Tillverkningsindustrin upplever en våg av investeringar i automation och ny maskinteknik som man historiskt sett inte upplevt tidigare. Vi är mitt inne i olika digitaliseringsprocesser och Industri 4.0 som driver produktivitet och effektivitet framåt. Svensk industri blir allt smartare för varje dag.
Detta har det skrivits om i många artiklar i tidningen de senaste åren. Produktiviteten måste förbättras för svag produktivitet drar ner den potentiella tillväxten som finns i många företag.
Företag som förädlar plåt måste automatisera, det är nästan enda chansen för dem att ha kvar produktion i ”högkostnadslandet” Sverige och klara jobben. Och vi är på rätt väg. Sverige är bland de ledande i världen hur man investerar i olika automationslösningar inom alla typer av maskinteknik. Alla moment går att automatisera idag och med nya mjukvaror och IT-lösningar ökar även digitaliseringen i industrin.
Man får även en kvalitetshöjning med automatiserad produktion på sina artiklar. Antingen blir alla fel eller alla rätt och jämför vi med en manuellt betjänad maskin oavsett vad det är för maskinteknik, så är den mänskliga faktorn alltid där på varje detalj.
Tidningens redaktion har varit här och skrivit om maskininvesteringar några gånger tidigare och vi pratar om Kvänumfabriken som är den största av Swegons fem fabriker. Här tillverkas luftbehandlingsaggregat och mitt på ”Västgöta slätta”, i ett område känt för sina expanderande plåtindustrier, ligger Kvänumfabriken. Här har Swegon tillverkat och levererat luftbehandlingsaggregat i mer än 50 år. Den stora produktionsenheten tar mer än 36 000 kvm i anspråk och här arbetar 350 personer.
Medarbetarna på produktionsanläggning i Kvänum har lång erfarenhet av hur man med teknik och kompetens skapar de rätta förutsättningarna för en effektiv produktion.
– Vi måste alltid ligga i framkant av utvecklingen och vårt nytänkande tillsammans med våra maskinleverantörer gör att vi är ledande i världen när det gäller lösningar för att effektivt tillverka luftbehandlingsaggregat som sedan exporteras över hela världen, säger produktionstekniker Michael Gustafsson.
Fabriken i Kvänum tillverkar luftbehandlingsaggregat, huvudsakligen för klimatanläggningar och energiåtervinningssystem. Traditionellt så har man inte stora serier utan arbetar med korta serier med många variationer och denna typ av produktion har vuxit fram i framförallt Skandinavien. Så här är all produktion högt automatiserad. Nu skriver vi in 2021 och resan fortsätter mot den allt smartare fabriken,
…. och nu skall vi nu ha i minnet att 99 % är enstycksproduktion idag, säger Michael Gustafsson.
Vi sitter och diskuterar med två experter, Michael Gustafsson produktionstekniker på Swegon och Pelle Wallin maskinsäljare på Salvagnini Scandinavia om ämnen som effektivisering – digitalisering – automatisering.
Först en presentation av grabbarna. Michael Gustafsson har arbetat på Swegon sedan 2001. Han arbetar med produktionsteknik inom ett område som kallas Team maskin. Här samlas kompetens från flera tekniker och teams och tillsammans ser man till att alla produktionsprocesser fungerar tillsammans inom då maskin, logistik och montering. Michael är också projektledare för den senaste teknikutvecklingen och skall längre fram berätta om fler anledningar till att man nu gjort denna rekordinvestering i fabriken i Kvänum.
Maskinsäljare Pelle Wallin; Tidningens redaktör känner dig väl men kan du presentera dig för läsarna.
– Har gått den ”långa vägen”. Min första kontakt med plåt, efter att i högstadiet ha sommarjobbat på Hoks Mekaniska, var att montera pulverlackeringsanläggningar främst i dåvarande Tjeckoslovakien och när jag inte var ute på fältet så blev det lite bockning av plåt och svetsning mm. – 1989 började jag som servicetekniker på Salvagnini. Jag kom att arbeta som servicetekniker, utbildare och med projektarbeten mm fram till 2008, då tog jag en paus från plåtvärlden och jobbade med försäljning av träbearbetningsmaskiner och av bearbetad grafit för att sedan 2013 återvända till plåtbearbetningsvärlden igen och börja arbeta med försäljning på Salvagnini.
