Roger Jansson, Joakim Heideman, Klas Nordh och Ulf Eriksson.
I bakgrunden ser vi RM12 motorn som har utvecklats för JAS 39 Gripen och det svenska flygvapnets behov. Idag används flygplanen i Sverige, Sydafrika, Thailand, Tjeckien och Ungern. Men som alla vet och som följer med i media vet att fler länder är intresserade. Motorn är en utvecklad GE F404 som har anpassats med enmotorinstallation. Produktionen startade tidigt 90-tal och fler än 200 flygplan levererades till svenska flygvapnet.
Det bubblar av aktivitet i flygindustrin igen, en ny produktportfölj skall fram, vilket gynnar flygmotortillverkaren och ger ringar på vattnet för en hel tillverkningsindustri. Nyligen tecknade bolaget ett 30-årigt avtal med amerikanska GE Aerospace om delar till flygmotorer. Avtalet är totalt sett värt 55 miljarder kronor och gör att GKN Aerospace kommer att behöva nyanställa 200 personer per år under de kommande fem åren.
Tidningens redaktör har fått äran att göra ett av mycket få möjligheter för fackpressen att komma innanför fabriksområdet som är välbevakat och kräver olika tillstånd för att kunna skriva en artikel, vilket har varit ett önskemål från redaktionen under många år. Spelreglerna är helt solklara och det betyder att vi får arbeta under restriktiva omständigheter som fotoförbud osv., vilket ändå blir mycket intressant. Vi skriver lite extra i detta nummer om gnistning och därför ska vi fokusera på det och till vår hjälp, har vi med oss Roger Jansson på Auran Industries som är leverantören av maskiner från japanska SODICK till olika produktionsenheter på GKN.
Men först till mer om GKN Aerospace som tillverkningsindustri. Vi tar hjälp av flera pressreleaser som företaget kommunicerar ut, dels från företagets hemsida, dels från andra källor;
” GKN Aerospace Sweden ingår i GKN Aerospace, som tillverkar motorkomponenter, flygplansstrukturer, kabinfönster, kablage och mycket mer till många av världens flygplan. Företagen i Aerospace-divisionen som arbetar med delar till flygmotorer bildar tillsammans Engines och vid vår anläggning i Trollhättan utvecklar och tillverkar vi avancerade delar till motorer för flygplan och rymdraketer. Vi arbetar även med motorunderhåll. Företaget har produktionsanläggningar i Trollhättan, Kongsberg (Norge), Mexiko och USA. Man har också ett ingenjörskontor i Bangalore, Indien och kontor i Stockholm (Public Affairs) och i Göteborg. Huvudkontoret för Engines ligger i Trollhättan, och där arbetar ca 2 000 personer.
”Varje gång man flyger, nästan var som helst
i världen, är det troligt att GKN Aerospace hjälper världens flygpassagerare på vägen. Vi utvecklar, tillverkar och underhåller delar till stridsflygplan och till stora civila flygplan, alltså passagerarplan med över 100 personer. Företaget designar och tillverkar även innovativa komponenter till rymdsystem. Man utvecklas ständigt, banar väg för ny teknik och utmanar sig själva för att bli bättre i allt man gör”.
Presstopp !
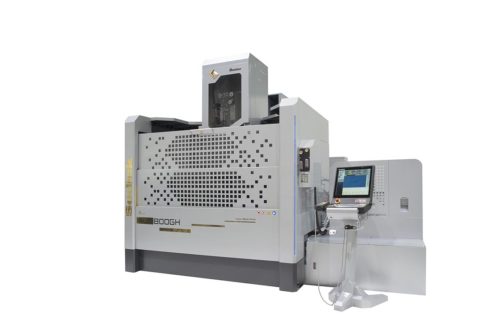
PRESSMEDDELANDE – 10 JANUARI 2024
GKN Aerospace investerar 600 miljoner kronor i mer hållbar produktion och erhåller mångmiljonstöd av Industriklivet
GKN Aerospace tar en ledande roll inom hållbar produktion och investerar 600 miljoner kronor i att industrialisera additiv tillverkning. Genom Industriklivet stödjer Energimyndigheten projektet med 152 miljoner kronor som kommer att bidra till minskad användning av råmaterial med upp till 80%. Den nya tillverkningsmetoden möjliggör ny effektivare design för framtidens motorer och kommer etableras i Sverige på GKN Aerospace fabrik i Trollhättan. Den nya produktionen beräknas tas i drift under 2024.
GKN Aerospaces metod kommer att kunna bidra till minskad användning av råmaterial och skapar möjligheter att förändra konstruktionen i grunden, vilket gör flygmotorn lättare och mer effektiv. Det här är första gången teknologin testas för denna storlek på komponenter och vi ser goda förutsättningar för spridning globalt och inom andra områden, säger Peter Engdahl, chef för avdelningen forskning, innovation och affärsutveckling på Energimyndigheten.
