Östlings Verktygs AB bildades 1959 och har sedan dess arbetat med konstruktion och tillverkning av formverktyg för termoplast. Företagets VD och numera ensamägare Sven Sköld tog över företaget efter Bernt Östling 2011, säger att företaget i och med flytten för 5 år sedan, mer än fördubblat sin verkstadsyta från tidigare 600 kvm till 1 400 kvm.
– Det är klart att det är ett lyft på flera olika plan, när vi kan investera och expandera vår verksamhet utan att i första hand behöva tänka på platsbrist för framtiden.
Sven Sköld anställdes av Bernt Östling 1995 och arbetade först som konstruktör för att sedan bli produktionsansvarig.
– Bernt var min mentor och en fantastisk människa, någon som jag verkligen ser upp till på många sätt än idag.
Allt har en historia och vi får gå tillbaka till början på 1900-talet då lokalerna vid järnvägsstationen inrymde det första industrihotellet kan man kalla det och här började man förbereda för att tillverka taggtråd för 1:a världskriget.
– Man har berättat för mig att planerna var långt komna med stickspår in till fabriken och man höll på med att utveckla en storskalig industri men så slutade 1: a världskriget och allt lades ner. Efter det har det varit många olika näringsidkare och kommer vi fram till början på 1950-talet, så startade Bernt Östlings far industriverksamhet där man tillverkade allt möjligt som exempelvis olika belysningsarmaturer och presentartiklar, ja det mesta faktiskt, berättar Sven Sköld,och vi återvänder till dagens ämne som handlar om ny teknik, precision och produktivitet, något som inte var nödvändigt förr i tiden, skrivet med all respekt.
2019 och storinvesteringen är på plats
Sköld tycker att konjunkturläget känns bra och framtiden ser ljus ut. Han säger också att han under åtta år aldrig har behövt be någon av sina anställda att ”torka av en maskin eller sopa golvet” utan det har funnits något att göra hela tiden om ni förstår vad Sven menar.
– Vi tillverkar verktyg, prototyper och förserier för Medical, förpackningsindustrin, vi har en del kontakter med fordons- och elektronikindustri, styrkan är allsidigheten.
– Våra kunder är lokala här i Gnosjö och Anderstorp men vi har även uppdragsgivare runt om i Sverige. Fler branscher ger fler ben att stå på och det är något man medvetet har jobbat på, med en ökande omsättning och lönsamhet som resultat, vilket han är mer än nöjd med.
– Vi producerar samtliga verktyg här på fabriken och blandar inte in importerade komponenter. Allt är “Made in Gnosjö”, säger Sven Sköld stolt.
Och här kommer vi in på en het potatis då branschen genomgått fler stålbad genom åren där många jobb gick på export till låglöneländer som till exempel Portugal, östra Europa och Kina.
– Det är klart att man får lite puls när man tänker på hur det var men vi har inte gått ”tomma” här något år men det är klart att lönsamheten blivit drabbad. Idag har det vänt och vi får många order som tidigare tillverkats i andra länder av våra kunder, säger Sven Sköld.
