Designade för tillverkningsbarhet
”Det finns inget effektivt med innovation”, sa den brittisk-amerikanske författaren och föreläsaren Simon Sinek en gång. Men har han rätt? Det åligger tillverkare att vara innovativa och hålla jämna steg med alla förändringar, särskilt de som drivs av e-mobilitet. Här förklarar Robert Smith, Offer Manager för håltillverkning och kompositmaterial vid verksamhetsgrenen solida hårdmetallverktyg (SRT) hos specialisten på skärverktyg, Sandvik Coromant, hur tillverkare kan – och måste – vara effektiva i sitt innovationsarbete med avancerade borr av solid hårdmetall.
Design för tillverkningsbarhet (DFM) har blivit allt viktigare för tillverkare i en mängd olika branscher – inklusive fordonsindustrin, flygindustrin och den allmänna verkstadsindustrin. DFM innebär att man utformar produkter som kan tillverkas enklare, effektivare och mer kostnadseffektivt. För Sandvik Coromants kunder innebär detta vanligtvis att man uppnår en fördelaktig kostnad per detalj vid bearbetning av komponenter; eller kostnad per hål i borrnings- och gängningsapplikationer. Vart och ett av dessa mål kräver skärverktyg som är mycket tillförlitliga och stöder hög produktivitet.
Dessutom fortsätter konceptet DFM att utvecklas i takt med en alltmer globaliserad försörjningskedja och en ökad efterfrågan på anpassade produkter. E-mobiliteten kommer också att ha en inverkan på DFM. Detaljer till el- och hybridfordon har större variation mellan tillverkare jämfört med deras motsvarigheter i en förbränningsmotor (ICE), och de tillverkas i större utsträckning av sega material som låglegerat stål, inconel och aluminium. En eltrend inom flygindustrin må fortfarande ligga några år bort, men samma trend inom fordonsindustrin är aktuell här och nu. Det innebär att tillverkare måste hålla jämna steg med förändringarna, annars riskerar de att hamna på efterkälken.
Men hur kan avancerade verktygslösningar göra skillnad för DFM? Svaret finner man i faserna från CAD till komponent inom tillverkningsindustrin. CAD till komponent hänvisar till tre steg i tillverkningen. Först har vi fasen CAD till spindel, där CAD och modeller från datorstödd tillverkning (CAM), inklusive digitala tvillingsimuleringar används för att förbereda en bearbetning och säkerställa att verktygsuppsättningen, arbetsstycket och bearbetningsparametrarna har optimerats.
Därefter kommer spindelfasen, eller den faktiska bearbetningen. Här kan vi utvärdera verktygets bearbetningsprestanda mot arbetsstycket, och dess effekt på kostnaden per detalj, kostnaden per hål, och – slutligen – våra kunders omsättning. Den sista fasen är komponentfasen där komponentens kvalitet och ytjämnhet utvärderas. Ytjämnhet och detaljer som hålens ytintegritet har mycket stor betydelse, oavsett om man är verksam i fordonsindustrin, flygindustrin eller den allmänna verkstadsindustrin. Bättre hålkvalitet förhindrar att komponenten går sönder– och beror till stor del på tillverkningsprocesserna som används vid bearbetning och finbearbetning av hålen.
I synnerhet är ett borrs utformning avgörande för att kunna producera bättre hål. Det är därför som skäreggsgeometrier i borr ständigt utvecklas, eftersom det är viktigt att uppfylla de högsta standarderna för tillverkning och detaljkvalitet. Det är också viktigt att använda skärvätska för att minska värmeuppbyggnaden i verktyget. Det är här som Sandvik Coromants specialister kan spela en viktig roll och hjälpa kunderna.
Enkel tillverkningarvning
Sandvik Coromant arbetar nära sina kunder för att inhämta relevant information om deras bearbetningsprojekt, så att de vet vad som krävs. Låt oss säga att kunden behöver utföra en kontinuerlig borroperation i ett arbetsstycke av 316L rostfritt stål – ett material som, enligt en studie publicerad i Journal of Engineering and Applied Sciences som ges ut av Asian Research Publishing Network (ARPN), har visat sig orsaka ”snabb och förödande förslitning” som påverkar livslängden hos skärverktyg betydligt.