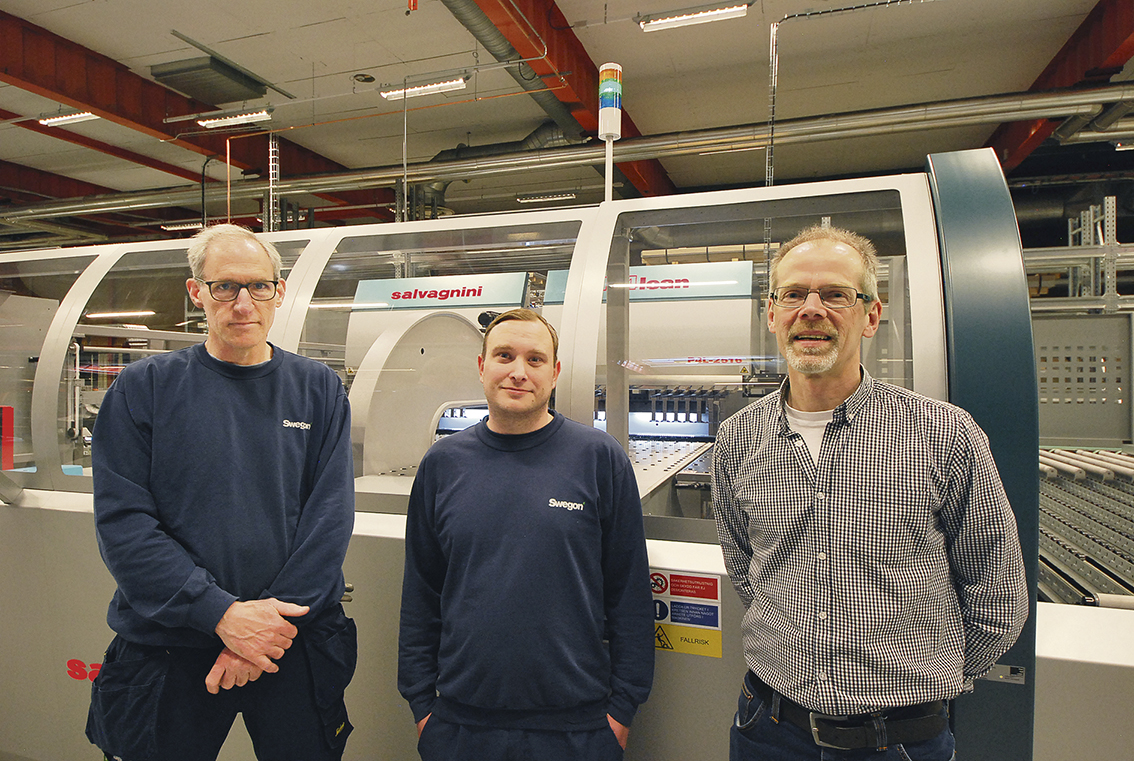
Ut i verkstaden
– I vår bransch är det en ständig press på effektivitet, att tillverka dels ”Just in Time” och med allt kortare ledtider, som bottnar i våra kunders krav i sin tur, för att Swegon skall kunna leverera ventilationsprodukter ut till marknaden och då behöver vi en maskinpark som matchar våra behov, utifrån en ökad orderingång, förklarar Michael Gustafsson på Swegon.
– ”Ljuv musik” för oss som arbetar för och med den italienska maskinbyggaren Salvagnini som har ett DNA där det handlar om att erbjuda effektiva maskinlösningar allt från ”stand-alone” maskiner till halv- och helt automatiserade maskinsystem i produktionslinjer, där man endast tillverkar exakt vad man behöver, mer eller mindre på ett så flexibelt sätt som möjligt och utan ställtider, så automatiserat som möjligt, säger maskinsäljare Pelle Wallin på Salvagnini Scandinavia.
Svensk industri lever i en hårt konkurrensutsatt värld, varje dag och här har Swegons fabrik i Kvänum, under en längre tid tillsammans med flera olika maskinleverantörer byggt upp en effektiv produktionsapparat. Och i detta fall idag med den senaste investeringen som vi uppmärksammar så är det maskinleverantören Salvagnini Scandinavia som installerat och anpassat produktionsutrustningen.
– Allt för att klara de framtida ökade beställningar och orderrader som är kopplat till vårt digitaliserade affärssystem. Vi tar marknadsandelar tack vare vår effektiva produktionsapparat, där vår kompetenta personal och effektiva tillverkningsprocesser tillsammans skapar framgång, säger Michael Gustafsson.
Produktionsfilosofi, planering, framtida ökade volymer och digitaliseringsbehov skapar behov av maskininvesteringar
– Projektet startade för 2 år sedan då vi gjorde en arbetsplan med en ordentlig benchmarking, där vi scannade marknaden för att se hur de olika maskinleverantörerna resonerade kring våra krav. Och projektet grundades också i det man kan säga är en investeringsplan i maskinparken. Vi tittar då och då på hur vår maskinpark fungerar, antal år i produktion, tillgänglighet och om vi behöver ny teknik, säger Michael och fortsätter;
– Vi såg här att vår äldre produktionslinje från 1999 som renoverades för 6 år sedan för ett antal miljoner, började ”tappa fart” eller skall vi säga vi behövde ny maskinteknik för att öka vår kapacitet helt enkelt. Så då såg vi det som ett lämpligt tillfälle att börja vårt projekt med att nyinvestera i en högt automatiserad plåtbearbetningsmaskin-system.
