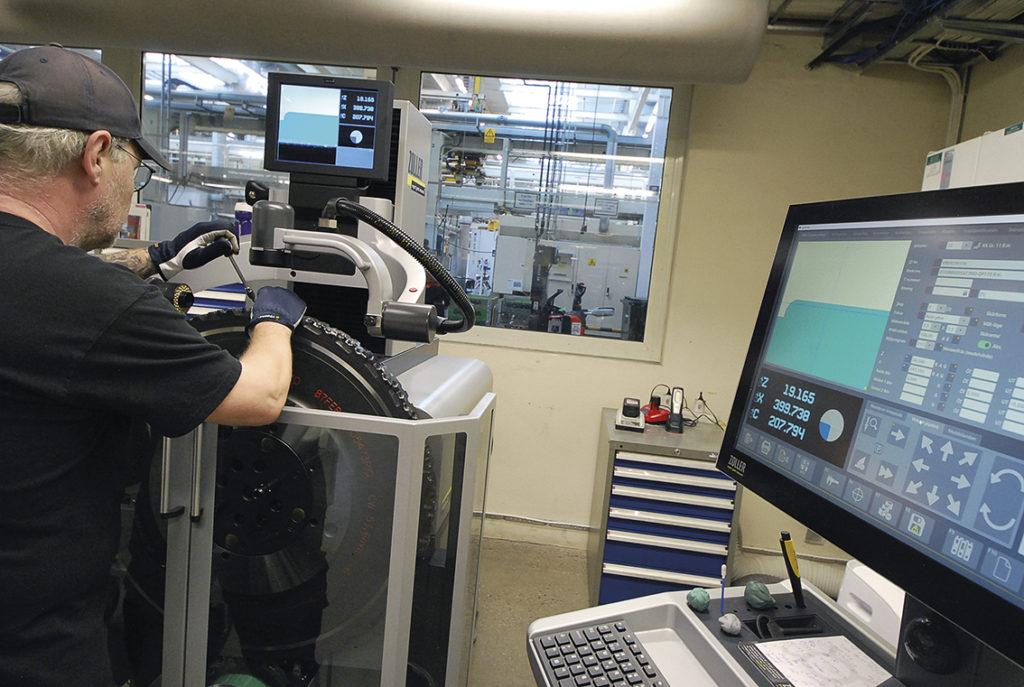
Ställ och verktygsinmätning
Projektledarna Joakim Öberg och Frank Salazar Diaz står och väntar på mig och Josef Axelsson på ZOLLER North Europe, för idag skall vi prata förinställning av skivfräsverktyg för vevaxeltillverkningen.
Josef Axelsson och hans medarbetare på ZOLLER North Europe och återförsäljaren GJS Verktyg är framgångsrika på den svenska marknaden, då försäljningen ökar för varje år.
Vi ber Josef beskriva den tyska tillverkarens produkter lite kort och sedan vill vi veta allt om mätmaskinen Gemini som nu är på plats i ställrummet hos Scania.
– ZOLLER har förinställningsmaskiner och verktygshanteringssystem för nästan alla ändamål.
ZOLLER Gemini är en standardmaskin speciellt utvecklad för att snabbt och enkelt kunna spänna upp och automatiskt mäta Scanias upp till 250 kg tunga skivfräsar. Alla skär som utgör diametern, bredden och radierna mellan diametern och bredden mäts. De skär som ligger utanför den förbestämda toleransen indikeras visuellt i mjukvaran och maskinen roterar skivfräsen automatiskt till rätt position för att justera skären. Det är en operatörsvänlig process som säkerställer att alla skären sitter korrekt innan skivfräsen sedan sätts upp i fräsmaskinen för att fräsa vevaxlar. Den största av Scanias fräsar har 288 stycken skär som mäts på tre minuter.
Hade Scania inte haft en Gemini och ett skär skulle legat ovanför toleransen skulle man ha monterat skivfräsen i fräsmaskinen i onödan, man skulle kört första bit (vevaxeln) skrot och man skulle fått plocka ner skivfräsen, tvättat den, demonterat alla skär, rengjort fräsen igen, monterat skären på nytt och hoppats att problemet löst sig inför nästa verktygsbyte.