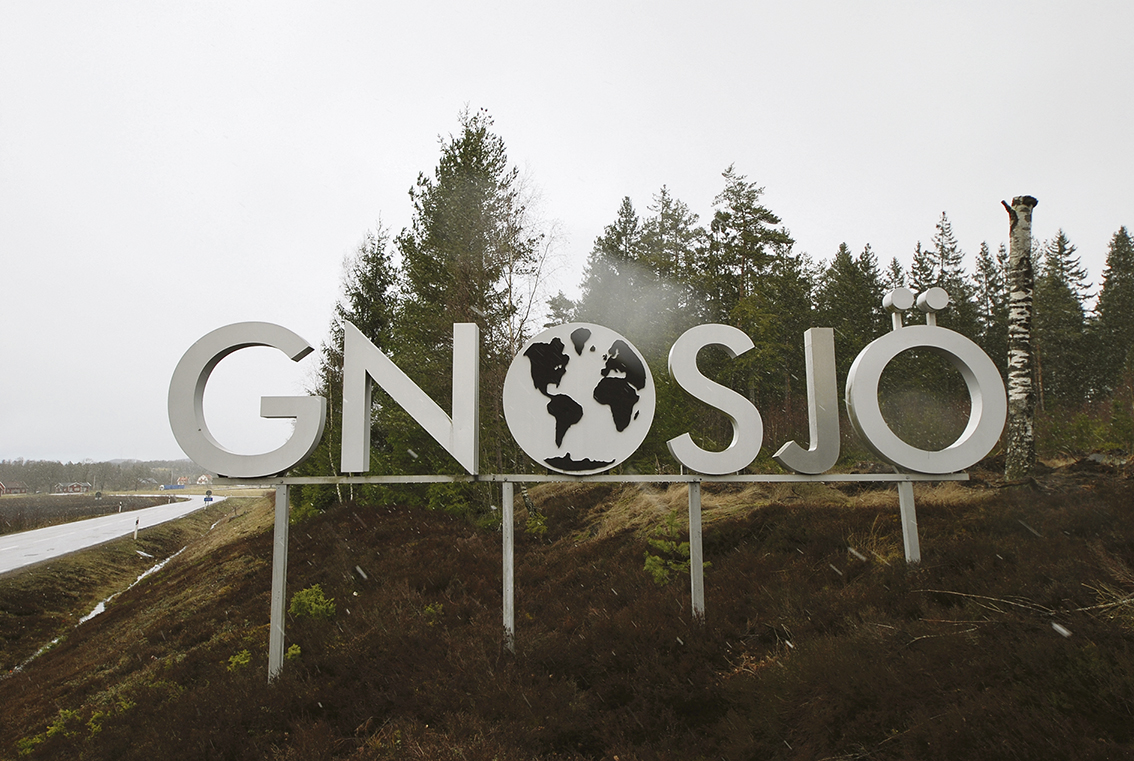
Man har skrivit spaltmeter om verktygstillverkningen som nästan försvann från Sverige på 80- och 90-talet men nu finns det fakta på att det inte lönade sig för svenska företag att på sikt lägga tillverkningen i andra länder, för att sedan transportera verktygen tillbaka till sina fabriker i Sverige. Som sagt långa transportertider, försenade leveranstider, sämre kvalitet och dolda kostnader som man inte räknat med blev resultaten för många företag.
Och det här med outsourcing har vi också skrivit flera artiklar om där flera företagsledare sett den som ett rent flockbeteende och dåliga affärer.
Från Långgatan till Marieströmsvägen
Företagets expansion kom när man flyttade från Långgatan till Marieströmsvägen och då anställde man flera personer och en sänkgnist från OPS Ingersoll kom på plats i de nya lokalerna hos Östlings. För överst på önskelistan stod en sänkgnist följt av en ny fräsmaskin. Men investeringen kom att se annorlunda ut än vad som vad meningen från början.
– Allt började egentligen när ”Börje 100-del” slutade och blev pensionär för 4 år sedan. Han var en ”trollkarl” hos Östlings och hade arbetat här som verktygsmakare i 50 år, berättar Sven och förtydligar;
– Han var den som såg till att det alltid blev perfekta resultat
i vår produktion och när han mycket väl förtjänt gick hem till pensionärslivet så blev det annorlunda i verkstaden, helt klart och jag förstod att vi behövde tänka till och tänka om. Den äldre generationen av verktygsmakeri och professionellt hantverk behövde vi delvis ersätta och komplettera med datorstyrd produktion.
Hösten 2018 installerades en ny fräsmaskin, en robot för palletter och elektroder och en mätmaskin. Detta integrerades helt med den sänkgnist som stod på plats sedan två år tillbaka. Östlings Verktyg har nu investerat i en helautomatisk fräs- och gnistcell och tar ett rejält kliv framåt både i precision, kapacitet och effektivitet.
– Jag tänker att vi kommer att kunna öka produktiviteten och maskinutnyttjandet i verkstaden med 20 – 30 procent inom ett till två års sikt, tack vare den här investeringen, plus att vi får färre flaskhalsar i produktionen och minimerar fel beroende på den mänskliga faktorn, säger Sven Sköld.
– Den nya investeringen är ett sätt att möta konkurrens och ökad efterfrågan på formverktyg. Det här möjliggör också obemannad körning dygnet runt.
Det handlar alltså om en helautomatisk fräs- och gnistcell från OPS Ingersoll bestående av en sänkgnist, en 5-axlig höghastighetsfräsmaskin samt en robot med magasin för Erowapalletter och elektrodhållare som hanteras av båda maskinerna. Systemet integreras dessutom med en CMM mätmaskin från Mitutoyo som används i förriggningen och ser till att varje palett synkas med rätt program utifrån exakta koordinater. Operatören behöver inte längre mata in manuella data och slipper hålla reda på yta och position.
