Det händer spännande saker på Höganäs som med sin teknik för Additiv tillverkning Digital Metal®, licensierat sin första maskin till en icke namngiven global kund.
– Det är en verksamhet inom Höganäs som gör allt själv och de har redan en rad processer för metallformning i huset och med vår teknik kan de göra helt nya saker. Det är också ett företag som uppskattar kombinationen av detaljrikedom, fina ytor och snäva toleranser. Komponenterna är både komplexa och kundanpassade, säger Ralf Carlström, chef för området Digital Metal®.

Man har även utökat kapaciteten inom Digital Metal®. Det senaste tillskottet är en toppmodern sintringsugn med varierbar atmosfär och temperaturcykel. Volymen är något större än den tidigare ugnen och man räknar med att kunna ha fyra skrivare som matar en ugn.
– I dagsläget har vi fem maskiner som står och kör och vi har precis bestämt oss för att bygga en sjätte. Det är något vi gör i huset och tar fyra-fem månader. Under hösten har vi även gått över till tvåskift för att öka vår produktionskapacitet. Vi ser en kraftig orderingång och åtgärderna är ett direkt svar på detta.
Ett viktigt område inom Digital Metal® är prototyptillverkning. Ofta kräver detta flera iterationer. Det är stor bredd i de prototyper som produceras, i många fall med tuffa krav på ytfinhet och annan efterbehandling, i andra fall enklare prototyper utan krav på efterbehandling.
– Just efterbehandling är något vi kommer att satsa mer på framöver. Det finns en rad tekniker och metoder för detta, vi har ett antal att arbeta med i huset idag och vi har även möjlighet att lägga ut på externa leverantörer. Vi vill utöka vår service till kunderna och bredda vårt erbjudande.
Höganäs är aktivt ute på mässor världen över för att visa upp sin teknik och de möjligheter som tekniken ger som undertecknad reporter kan konfirmera. Det är ett led i säljstrategin. I år har man även tagit mer hjälp av Höganäs ordinarie säljorganisation och anställt Alexander Sakratidis som säljansvarig. Vi skall få några ord med senare i artikeln. Det innebär att man når ut bredare genom ett stort kontaktnät och det har resulterat i flera nya kunder, menar Ralf Carlström.
Som om inte ovanstående satsningar vore nog har man också börjat erbjuda metallpulver specifikt för 3D-skrivarteknik, då inte endast till Höganäs egen utrustning utan även till konkurrenter och externa kunder.
– Det är för olika typer av Additiv utrustning, säger Ralf Carlström, laser, EBM och Direct Energy Deposition, DED. Det handlar framförallt om kundanpassade nickel-, kobolt- och järnbaserade material, som rostfritt stål och verktygsstål i olika varianter.
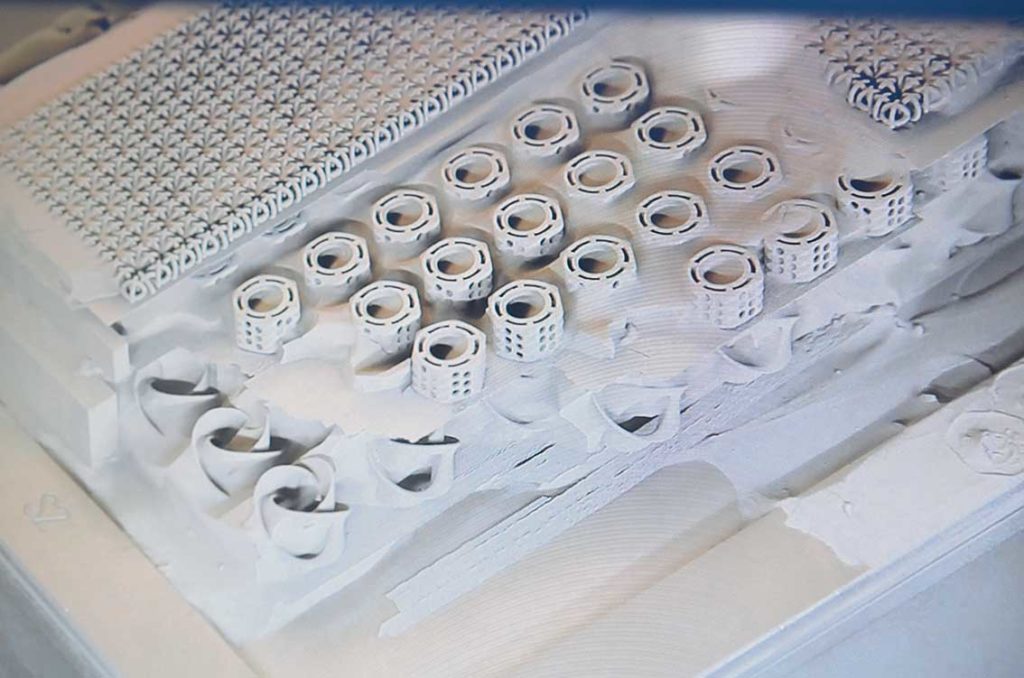
Tidningen Maskinoperatören åker de 12 milen till Höganäs och hälsar på.