Att mäta och veta att frässkären är korrekt monterade på fräsen sparar mycket tid och pengar för Scania. Så vi är väldigt glada att ha fått hjälpa Scania med den här mätmaskinen som en lösning till ett effektivt arbetssätt kring deras skivfräsar.
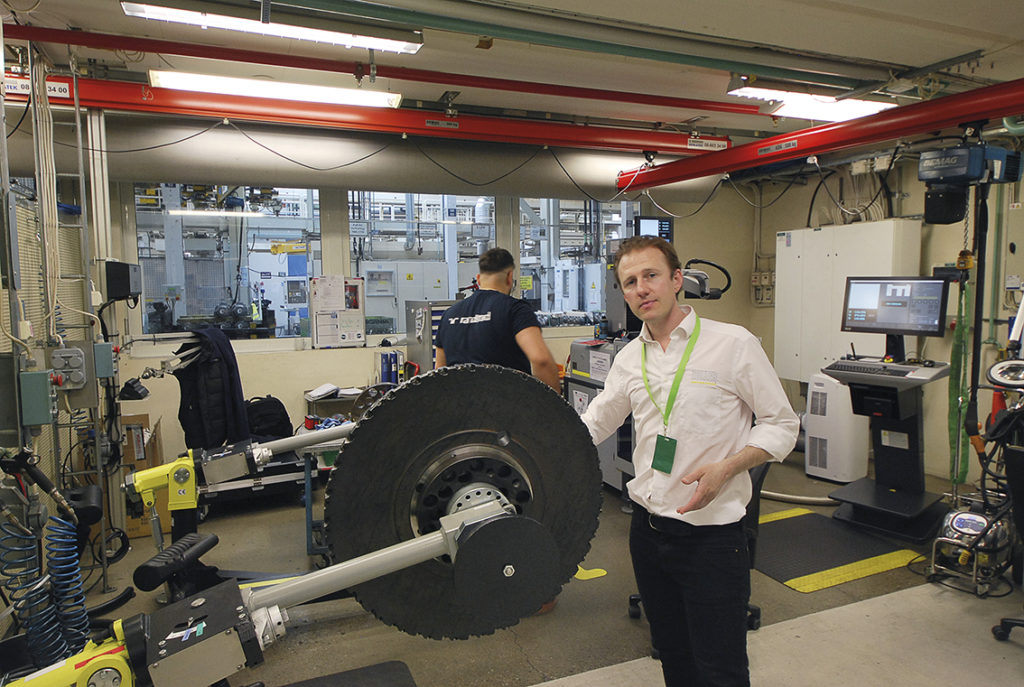
– Alla fräsar är utrustade med RFID chip från Balluff som kommer att överföra exakt mått på diameter och bredd till fräsmaskinerna. På chippet har vi också valt att lägga till en del extra funktioner för uppföljning för att få ett automatiskt meddelande när bytesintervallet för att byta skärskruvar är uppnått. Vi lagrar också vilket systerverktygsnummer som varje fräs har, vilken av fräsmaskinerna som fräsen har suttit i sist den användes, vem som förinställde fräsen, hur många gånger fräsen hittills använts under sin livscykel, när fräsen togs i bruk första gången och en del annan logik. Skulle inte skären gå sin fulla livslängd, utan operatören väljer att ta ut fräsen i förtid så loggas anledningen till detta tillsammans med all annan information från chippet. Det här gör att man sedan kan filtrera i databasen på all info som loggats från chippet och enkelt titta efter samband mellan gångerna fräsen inte gått full livslängd. – Uppstår det här problemet alltid från samma fräsmaskin? Bara från det här systerverktygsnumret? Alltid när intervallet för skärskruvarna håller på att uppnås?