– Och eftersom mätmaskinen ger rätt positioneringar på tusendelen och fräsmaskinen och sänkgnisten kommunicerar med varandra så tar det oss ett steg längre i jakten på precision, säger Sven Sköld.
Ökad precision och fler maskintimmar när nu formkurvan pekar uppåt för Östlings Verktyg
– Det här ger oss en ökad nivå av precision vilket är huvudsyftet. Vi eliminerar den mänskliga faktorn. Vi kan också öka nyttjandegraden i maskinen och använda dygnets alla timmar för att möta konkurrensen eftersom operatörerna kan rigga medan maskinerna går. Och när operatören går hem så fortsätter cellen producera bitar, förklarar Sven.
Vi ber Sven utveckla hur han tänker ur det produktionstekniska perspektivet.
Investeringen i en automationscell som producerar verktygsdelar med total kontroll på toleranser är samtidigt ett sätt att möta den allt mer påtagliga verktygsmakarbristen i landet.
– Pensionsavgångar har gjort att de som brynte och kände och fick bitarna att lira ihop med varandra inte längre är kvar (Börje 100-del). Nu möter vi bristen på manuellt skickliga bänkarbetare med teknikutveckling. Dessutom innebär investeringen en möjlighet att ta expressjobb i form av ”snabba verktyg”, provverktyg, som kan vara redo för provkörning inom ett dygn i vår plastspruta, säger Sven.
– Det är dags för tekniklyft inom industrin och vi går gärna
i frontlinjen i ämnet maskinkommunikation. Som verktygsmakare har man en naturlig öppenhet för ny teknik. Om man bara ser sig om och öppnar ögonen så ser man hur det ”kokar av möjligheter”, säger Sven och fortsätter;
– Att vi nu har investerat i ett helautomatiskt Mould- Center från OPS Ingersoll som första företag i Sverige är resultatet av att vi ser otroliga utvecklingsmöjligheter om man hittar vägar och nycklar att sammanföra teknikutvecklingen på olika områden och hitta länkarna mellan fräs, gnist, automation och mätning.
– Mer lättanvända applikationer och användarvänliga lösningar finns på marknaden. Vi pratar mjukvara och digitaliseringen som nu ger industrin möjligheter att ta stora steg in i datakommunikation. Med CAD och CAM, smart integrerade i varandra kan man idag genom några få klick på datorn i styrningen få en färdig bearbetningsfil som själv hämtar och korrigerar nödvändiga data för en näst intill felfri tillverkningsprocess och slipper därmed den mänskliga faktorn där emellan. Operatörens uppgifter blir mer att planera, övervaka och kontrollera komplexa processer och där är människan helt överlägsen, säger Sven Sköld.
– Med den helautomatiska robotcellen kan vi nu på ett mycket bättre sätt jämna ut toppar och dalar, komprimera beläggningsgraden och få ett jämnare flöde, vilket var en av de viktigaste anledningarna till vår investering Just nu upplever vi ett stabilt läge. Visst lever vi med korta leveranstider och en kort framförhållning när det gäller orderstocken, men vi är snabba på att komma igång med nya projekt och det gör oss oerhört flexibla, säger Sven.
– Bland annat inom prototypframtagning och lågserier. Vi kör steget efter SLA-prototyper, något vi kallar för ”snabba verktyg”. Meningen är att vi skall kunna hjälpa kunden när det är bråttom och nu har vi kapacitet för det scenariot. Det handlar om prototyper och små serier i formriktiga verktyg, en produkt som är gjord enligt serieproduktionsliknande förhållanden.
– Och här har vi märkt att det finns en stor efterfrågan. Det här är en gren som har växt hos oss, säger Sven.
– Vi är ett verktygsmakeri, vi är bra på att gnista och fräsa, då är det tydligt att vi behöver bra maskiner och i vår senaste maskininvestering har vi hittat en helhetslösning från en leverantör, efter att ha funderat länge. Det är en storinvestering men ”allt lirar ihop” på ett mycket bra sätt och vi är supernöjda. Datastyrd tillverkning kopplat till Industri 4.0, det gillar vi, säger Sven Sköld.

Maskinleverantören

Maskintillverkaren OPS Ingersolls svenska representant Lennart Rönn på Victoolia menar att Östlings investering är mycket intressant eftersom det är det första kompletta Mould-Centret i Sverige som man installerat. Det här är intressant och vi skall titta lite närmare på maskinerna och tekniken som styr.