– Från början var detta ett bolag i Göteborg, Fcubic som i samarbete med IVF som idag heter Swerea arbetade med tekniken additiv tillverkning och tog fram en maskin 2006. Vi på Höganäs började arbeta med dem 2010. Sedan slutet av 2012 ägs bolaget av Höganäs AB och verksamheten drivs numera på plats här i Höganäs och här har vårt fokus varit att utveckla nästa generation 3D–skrivare, berättar Ralf Carlström.
Höganäs metod som kallas Digital Metal® är att komponenterna limmas istället för att smältas ihop vilket ger god upplösning, bättre detaljrikedom och förhållandevis hög produktionshastighet i jämförelse med många andra tekniker. Skrivaren eller bygglådan som man kallar den skriver ut på metallpulverbädd med bläckstråleteknik. Tunna lager läggs på varandra och sedan limmas metallpulvret och på så sätt byggs små komponenter.
– Vi växer och idag är vi ett tjugotal medarbetare som jobbar med allt från ta emot kundbeställningar till att printa, sintra och efterbehandla produkter som tillverkas. Vi är en totalleverantör inom Additiv tillverkning vilket betyder att vi säljer vår maskinteknik och även pulver till marknaderna runt om
i världen, säger Ralf Carlström.
– Det är roligt och spännande att man kan tillverka olika komponenter med den här tekniken. Jobbet är mycket varierande och vi får vara med och påverka arbetssättet och delta i hela processen, säger tekniker Jelica Pomorisac.
– Vår nisch är att ta fram främst små komponenter., ofta mindre än 50 mm. Vi arbetar med fler olika branscher och då handlar det om en mängd lika prototyper. När det gäller industriella komponenter ser vi nu inte bara beställningar av prototyper utan även mindre serier. Alt vi behöver från kunden är en 3D CAD-fil så är vi igång, förklarar Ralf Carlström.
Bland de utmaningar som finns är bl.a att när man sintrar komponenterna så krymper de 20 % vilket gör att man printar dem 20 % större än det begärda formatet. Andra utmaningar som man nu arbetar med är att ta fram produkter i material som koppar, silver och titan.
– Vi lever nu i en spännande värld där det händer mycket inom Additiv tillverkning och som sagt vi har hela kedjan komplett från maskin, olika pulver till egen teknikutveckling ”in-house”, och vi lär oss mycket av att producera själva, avslutar Ralf Carlström.
Vi vill veta mer och Ralf och Alexander ger oss mer input.
– Jag är utbildad bergsingenjör från början och har innan jag började arbeta med additiv tillverkning sålt pulver för Höganäs i alla år. Vi är stora på världsmarknaden och jag kan nästan garantera att det i varje fordon i världen sitter en eller flera komponenter tillverkat av pulver från Höganäs, säger Ralf och Alexander berättar att han började arbeta som säljansvarig på det nu expanderande området inom Höganäs 2015.
– Jag är kontaktpersonen och arbetar med utåtriktad försäljning och information till kunder som är och kan vara på väg in i 3D print världen. Just nu är vi aktiva på mässor runt om i världen och här arbetar jag aktivt med att följa upp de kontakter som vi skapar. Jag vill betona att vi säljer både maskiner och legouppdrag, säger Alexander och fortsätter;
– Fördelarna med tekniken är att man kan tillverka prototyper väldigt kostnadseffektiv jämfört med traditionell tillverkning som formsprutning och fräsning som kräver ett verktyg. Kunden kan även snabbt och utan kostnader ändra komponentens utseende och design utan merkostnad. Industrin får nu också mer och mer upp ögonen för tillverkning av små serier då processen nu utvecklats så att den lämpar sig för serieproduktion. Och då passar tekniken som hand i handsken om vi pratar avancerade geometrier och former.
– Vi har utvecklat vår process så att vi får en allt mer högre produktivitet då vår bläckstråleskrivare är snabb och det är anser vi nyckeln för framtiden om vi skall utvecklas som maskintillverkare och kontraktstillverkare. Och vårt sätt att tänka och utveckla vår maskinteknik är inte så lätt att kopiera för vem som helst utan ger oss ett försprång på marknaden, säger Ralf och fortsätter beskriva tekniken;
– Vi utvecklar och förfinar vår teknik vilket ger en minskad standardavvikelse i våra automatiserade processer och att vi ser antalet kassationer minska. Idag ligger vi på 0.2 % felavvikelser vilket är riktigt bra, mycket bättre än vad många tror och avslutar med att konstatera att industrin idag vet väldigt lite om tekniken, man har hört talats om additiv tillverkning men vi är i början på en lång resa in i framtiden, det är ett ständigt missionerande men vi tar gärna den fajten.