– Vi hade uppe flera olika alternativ och upplägg. Men vi fastnade för Salvagnini som har utrustningar här sedan många år tillbaka och där vi är nöjda med service och support, så vi gjorde vår hemläxa bra, säger Michael.
– Fler och fler av våra kunder kommer idag med ett produktionsbehov och inte ett maskinbehov i första stadiet. Att tillsammans ta fram en lösning i ett nära samarbete där målet alltid måste vara att slutresultatet blir en optimalt fungerande anläggning som motsvarar kundens enskilda krav och behov, menar Pelle Wallin.
– Vad som är både spännande och produktivt med den nya linjen är att vi har investerat i tre materialtorn för att dels få tillgång till olika plåtformat och eftersom materialflödet i volymtillverkningen är ett 1-stycks flöde innebär detta, ett utgångsämne är lika med en detalj och eftersom materialet växlar mellan Alu-zink och för lackerad plåt med intervall – med en av två. Så jämfört med existerande linjer från Salvagnini att vi går från två till tre torn och får 16 st ytterligare grundformat att välja på för att kunna optimera spillprocenten ytterligare och på detta vis sparas pengar i materialåtgång.
Kitproduktion olika varje gång
– Även om vi har en stor variantflora så inte nog med det staplar vi även många olika kombinationer där vissa paneler förekommer i flera olika kit med olika sekvenser och tex olika staplingsvinklar mm.
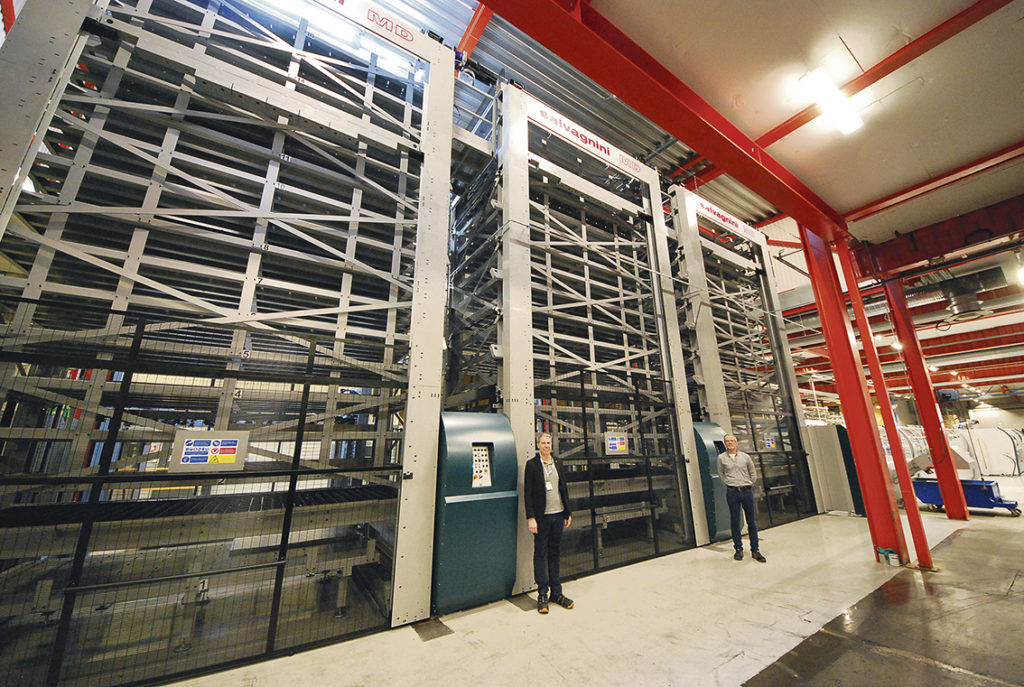
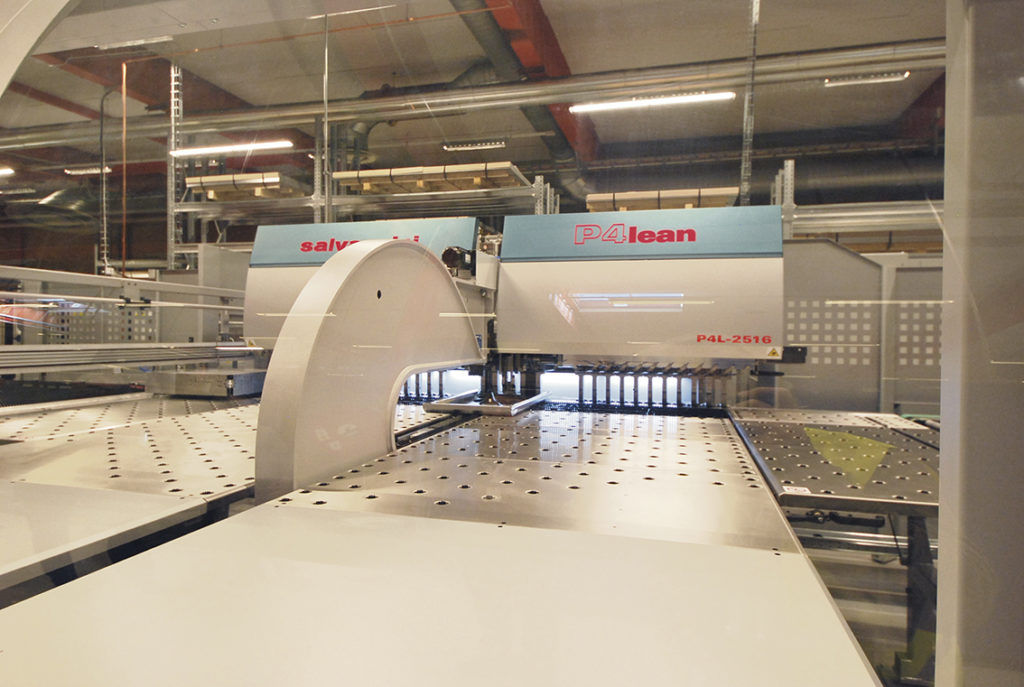
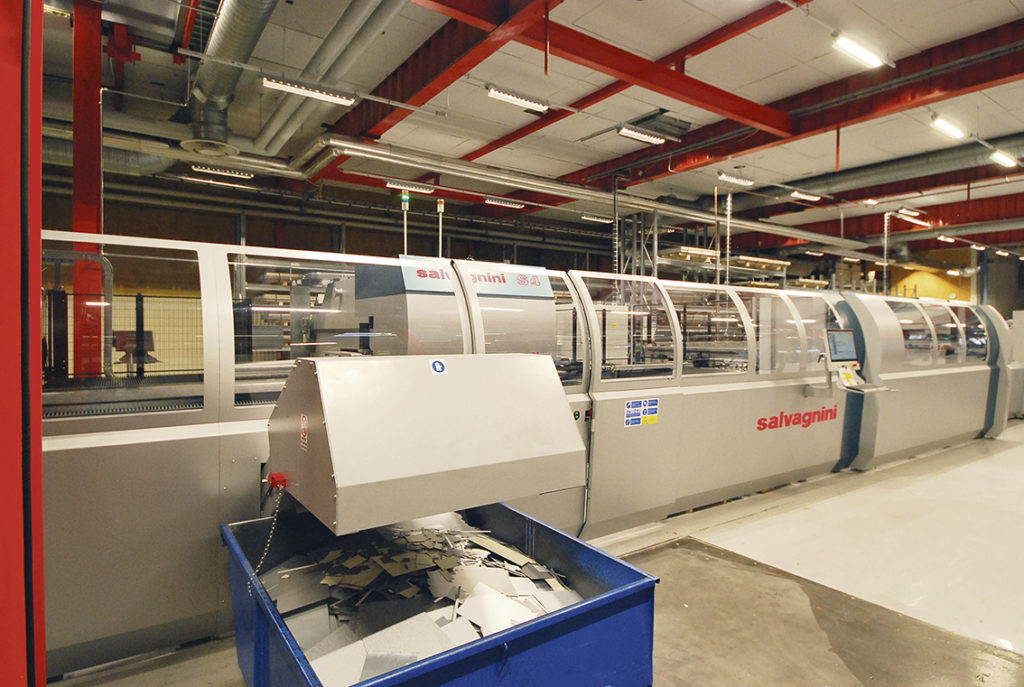
Minskat plåtspill
Man pratar ofta om att ha en effektiv nesting, här fungerar det på ett lite annorlunda sätt, förklara Pelle.
– Eftersom den stora tillverkningsvolymen produceras i enstycksflöde med Alu-zink material varvat med förlackerad Alu-zink, dvs. innerpanel obehandlad och ytterpanel färdigmålad utan skyddsfolie. Så det enda vi använder nestingen till är att fördela ut netto och bruttoskillnaden av utgångsämnet och den färdiga detaljen korrekta utbredningar där vi alltid börjar med 3D ritningen för att få rätt utbredning i stansmaskinen.
– Nesting för att programmera, när man producerar större batcher än enstyck fungerar, genom att mjukvaran (StreamNest) lägger ut ämnen på de utgångsformaten som ger minst plåtspill och kan vara multipler eller fri nesting, den enda begränsningen är att man måste hålla sig till samma materialkvalitet.