Flygmotorkomponenter tillverkas idag av stora gjutgods och smiden och med nuvarande teknik bearbetas upp till 80% av materialet bort innan komponenten får sin slutliga form. Med additiv tillverkning kommer produkterna i stället att byggas upp lager för lager av metalltråd eller pulver som smälts samman med hjälp av laser.
– Vi vill bidra till att minska flygindustrins påverkan på klimatet och vara en föregångare inom hållbar produktion. Vår produktionsteknologi är unik i sitt slag då man aldrig tidigare använt additiv tillverkning för så stora och komplexa flygkomponenter. Vi är oerhört glada över beskedet att den svenska staten stöttar denna satsning som bidrar till att vi etablerar banbrytande teknologi i Sverige, säger Joakim Andersson, koncernchef för GKN Aerospace Engines.
Stödet från Industriklivet bidrar till att GKN Aerospace väljer att etablera tillverkningen på sin anläggning i Trollhättan. Den nya satsningen med additiv tillverkning beräknas tas i drift under 2024 och kommer på sikt växa till fullskalig produktion. I framtiden kan satsningen innebära upp mot 150 arbetstillfällen åt operatörer, tekniker och ingenjörer.
GKN Aerospace har arbetat tillsammans med Business Sweden, Trollhättans Stad, Västra Götalandsregionen, Position Väst och andra aktörer för att investeringen ska etableras i Trollhättan.
Tidigare pressrelease;
GKN Aerospace köper Permanova Lasersystem AB för att bredda sin kapacitet inom additiv tillverkning (AM) för flygmotorkomponenter. Permanova Lasersystem AB kommer att tillhöra GKN Aerospace Engines nystartade affärsenhet och är ytterligare en företagssatsning kopplat till den gröna omställningen inom flygindustrin.
Göteborgsbaserade Permanova Lasersystem AB är ett ledande bolag inom avancerad laserteknik och industriell integration, som är en nuvarande leverantör av produktionslösningar för lasersvetsning och additiv tillverkning till GKN Aerospace. Förvärvet kommer att stärka GKN Aerospace:s förmåga av nya konstruktions- och tillverkningslösningar baserade på additiv fabrikation, påskynda storskalig industriell tillverkning av additiv tillverkning och möjliga framtida affärstillväxt.
Genom additiv tillverkning räknar GKN Aerospace med att kunna minska både energi- och materialåtgången kraftigt jämfört med dagens tillverkningsmetoder. Dessutom kräver ytterligare tillverkning helt nya lösningar som ytterligare kan bidra till flygets klimatomställning.
GKN Aerospace meddelade nyligen att man startar upp en ny affärsenhet inom sin flygmotorverksamhet, Engines, för att utveckla och erbjuda alternativa och mer hållbara materiallösningar. Det är en Game-Changer eftersom det kommer att göra det möjligt för företaget att snabba upp industrialiseringen av additiv tillverkning i stor skala.
Satsning inom AM -området som vi kan läsa om i ovan pressmeddelande betyder att man beställt ytterligare en trådgnist från AURAN och SODICK. Det handlar om en av de större trådgnistarma på marknaden och vi ber maskinsäljare Roger Jansson att förklara orderns betydelse för GKN Aerospace.
– Det är en investering i en SODICK ALC800GH som har ett intressant arbetsområde på
X-800 x Y-600 x Z-800 mm. Ett arbetsstycke på smått fantastiska L 1500 x B 1040 x H 800 mm. Det här är en av få trådgnistar som klarar av att gnista ett arbetsstycke på 800 mm höjd.
Alla Sodick ALC maskiner har som standard ett system som vi kallar iGroove.
iGroove roterar tråden under andra skäret och följande skär, på så sätt utnyttjar vi tråden runt om i stället för endast på en sida som vid konventionell trådgnistning. Detta ger en bättre ytfinhet, högre noggrannhet samt mindre trådkonsumtion.
– Trådgnisten skall användas främst för att skära loss printade material samt bearbeta stora och otympliga arbetsstycke, säger Roger Jansson på Auran Industries.
– För oss på GKN blir det inom det allt viktigare med 3D print och AM metalltekniken. Att byta ut utslitna flygmotorkomponenter kan bli en dyr historia. Delarna är ofta tillverkade i avancerade metallegeringar och har hårda säkerhetskrav. GKN har som ambition att försöka förlänga livslängden på de befintliga delarna och utnyttja de resurser som redan finns. Bolaget har utvecklat nya metoder för reparationer, bland annat med hjälp av additiv tillverkning som drar ner kostnaderna och ökar flexibiliteten. Man använder sig bland annat av automatiserad inspektion vilket förenklar undersökningen av komponenten, säger inköpare Joakim Heideman.