I denna fas av kundens bearbetningsprocess, den tidigare nämnda CAD-till-spindelfasen, kan våra specialister undersöka och bakåtkompilera kundens processer, inklusive användandet av CAD och CAM-modeller. Genom att göra detta kan Sandvik Coromant ta fram en verktygsprototyp på morgonen, och ha den redo för testning vid FoU-avdelningen på eftermiddagen. Innan digitaliseringens dagar skulle den här processen har krävt att man skickade ritningar fram och tillbaka, och arbetet hade tagit upp till sex veckor. Idag har möjligheten att leverera verktygsprototyper redan samma dag varit helt revolutionerande för Sandvik Coromant.
Ökad skärlivslängd ång
Sandvik Coromant erbjuder en mängd produkter som stöder kunderna vid tillverkning av komponenter, även till elfordon. Bland dessa återfinns CoroDrill® 860, ett borr i solid hårdmetall som har tagits fram för snabb och problemfri borrning samt maximal produktivitet tack vare hög effektivitet under skärande bearbetning. Verktyget finns i en mängd olika geometrier, inklusive 860-MM för rostfria stålmaterial som ger långa spånor, så som austenitiskt, superaustenitiskt, ferritiskt och rostfritt duplexstål.
Sen har vi CoroDrill® 860-GM som har visat sig användbart för tillverkare inom fordonsindustrin vid borrning av motorblock, höljen, flänsar och grenrör. Borret lämpar sig också väl för alla applikationer utanför fordonsindustrin och den allmänna verkstadsindustrin där hålkvaliteten är avgörande – till exempel inom flygindustrin, olje- och gasindustrin, kärnkraftsindustrin och för producenter av förnybar el.
860-GM har uppnått imponerande resultat, även hos en fordonstillverkare i Korea. Sandvik Coromants kundprojekt var att borra genomgående hål i en batch med kontakter till växellådor. Målet var att borra åtta genomgående hål med en diameter på 8,2 mm (0,32″) i respektive komponent, med ett djup på 10 mm (0,39″). Den befintliga lösningen producerade 200 komponenter, totalt 1 600, med en skärhastighet (Vc) på 80 m/min (3 102 varv/min) och en skärmatning (Vf) på 381 mm/min. I jämförelse producerade CoroDrill® 860-GM 2 300 komponenter (18 400 hål) med en Vc på 100 m/min (3 878 varv/min) och en Vf på 814 mm/min.
Över lag gav CoroDrill® 860-GM en betydligt -längre verktygslivslängd med 1 150 %. Detta följdes av en produktivitetsökning som hjälpte till att sänka kostnaden per detalj avsevärt för kunden. Liknande imponerande resultat har rapporterats från andra Sandvik Coromant-kunder i fordonsindustrin världen över.
Något som är minst lika viktigt som att borra släta hål är gängningen, den åtgärd som skapar en gänga inuti hålet. För detta erbjuder Sandvik Coromant CoroTap® 100, 200, 300 och 400, vilka allihop har optimerats för olika applikationer. För att bara nämna några exempel så är CoroTap® 100 en serie raka gängtappar som har optimerats för kortspånande ISO K-, ISO N- och ISO H-material. CoroTap® 400 å andra sidan, är en spånfri pressgängtapp för höga hastigheter, för både genomgående hål och blindhål i stål, rostfritt stål och aluminium. Kundens val beror på vad som passar deras applikation bäst.
Framöver kommer Sandvik Coromant att kunna erbjuda CoroTap® 100-N och CoroTap® 400-N. Dessa två har tagits fram för att stöda kunder med gängningsapplikationer i aluminium, vilket blir allt vanligare i tillverkningsprocesser.
Än så länge visar Sandvik Coromants välpresterande skärverktyg hur verktyg som har tagits fram för att stöda borrning och gängning i flera olika material kommer att spela en avgörande roll när det gäller att hjälpa tillverkare producera lättare, mindre och mer varierande komponenter. Inte nog med att maskinverkstäder kan utforma och utveckla dessa detaljer mycket lättare och mer kostnadseffektivt, de kan även se till att DFM förblir en prioritet i hela tillverkningen – och sköta innovationsarbetet effektivt.