Vad det gäller digitaliseringen mellan Salvagnini och Swegon. Så sker detta i två steg. Vi har gemensamt utfört ett pilotprojekt, steg 1 (på Salvagninis språk L-Bit) för ett planeringssystem av produktionssekvensen av 3 dagars produktion med utgångspunkt att aggregat monteringen drar hela flödet genom fabriken. Planringsmjukvaran samarbetar med informationen som finns i Swegons monterings stöd mjukvara, Casat. L-Bit talar om med hjälp av data i Casat vilket som är den mest fördelaktiga monteringssekvensen för att undvika flaskhalsar och komponentbrist. Men det kan även tala om att med vald produktionsplanering behövs extra resurser vissa klockslag mm. För produktionstekniker så kan man se vad belastning blir på var monteringsstation osv. Verktyget har används i skarp produktion i ca 6 månader. L-Bit sätter produktionssekvensen i affärssystemet innan produktionsorderna släpps för produktion.
Steg 2 i digitaliseringen görs via Salvagnini OPS (som är Salvagninis namn på kopplingen mellan kundens affärssystem och Salvagnini systemen som har förfinats sedan första leveransen till GE 1985) innehåller fullständig kontroll av råmaterial och deras interna transporter till de 3 Salvagnini linjerna. Produktionsflödes optimering av de tre linjerna med hänsyn taget till aktiv produktions kö jämfört med kvarvarande monteringstid i panelbufferten och minimering av skrotprocent per kit. Kitten kommer att vara staplade på lastbärare som har programmerbar RFID och elektroniska hyllkantsetiketter för enkel information om plastbärarens innehåll. Alla transporter mellan de 3 linjerna och de olika panel buffertlagren kommer att styras av Salvagnini OPS. Steg 2 kommer att var fullt implementerat i alla tre linjer inom ca ett år. Då finns det en anledning att återkomma och göra ett uppföljande digitalisering reportage.
Vi ber som alltid om tekniska fakta, Pelle Wallin ger oss den informationen;
– Linjen börjar med tre höglager som har 16 hyllplatser med max 3 ton material per plats, I extrema fall kan även inmatningsbordet mata maskinen direkt utan att mellanlagra formatet i lagret. Stansmaskinen är vår beprövade modell med inbyggd vinkelsax och 50 stansstationer som alltid är stansberedda, dvs vi växlar inte verktyg. Med integrerad vinkelsax. För att maskinen ska producera paneler så har vi ingen staplingsstation utan efter stansen så kommer RIP plåtvändaren för att få eventuella grader in i panelen samt förlackerad plåt att komma med lacken på undersidan i panelbocken.
– ACP förcentrering bord innan P4L-2516 som är utrustad med RBU, en borste som rengörplåtarna innan plåten centreras. Dessutom rengörs bockverktygen med tillbehöret PSE mellan varannan plåt för att inte få beläggning från Alu-zink materialet på bockverktygen. För att klara att hålla bockvinklarna inom tolerans, även på det mest krävande profilerna så används MAC 2.0 som i realtid kompenserar skillnader i materialhårdhet. En oförstörande process, då vi mäter innan första bocken är färdigbockad och applicerar eventuella korrektioner på sista delen av bockvinkeln. Maskinen är utrustad med ABA för att ställa om panelstorleken mellan var panel utan cykeltidspåverkan.
– SAR kallas vår robotstaplingslösning som är en standardmodul med interaktiv automatisk stapling via mjukvaran ConnectionManager. CM läser av den geometriska information från P4 programmet och med hjälp av detta så anpassas gripdonets konfigurering och rörelsemönster automatiskt. Men för Swegons räkning så finns ett antal anpassningar jämfört med standardutgåvan. Dels hanteringen av kit lastbärarna som påverkar staplingsbeteendet och möjlighet till flexibel linjärstapling. En av utmaningarna har varit att staplingsordningen inte sker i fallande storleksordning utan strikt efter monterings sekvens. Samt att man oftast vänder varannan panel för att inte få onödiga repor på panelerna. För att kompensera detta staplas kitten på pallar med sidostöd och ett automatiskt lutande plan. Det finns plats för fyra ostaplade pallar och fyra staplade pallar innan man måste ta hand om pallarna in och ut ur linjen.
Swegon har nu en
nyckelfärdig lösning för framtiden.
– Att kunna leverera automatiserade och komplexa lösningar har alltid varit och är maskintillverkaren Salvagninis ledstjärna gärna som en helhetslösning. Man siktar hela tiden mot att inte ha något som helst manuellt ställ. Att under löpande produktion snabbt kunna ställa om maskinerna med automatik, där fasta program i olika varianter ligger i en databas och operatören kan enkelt styra produktionen efter kundernas beställningar,” allt sker i ett enda flöde, i sekvens och styrs efter vad man skall leverera till monteringen.