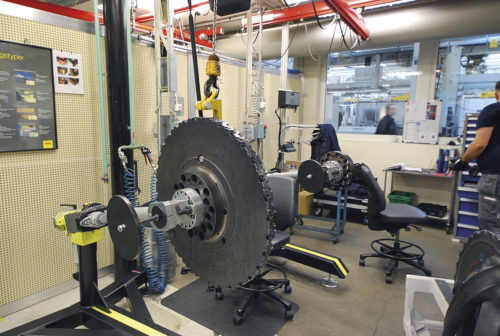
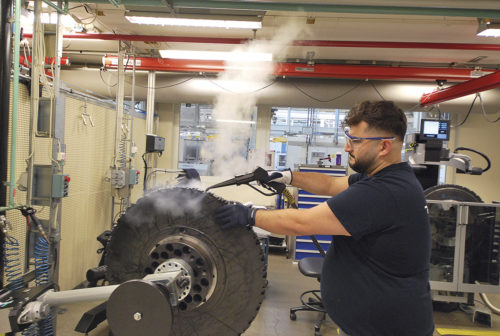
Med den här informationen och inbyggda logiken kan man enkelt analysera och förebygga verktygsproblem.
– Generellt för företag som väljer chip som databärare eller redan har chip är den här typen av logik enkel att lägga till och vi ser en ökad efterfrågan hos svenska företag förklarade Josef Axelsson.
Projektet har blivit mycket framgångsrikt och helt i enighet med de ständiga förbättringar som uppnås genom att Scania arbetar hårt som en del av sin företagsfilosofi, Scania Production System (SPS).
– Vi ser stora produktivitetsförbättringar i verktygslivslängd och en säkrare och bättre ytkvalitet på vevaxlarna genom att byta process. Material blir allt dyrare nu och i framtiden och genom att minska på inköp av antalet skär, bidrar vi till ett alltmer hållbart samhälle, säger projektledare Joakim Öberg och ansvarig produktionstekniker Frank Salazar Diaz på Scania i Södertälje.
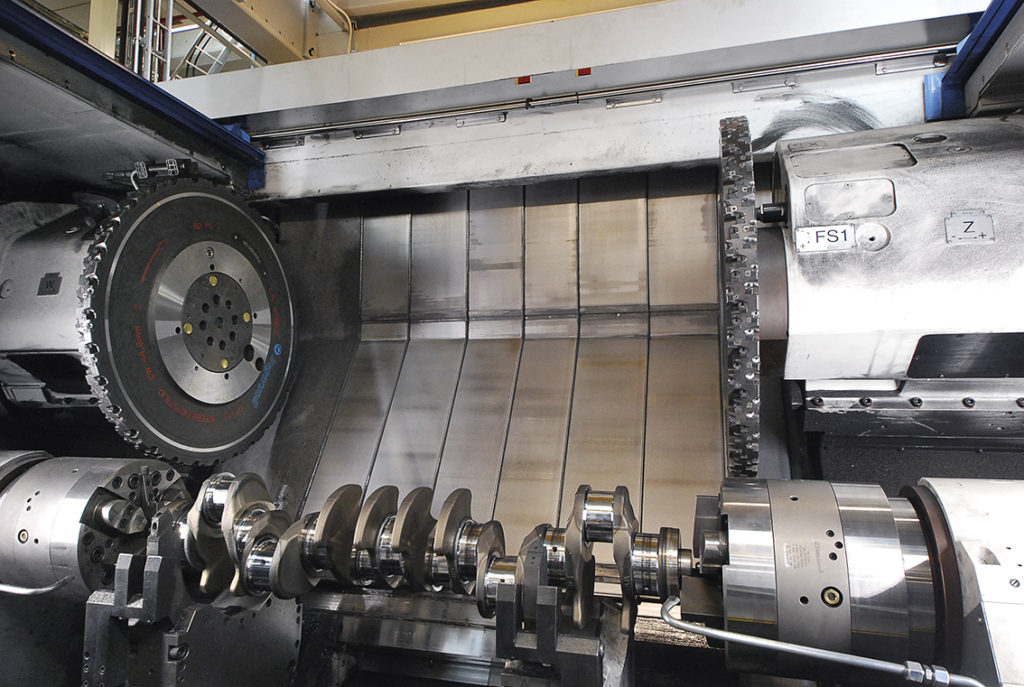
Teknikskifte / bearbetning – från mjukfräsning till hårdfräsning
I alla förbättringsprojekt finns flera ingredienser. Vad vi behöver veta för att få hela bilden i projektet, så fanns ett behov av att hitta nya fräsverktyg och nya skärsorter för att få till en komplett lösning. Den tyska verktygstillverkaren INGERSOLL Werkzeuge GmbH bistod med tekniskt kunnande och verktygslösningar genom sina i Sverige anställda Key Account/applikationstekniker Anders Sunnemalm och Per-Anders Fransson.
