Det var en gång i Hillerstorp
Hillerstorp ligger i Småland för den läsare som inte visste. Thule är ett svenskt företag som grundades 1942 av Erik Thulin som då tillverkade utrustning till fiskare. Men redan på 50-talet så började Thule att tillverka takräcken för bilar och detta är fortfarande troligen en av de produkter som de flesta förknippar Thule med idag.
I över 75 år har Thule skapat lösningar som underlättar livets äventyr. Man har fokuserat på att utveckla smarta, snygga produkter av hög kvalitet som är miljövettiga, säkra och enkla att använda. Företaget tillverkar idag också en rad andra produkter som alla har det gemensamt att de underlättar ett aktivt liv för sina användare. Produktportföljen innehåller bland annat takboxar, hållare för cykel-, vatten- och vintersporter, taktält för montering på bilen, men också produkter för den aktiva familjen så som barnvagnar, cykelvagnar och cykelbarnstolar. Thule är marknadsledare inom sina produkter för husbilar och husvagnar exempelvis markiser, cykelhållare och förtält för husbilar och husvagnar och företagets attraktiva vandringsryggsäckar, resväskor och kameraväskor växer i volym över hela världen.
Och vi kan rapportera att det går bra för företaget inte bara i Sverige utan globalt, mycket bra till och med. Och med ett ökande intresse för fritid och semester närmare hemmet så har försäljningen ökat ytterligare. 2021 omsatte Thule Group 11,4 miljarder kronor. Företagets produkter säljs i 140 länder.
Sammantaget innebär försäljningsökningarna att man behöver öka kapaciteten i sina fabriker världen över och i Hillerstorp expanderar man med både nya maskiner och utbyggnader i produktionsyta. I detta lilla reportage skall vi titta in på pressavdelningen och även verktygsavdelningen för att se vilka investeringar som görs i detta nu.
Nyckeln till plåtens formbarhet ligger i kraften
och numera också tekniken i presslaget.
I många av Thules produkter finns det plåtdetaljer, de flesta av dessa tillverkas i fabriken i Hillerstorp. Och här handlar det om takräckesprodukterna.
– På vårt företag arbetar vi med produktutveckling i fokus och den kringgärdas av sekretess. Av förståeliga skäl, så kan vi då inte visa upp nyutveckling, när det gäller design och konstruktionsförändringar innan en produkt kommit ut på marknaden av konkurrensskäl, så ingen fotografering av plåtdetaljer är tillåten, säger projektledare Viktor Huss.
Vi möter detta ofta i vår vardag då svenska företag ofta är i täten, när det gäller utveckling av nya produkter. Stora summor investeras i konstruktionsarbete och maskinparken. Och jag som redaktör ser det som positivt att vi ändå får komma in i fabrikerna och få en glimt av maskintekniken som används och hur man resonerar när det handlar om produktionsutveckling.
Idag är det pressverkstaden som investerat i en helt ny press från ZANI och det handlar om en servopress, den första på Thule Group i Hillerstorp men kanske inte den sista.
Från projekt till investering,
installation och produktion.
– Som vi förstår, så är trycket hårt på pressverkstaden för att hinna med att pressa plåtdetaljerna som skall monteras i olika typer av takräcken, ofta individuellt anpassade till vilket bilmärke eller modell som takräcket skall monteras på.
– Vi har ett långt samarbete med Olsons Maskinservice som levererat fem presslinjer till verkstaden, så det föll sig naturligt att vi tog upp en diskussion om en ny press. Man är dessutom en helhetsleverantör av service, support och operatörsutbildning, förklarar Viktor.
Vad var era tekniska krav på en ny maskin?
– Vi kände att vi behövde en större press än tidigare investeringar och en bordstorlek på 3 meter för att kunna bygga större verktyg. Även högre presskraft än tidigare för att kunna klara en plåttjocklek upp till 8 mm och bredd upp mot 800 mm.
– Att vi valde en servopress var även för att utveckla oss tekniskt och bli mer flexibla och kunna ta del av alla fördelar som kommer med en servopress i och med att man kan styra löparen på ett helt annat sätt.