För tillfället byggs ett nytt verkstadsavsnitt på anläggningen i Trollhättan som ska fokusera på detta. Flera stora ordrar är bekräftade och GKN Aerospace räknar med att behöva anlita mer resurser. Så här har ni en del av svaret på varför man investerar i trådgnisten från SODICK, modell större.
Precisionsgnistning är en tillverkningsmetod som passar GKN Aerospace som hand i handske.
Maskinval inom precisionsbearbetning blir allt tydligare inom Aerospace industrin där gnistning sedan lång tid tillbaka har en tradition att medverka i allt fler tillverkningsprocesser och med en kirurgisk precision.
– Tekniken är optimerad för främst flygindustrin i ett större perspektiv och egentligen alla typer av roterande motorer i det lilla perspektivet, säger Roger Jansson expert på olika gnistmetoder och maskinteknik hos Auran Industries.
SODICK AQ400L
Detta är en äldre trådgnist med 12 år på nacken som är Klas Nordhs skötebarn.
– Det var här jag lärde mig trådgnista efter 24 år på andra avdelningar här på GKN. Klas har flera olika titlar;
– Han är produktionstekniker, teknikstöd för avdelningen, teamleader och skiftessamordnare, ja som du skriver, så förstår du att vi har lite problem med titlarna här, säger chefen för verktygsavdelningen Ulf Eriksson och alla skrattar högt.
Men trots alla titlar, så är Klas Nordh huvudpersonen när vi nu är bland maskinerna på verktygsavdelningen.
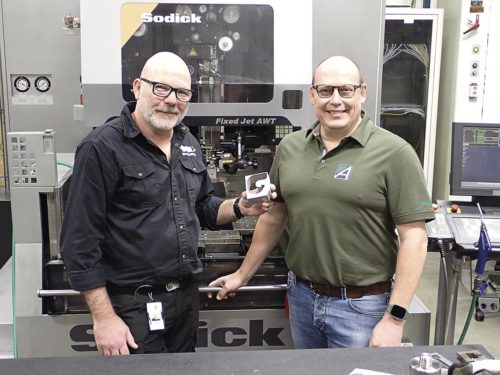
– Här tillverkar vi allt ibland nästan det omöjliga men vi skall inte överdriva det för mycket. Men trådgnisten kan och ska lösa kraven på detaljer med avancerade geometrier och höga toleranser. Ibland är det akut och ibland får vi lite mer tid på oss att förbereda oss. Det kluriga är uppspänningen, här behöver vi ofta tänka till och här kommer min/vår erfarenhet in.
– Och är det några problem så har vi en väldigt bra kontakt med Roger Jansson. Vi delar hela tiden erfarenheter med Auran, det är bara att ringa honom så får vi adekvat hjälp, säger Klas Nordh.
– Planering av körsätt är A och O. En detalj är sällan noggrann överallt utan man har vissa ytor, hål och styrningar som har kritiska mått. Har och får man kontroll på detta så har man kommit långt i sina gnist- och tillverkningsprocesser, säger Roger Jansson och Klas nickar.
Sodick AQ400L är en standardmaskin som jobbar med hög noggrannhet och tillsammans med linjärmotorerna i alla simultant styrda axlar har vi möjlighet att skapa de produkter som GKN Aerospace eftersträvar.
Nästa maskin står en bit bort på en annan ”liten avdelning” och då handlar det om SODICK AG100L sänkgnist. I den här maskinen kan vi placera ett arbetsstycke på 5000 kg och med maxstorlek på L 2100 x B 1250 x H 650 mm. SODICK AG100L har som alla andra av Sodick´s maskiner linjärmotorer för drivning av axlar. Dessa linjärmotorer producerar vi i egen regi från ax till limpa på våra fabriker i Japan samt Thailand, förklarar Roger Jansson.
Så slutligen frågar vi Klas Nordh hur man använder tekniken och till vad.
– Produktion givetvis samt olika typer av tester. Vi tillverkar mätbitar och vi tillverkar hållande verktyg för fixtureringar i våra gnistar samt ofta även för vår övriga maskinpark.
Bra att veta om gnistningens underbara värld.
Här följer lite information från experten Roger Jansson som vi fick åtnjuta under vårt besök på GKN Aerospace. Se detta som lite överkurs men intressant läsning i vilket fall tycker redaktören.