Victoolia AB startades av Lennart Rönn 1991. Företagets huvudsakliga fokus är leverantör av tråd- och sänk-gnistmaskiner samt 3- och 5-axliga höghastighetsmaskiner och fräsverktyg från japanska UNION TOOL.
– Vi representerar Mitsubishi Electric och OPS-Ingersoll. Förutom försäljning av maskiner, tillhandahåller vi service, reservdelar och förbrukningsmaterial. Båda våra leverantörer har stor erfarenhet av automatiseringslösningar. Vi är baserade i Täby utanför Stockholm men har hela landet som arbetsområde, säger Lennart Rönn.
Vi ber Lennart Rönn om lite tekniska fakta runt maskinerna som han levererat och installerat.
Gemensamt för OPS Ingersolls HSM och sänkgnistmaskiner är att de är portalbyggda (Gantry). Denna konstruktion gör att de håller en mycket hög precision och klarar temperaturvariationer på ett bättre sätt än exempelvis så kallade C-byggda maskiner.

– OPS-INGERSOLL erbjuder en komplett arbetsflödeslösning för press och formtillverkare. Toppmodern 5-axlig fräsning som samtidigt kombinerar både prestanda och hög precision.
– Maskinen kan bearbeta hårda material men även grafit vilket gör den väldigt mångsidig. Det är fortfarande enkelt att automatisera tack vare åtkomlighet från båda sidor.
– Det nya Heidenhain styrsystemet TNC 640 möjliggör både hög precision och snabb bearbetning och har medfört en annan marknadsfördel tack vare att många maskinoperatörer redan har erfarenhet av Heidenhain.
– Gantry Eagle sänkgnistmaskiner är alla tillverkade i portalutförande vilket ger bästa möjliga precision och prestanda. Generatorn är utvecklad för att vara både snabb och att medföra minimal förslitning av grafitelektroderna. OPS-INGERSOLL erbjuder en lösning från en källa, för alla verktygstillverkare. Hanteringssystemet MultiChange sammanbinder de båda teknikerna och ger möjlighet till mycket obemannad produktion med en kapacitet på upp till 154 elektroder och 8 stycken palletter med arbetsstycken. Allt på en mycket liten golvyta.
– I samband med OPS-INGERSOLL detalj-hanteringsprogramvara (OIPM) genererar det ett komplett arbetsflöde som kan integrera även andra (periferiska) enheter i processen. I detta fall en CMM (Mitutoyo mätmaskin). Dessutom används RFID chip-identifiering i processen som medför ett problemfritt arbetsflöde för operatören, informerar Lennart Rönn

OIPM-OPS-Ingersoll Part Managment
Vad är OIPM?
• OIPM hanterar detaljer (arbetsstycken och/eller elektroder och dess data)
• Arbetsstyckena är monterade på palletter och elektroderna på hållare
• Bestämning av offsetvärden med en CMM, sålunda minskning av ställtider
• Identifiering med chips som blivit monterade på palletter och elektrodhållare
• Bestämning av detalj till en pallett med hjälp av chip i OIPM
• Magasinet är utrustat med automatiskt chipläsarsystem
• Det medför att man kan placera palletter och elektrodhållare på valfri ledig plats
• Systemet identifierar och håller reda på possitionerna helt automatiskt
Vad är inte OIPM?
• OIPM är inte ett CAM-system
• Hantering av maskinbearbetningar är inte möjlig, följaktligen kan OIPM inte avgöra om en bearbetning är möjlig
• Operatören är ansvarig för i vilken ordning bearbetningar måste ske
Fördelar med OIPM
• Enkelt system för detaljhantering
• Minskning av ställtider (nya jobb kan förberedas under tiden maskinerna bearbetar)
• Hög tillförlitlighet
• Helt från en leverantör
• Kostnadseffektivt
• Möjlig att uppgradera till ett fullt utrustat ”job managment system”
Östlings höghastighetsfräsmaskin OPS-Ingersoll V9 är 5-axlig med Heidenhain styrsystem. 4/5-axeln är så pass kraftig att man kan bearbeta arbetsstycken på upp till 500 kg. En OPS-Ingersoll V9 går att beställa med tre olika spindelstorlekar nämligen HSK E40: 1 – 42.000 rpm. HSK E50: 1 – 36.000 rpm, HSK E63: 1 – 18.000 / 26.000 rpm. Eftersom Östlings väljer att bearbeta både stål och grafit valdes en HSK E50 och Fischer spindel med 36 000 rpm.



