Därför är det knappast överraskande att WFL också utvecklat additiv tillverkning. ”Med våra maskiner, klarar vi avancerade applikationer och de flesta av våra kunder vill kunna klara komplexa bearbetningar som kräver högsta precision, repeternoggrannhet och processtabilitet. Detta kräver innovativt och ibland även revolutionerande tänkande ”, förklarade Reinhard Koll, Applikationsteknisk chef på WFL.
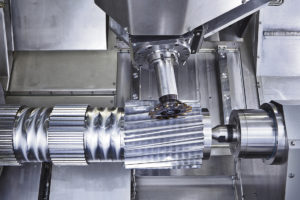
Ytterligare bearbetningssteg utan fler uppspänningar
”Trots det enorma utbudet av processer i millturnmaskiner var det förr nödvändigt att lossa arbetsstycket för att utföra ytterligare en bearbetning och, vid behov, därefter återgå till millturnmaskinen för ytterligare efterbearbetning. Detta är fortfarande oftast nödvändigt under bearbetningar som kräver härdning, något som skall svetsas eller kräver beläggning”, fortsätter Koll. Som exempel, hänvisar han till tillverkning av arbetsstycken som kräver applicering av slitstarka beläggningar eller kuggar, som tillverkas med hjälp av millturn och som sedan kräver efterföljande härdning. Målet har länge varit att göra det möjligt att dessa typer av arbetsmoment ska kunna göras direkt i en millturnmaskin.
För några år sedan hade frågan om additiv tillverkning ännu inte diskuterats. Denna speciella tillverkningsprocess utvärderades under en intern workshop för ca två år sedan. Syftet var att ta reda på om det skulle vara av betydelse för företaget och om det med framgång skulle kunna inkluderas i millturnkonceptet. Resultatet visade att kombinationen av fleroperationsmaskin och laserteknik skulle vara ett givande drag.
”Det viktigaste är alltid genomförandet. Först och främst måste vi skapa mervärde för våra kunder”, förklarar Dieter Schatzl, marknadschef på WFL. ”Kundens arbete måste göras enklare och mer kostnadseffektivt. Helst vill vi att de ska kunna utföra alla sina bearbetningsprocesser i vår maskin”, tillade Schatzl.
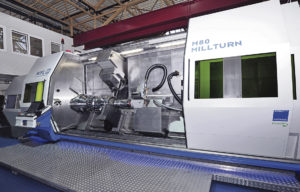
Den rätta processen
Det bästa sättet att möjliggöra svetsning, härdning och materialbeläggning är en applikation via laser och användning av metallpulver. Denna teknik omfattar alla nödvändiga element. En kombination av möjligheter att bearbeta ett stort antal detaljer i många olika material och i stora volymer ger optimala förutsättningar för ett brett användningsområde. Men det finns fortfarande några grundläggande frågor som måste besvaras: Hur skulle metallpulvret bete sig i maskinen? Vilken maskintyp kan utrustas med denna teknik? När kan företaget lansera detta på marknaden? Vilka partners kan företaget jobba med i detta projekt?
Applikatorhuvudet utvecklat av Dresden-baserade ”Fraunhofer-institutet for Material and Beam Technology IWS” erbjöd den bästa lösningen. Det uppfyllde WFL´s krav exakt. Applikatorhuvudet matas av en Laserline diod-laser, och har en märkeffekt på 10 kW. En laser med en effekt upp till 40 kW kan installeras som alternativ.
Processen i detalj
Tack vare en kombination av olika tekniker, kan laserbeläggning och laserhärdning utföras med samma huvud, eftersom båda applikationerna kräver en något större brännpunkt. Under beläggningen, används en inert gas för att fokusera metallpulvret på en träffpunkt via ett ringmunstycke. Laserstrålen är också fokuserad på detta område, detta resulterar i en smältpool. Det smälta metallpulvret sätter sig i poolen och stelnar därefter. Bredden och höjden av materialbeläggningen som ska appliceras bestäms genom att exakt balansera den energi som tillförs och passagehastigheten av laserstrålen med den mängd pulver som matas genom maskinen. Som med traditionell inert gassvetsning förhindrar inert gas oxidationsprocesser samtidigt som det fungerar som en bärare och transport av gas för pulverpartiklarna. Pulverpartiklarna är mellan 100 och 150 µm i storlek, så de är tillräckligt stora för att filtreras bort av 40 µm filter. Detta säkerställer att överskottspulvret i längden inte påverkar maskinen. Beroende på processparametrarna, applikationshastigheter produceras beläggningar från 1,0 mm och uppåt.