Projektledare och produktionstekniker Michael Gustafsson får sista ordet;
– Vi försöker att automatisera så långt det går och när det jobbet är gjort så försöker vi lite till. Så för en automationsivrare som Swegon är, så är denna investering en dröm att dagligen utveckla och arbeta med ständiga förbättringar MEN utan att det blir för komplext. Vi skall inte överautomatisera.
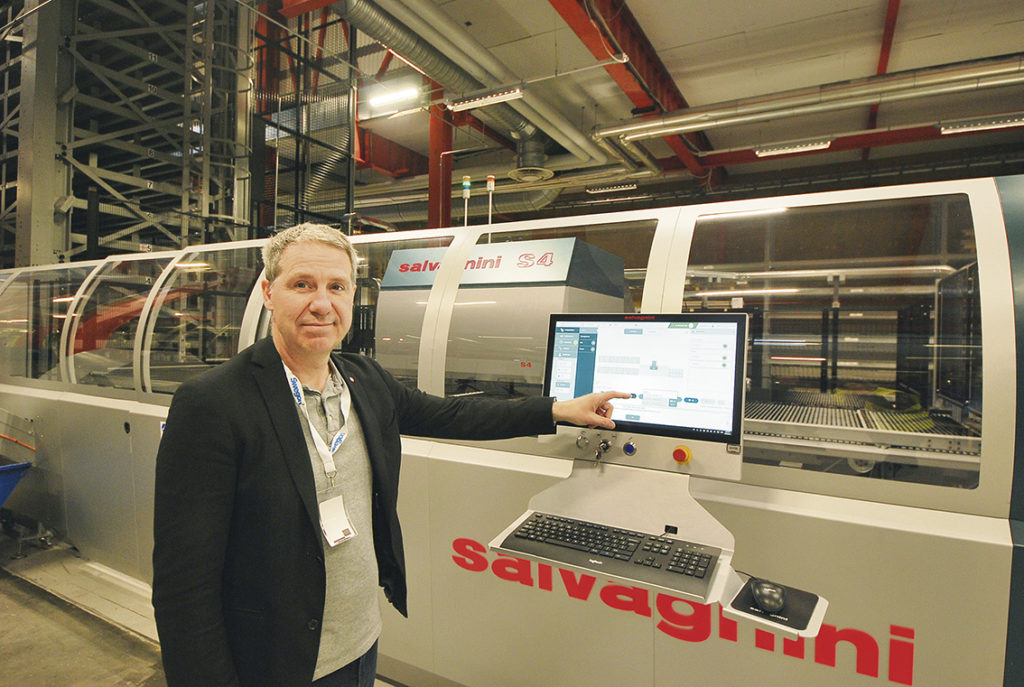
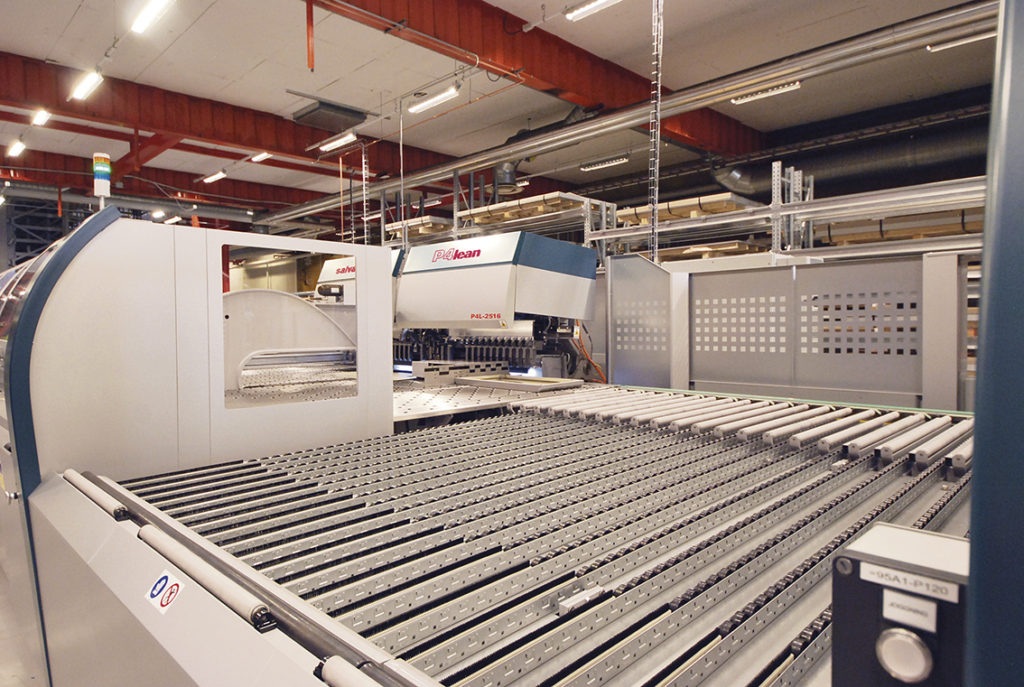
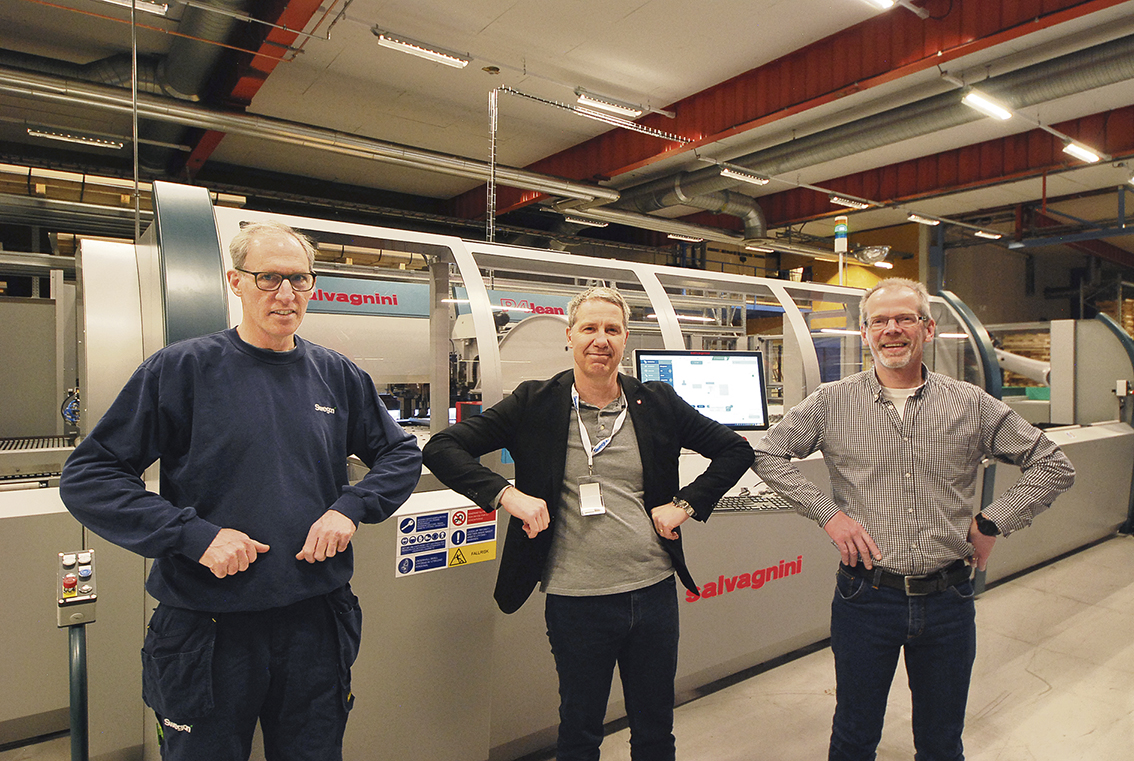
– OCH om man ser tillbaka här i fabriken så skulle automationen vara visuell. Operatörerna skulle kunna följa produktionen, visuella buffertar osv.
– Nu går vi ifrån det, talar om att nu är det ”systemet” som skall ”se”. Digitala produktionssystem som är självtänkande ger bättre förutsättningar att kunna optimera ännu mer. Produktionsmixen blir allt mer komplex och varierad, så det behövs ett produktsystem som supportar operatörerna i deras beslut
– Vi har fått nu upp farten men det är några steg kvar till det helt digitaliserade maskinsystemet.
– Vår strategi fungerar och anläggningen går idag i tre skift som är schemalagd. Här på Swegon är det en ständig produktutveckling med tillkommande varianter och löpande processförbättringar, så nu har vi en tillverkningscell som vi styr efter vad vi skall leverera till kund, säger Michael Gustafsson och han ser mycket nöjd ut.
Redaktörens spaning
Så här får nu medarbetarna en roll som övervakare av systemet. För trots allt så människan överlägsen den största datorn som man kan bygga men då handlar det om andra parametrar som att hitta och separera mönster, snabbt ändra sig, då en dator inte kan ändra ett av sina program hur som helst mm. Och AI artificiell intelligens saknar en förmåga till såväl kreativitet i nuet samt kunna formulera en helhetssyn.
Och datorer är naturligtvis konstruerade av människor och fungerar i enlighet med de instruktioner som programmeras in. Datorer behövs men människan är fortfarande överlägsen.