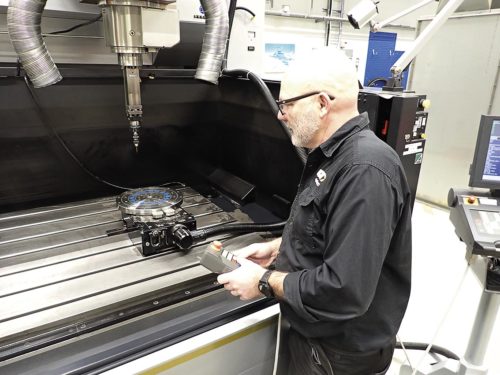
Visste ni att gnistmaskinen utvecklades på 1940 talet. Det var B.R. och N.I. Lazarenko som 1943 lyckades tygla en gnista och på så sätt sätta grunden till dagens gnistmaskiner. Det som gått fram mest genom åren är den så kallade ”vita zonen” eller den fördärvade ytan på arbetsstycket.
Går vi tillbaka 30 år så var den vita zonen flera 10-delar djup och full av sprickor. Med dagens gnistgeneratorer så vågar vi ligga närmare mellan elektrod och arbetsstycke vilket gör att gnistan blir kortare och mer kontrollerad.
Resultatet blir då att den vita zonen nu är nere på 1000-delar och det passar exempelvis GKN Aerospace som hand i handsken när de ska producera avancerade produkter i hårda samt svårbearbetade material.
Fortsättningsvis så ger kortare och mer kontrollerade gnistor även fantastiska egenskaper både i noggrannhet och ytfinhet. Vi kan skapa en gnistyta som i princip går att spegla sig i, säger Roger Jansson på Auran.
Mer om avancerade 3D-geometrier.
Med Esprit CAM görs det svåra lättare. Det betyder att Esprit skapar ett NC-program till trådgnisten från befintlig CAD-fil (produktionsritning). Hur går det då till. I Esprit skapar man ett NC-Program genom att markera de ”ytor” på soliden som ska bearbetas. Sedan genererar Esprit NC-koden inklusive de konditioner som krävs för att bearbeta detaljen, säger Mikael Tormod på Holotech och Roger Jansson Auran.
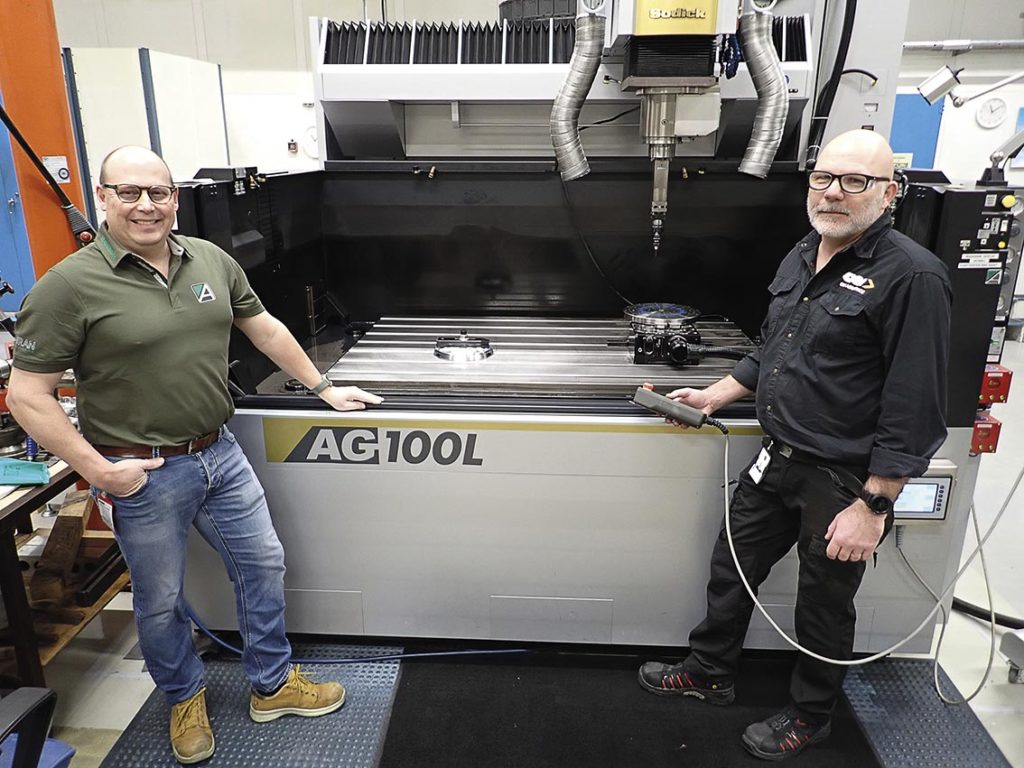