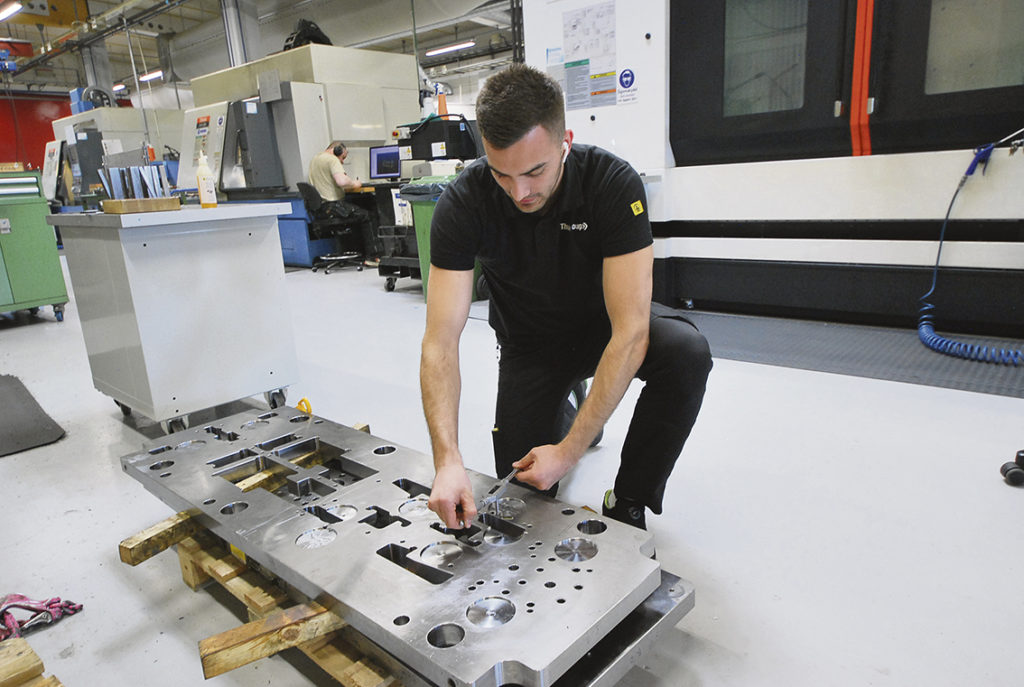
– Thule arbetar med samma krav som fordonsindustrin när det gäller att få ned vikt men samtidigt öka hållfasthet (säkerhet). Det innebär t.ex. nya materialval och med det följer helt nya presscykler för att klara form och funktion.
– Vi arbetar också med LEAN tänket i alla led och då föll det sig intressant när Patrik Olson presenterade maskinbyggaren ZANIs modellprogram av servopressar, säger Viktor Huss.
– Vill man vara med i toppen av teknikkedjan så är det i många fall en servopress som gäller. Det finns många fördelar med servopress, bland annat får kunden lägre servicekostnader, eftersom den saknar kopplingar och har få rörliga delar som kan slitas, säger Patrik Olson och fortsätter;
– Tekniken och kvalitén är på en högre nivå, bland annat kan du korrigera hastigheten på ett sätt som inte går i en mekanisk press och bygga egna presscykler som anpassas beroende på plåtdetaljens tjocklek, bandbredd och storlek på bordet.
– Det man nu ser är ett behov av att använda mer avancerade pressar för att kunna utveckla ny teknik och mer avancerade produkter samt att man börjar använda nya material med nya egenskaper som är svårare att forma. Servo presstekniken är nyckeln till att kunna göra mer avancerade och komplexa pressverktyg och styra presslaget med precision.
– Detta innebär att man kan ge konstruktörerna bättre möjligheter att produktutveckla och man kan blanda all teknik från tre olika presstekniker i ett verktyg och då kan man tillverka mer avancerade artiklar och verktyg för nya konstruktioner. En viktig poäng med servopressning är att man får bort vibrationer och man får bort stötar och servopressningstekniken sliter mycket mindre på verktygen. Man kör helt enkelt mjukare och tystare och detta halverar underhållskostnaderna på verktygen. Och man sparar pengar på en lägre energiförbrukning, säger Patrik Olson på Olsons Maskinservice.
Fakta Zani presslinje: Pressmodell ZANI SM400-S2-30-30.
Specifikation: Pressbord 3000 x 1500 mm. Slaglängd, max 300 mm. Hastighet 3-65 SPM.
Med bandlinje: TOMAC TLF5-800, kompakt linje med mätande riktverk och haspel. Max bandbredd 800 mm
Max materialtjocklek 6 mm. Max Coilvikt 5000 kg.
Leveransen var komplett med logistiklösningar för bandsmörjning, verktygsväxling skrot- och detaljhantering.
Återigen upphör man aldrig att förvånas över svenska verkstäder, deras nyfikenhet och framåttänk som gör dem konkurrenskraftiga idag och imorgon. Jag tar bilen hem till kontoret i Varberg och fylls av glädje och framtidstro, efter att ha besökt ytterligare ett världsledande företag med duktiga tekniker inom sin nisch.

– Verktyg slits och blir gamla och pga. vår ökade produktion, så ökar belastningen på verktygen. Så istället för att tillverka nya pressverktyg, så kan vi reparera en skada på kort tid med lasersvetsning och får därmed en längre livstid.
– Det kan handla om våra klippverktyg, stansverktyg och pressverktyg. Verktygen slits och då kan man reparera upp ytorna på verktygen med laser och det tillsatsmaterialet som passar, säger Joakim Kilén.