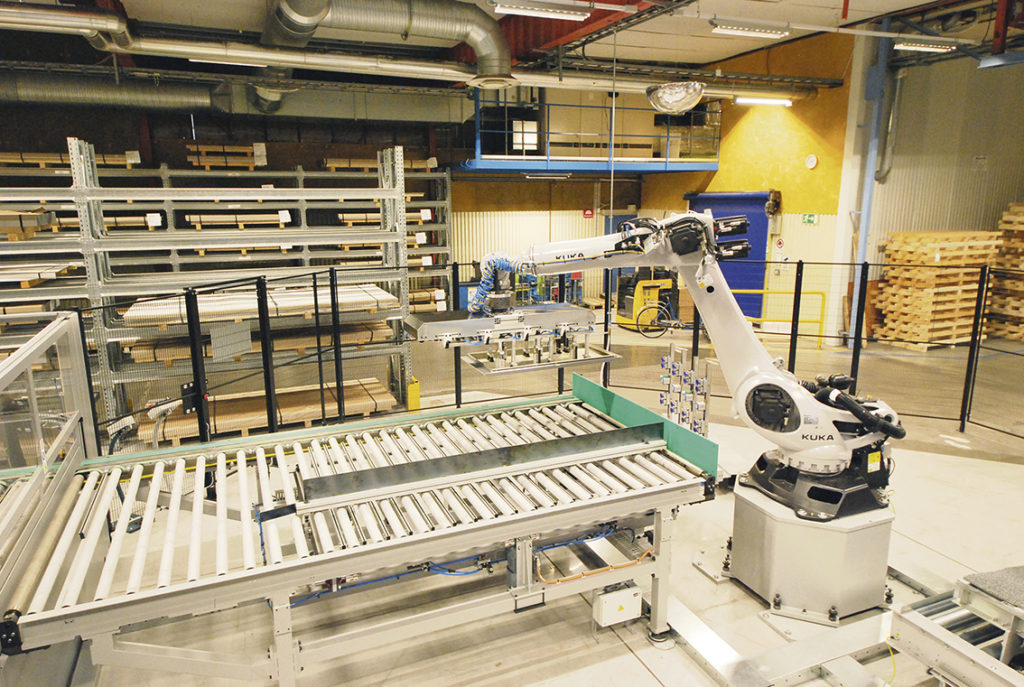
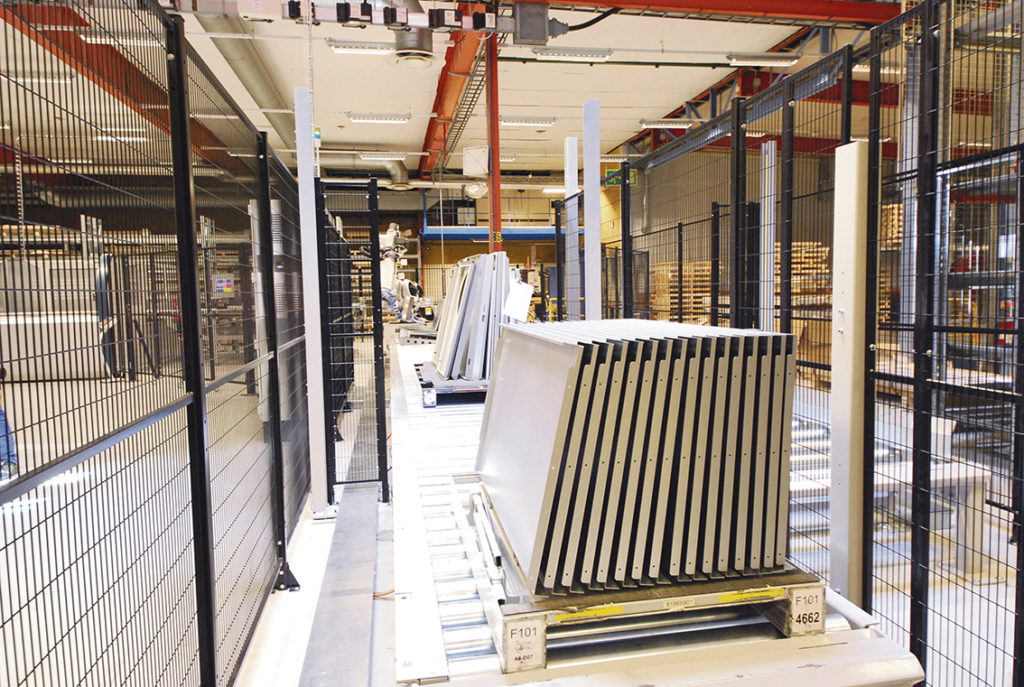
Robot hanterar paneler i slutet på den automatiserade produktionscellen. Man kallar det för linjärstapling på Swegon och det handlar om att få plats med fler paneler på pallen.