Ge mig era upplevelser och verktygsvalen
– Efter en första provfräsning på vårt ”Ingersoll Technology Center” genomfördes en bearbetningstävling på befintliga vevaxlar hos maskintillverkaren.
Baserat på resultaten valdes Ingersoll ut som ”Preferred Supplier” för projektet.
Vändskären är anpassad belagd keramik för härdad bearbetning. Val av antal vändskär baseras på bl.a. ekonomi, skärförlopp och processäkerhet.
Utmaningar hårdfräsning
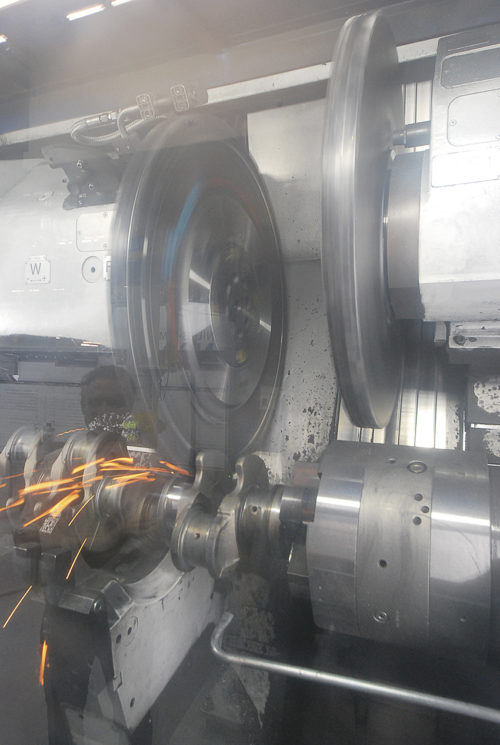
Med tanke på vevaxelns hårdhet måste följande beaktas: Värmeutveckling som vändskären utsätts för under skärförloppet i och med torrbearbetningsprocessen.
Eventuell temperaturhöjning av vevaxeln under bearbetning. Härdade spån som angriper verktygskroppen. Anpassat skärmaterial lämpligt för hårdbearbetning.
I början av projektet genomfördes provbearbetning på originalhärdade Scania-vevaxlar för att förhindra att kunden skulle undvika korrigeringar i efterhand.
Här pratar vi förstås massproduktion, vad är fordonsindustrins utmaningar och hur påverkar det verktygsval.
– Vi talar om eliminering av förslipning, den slutliga finishen görs fortfarande genom precisionsslipning.
Avvikelser efter härdning i vevaxlar i bilstorlek är lägre; i vevaxlar av lastbilsstorlek med större avvikelser ser vi huvudområdet för hårdfräsning.
De främsta fördelarna är uppenbara under hela tillverkningsprocessen. Hårdfräsningsprocessen är mer kostnadseffektiv att investera i och mer miljövänlig, eftersom det inte krävs något kylande smörjmedel för bearbetningsprocessen.
INGERSOLLs uppdrag i Sverige är att etablera befintliga högkvalitativa produkter och servicen hos våra svenska kunder. Vi har nu direkt support på den svenska marknaden och kommer att utöka denna tjänst i framtiden, avslutar Anders Sunnemalm.