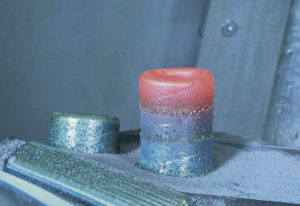
Fördelarna med att integrera additiv tillverkning i en fleroperationsmaskin är uppenbara. Möjligheten att tillverka komplexa detaljer som inte kan tas fram med hjälp av konventionella tillverkningsprocesser, eller som bara kan tillverkas med stor svårighet, är nu inom räckhåll tack vare denna teknik. I fall med stora detaljer som skjuter ut från arbetsstycket, är överdimensionerade råämnen inte längre nödvändiga, vilket minskar bearbetningstiden. Detta sparar tid, sänker kostnaden för verktyg och ger möjlighet att fortsätta bearbetningen utan att behöva spänna fast arbetsstycket. Detta är en viktig faktor, särskilt när materialen som används som är dyra eller svåra att spänna fast. ”Beläggningslaserhuvudet kan även användas för laserhärdning, och en valfri lins, som har optimerats för härdningsprocessen, kan installeras. Som exempel kan kuggflanker härdas direkt efter fräsning vid tillverkning av kugghjul”, förklarade Koll.
För lasersvetsning krävs ett huvud med en annan lins. För djupsvetsning krävs en mycket smalare brännpunkt för att laserstrålen ska nå svetsdjupet på ena sidan och för att hålla den värmepåverkade zonen så liten som möjligt på den andra. Målet är att utveckla ett alternativ för att smala, djupa borrhål. På detta sätt kan en kylkanal först fräsas in i den yttre konturen av en detalj och en beläggning kan därefter lasersvetsas över detaljen. Detta gör inte bara bearbetningen lättare, det ger också helt nya möjligheter när det gäller formen. Det kommer även att vara möjligt att svetsa roterande delar koncentriskt. Dessa skulle tidigare har tillverkats parallellt av huvud- och motspindeln av maskinen.
Laserhuvudet i verktygshållaren
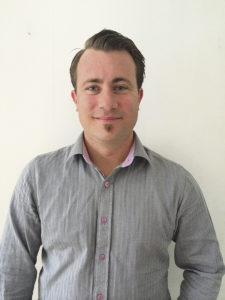
Båda laserhuvuden matas av samma diodlaser och kan lätt ändras. Det aktuella laserhuvudet placeras på en särskild konsoll inuti maskinen och är ansluten till den externa laserförsörjningen via mediakabeln. Lasern monteras med hjälp av WFL prismatiska verktygsinterface. Tack vare de fem interpolerande axlarna på WFL´s millturnmaskiner kan lasern svängas över ett stort område och kan även användas för att bearbeta fritt formulerade ytor. Beroende på vilket munstycke som används, kan materialetbeläggning även utföras på horisontella ytor. Dessutom är det möjligt att uppnå en rad effekter under materialbeläggningen genom att använda olika former av munstycken och olika pulverkombinationer.
”Som en grundläggande princip, när nya möjligheter uppstår, står WFL fast vid sin strategi om att arbeta tillsammans med sina kunder för att bestämma processparametrar med hjälp av konkreta projekt och då skräddarsy bearbetningsprocessen efter applikationsbehov. Det är det enda sättet vi kan jobba på för att uppnå den optimala nivå på kvalitet och effektivitet som våra kunder förväntar sig av oss ”, avslutade Koll.
Mer information: tl-maskinpartner.com