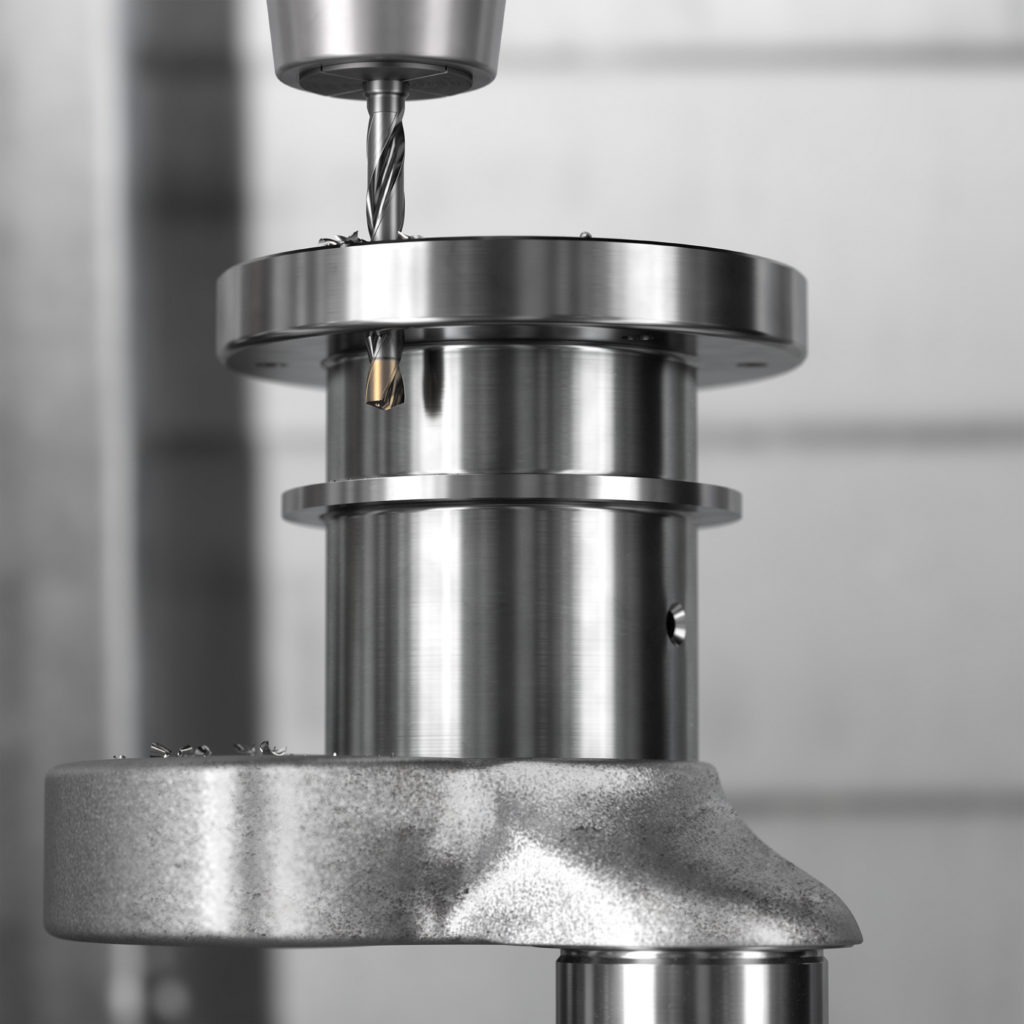
Sandvik Coromant
Som en del av den globala Sandvik-koncernen är Sandvik Coromant ledande när det gäller verktyg för skärande bearbetning, bearbetningslösningar och kompetens som höjer standarden inom industrin, samt innovationer som efterfrågas inom skärande bearbetning idag och i framtiden. Utbildningar, stora investeringar i forskning och utveckling, samt starka partnerskap med kunder säkerställer utvecklingen av bearbetningstekniker som förändrar, leder och driver framtiden för tillverkning. Sandvik Coromant äger över 1 700 patent globalt, har över 7 700 anställda och är representerade i 150 länder.
För mer information gå in på www.sandvik.coromant.com eller följ diskussionerna på sociala medier.
Kontaktuppgifter för redaktionella frågor
Kontakt: Anna Lind – PR – Sandvik Coromant
Mejl: anna.w.lind @sandvik.com
PR agency
Kontakt: Laura England eller Courtney Cowperthwaite – Stone Junction
Mejl: laura@stonejunction.co.uk eller courtney@stonejunction.co.uk
Tel: +44 (0)1785 225416