Produktionstekniker Robert Lundgren, produktionschef Lars-Erik Larsson Mastec och Lars Westin System 3R.
Höjd automationsnivå är en teknikutveckling som är i fokus vid verkstadsföretagets tunga maskininvesteringar. Tre identiska robotceller har fått produktiviteten att öka genom en hög maskinutnyttjandegrad och den stora potentialen är företagets standardiseringsarbete.
Tidningen Maskinoperatören hälsade senast på hos Mastec i oktober 2016 och nu var det åter dags för ett återbesök. Initierat av Lars Westin på System 3R, så hamnar vi mitt i en historia om tunga maskininvesteringar, dramatisk produktivitetshöjning och en maskinutnyttjandegrad i världsklass. Och allt började, kan man säga då Lars-Erik Larsson började som platschef, idag är han produktionschef. Han kom med lång erfarenhet från plåtindustrin och därifrån hade han med sig ett annat tänk.
Här får vi en liten resumé hur vi rapporterade vid vårt förra besök;
– Jag kom hit till Mastec konstaterades att maskinparken var lite eftersatt, hade gått många produktionstimmar och vad jag förstod då så hade våra konkurrenter investerat i nya maskiner och ny teknik, så vi kände att vi behövde se över vår verkstad. Då det var svårt att få fram ett relevant mätetal på maskinutnyttjandegraden, så bestämde vi oss för att börja mäta för att få reda på hur vi utnyttjade våra resurser, sa Lars-Erik Larsson.
– I samarbete med högskolan i Jönköping gjorde en av skolans studenter sitt examensarbete här och tillsammans med produktionsansvariga på Mastec genomfördes en noggrann analys där målet var att se om mer avancerade maskiner kopplade till automation kunde göra oss konkurrenskraftigare, berättade Lars-Erik Larsson.
Företaget såg att man började tappa i konkurrenskraft, det blev allt svårare att vinna nya affärer och det blev en utmaning varje gång att behålla affärer också, så koncernledningen beslöt att skjuta till pengar för att snabbt skapa ett incitament för en rejäl satsning på ett nytt produktionstänk – 5-axlig teknik med automation.
Och kravet var att hitta en standardiserad automationslösning som man skulle kunna utnyttja maximalt vid bl.a. parallell produktion. Små serier med snabba växlingar mellan olika artiklar, längre serieproduktion obemannad körning och ibland låta en maskin kopplas från robotcellen och köra manuell körning och den andra maskinen i automationscellen fortsätter med sina körningar, alltså en helt oberoende flexibilitet som kunde öka maskinutnyttjandegraden maximalt och framförallt minska ställtiderna rejält.
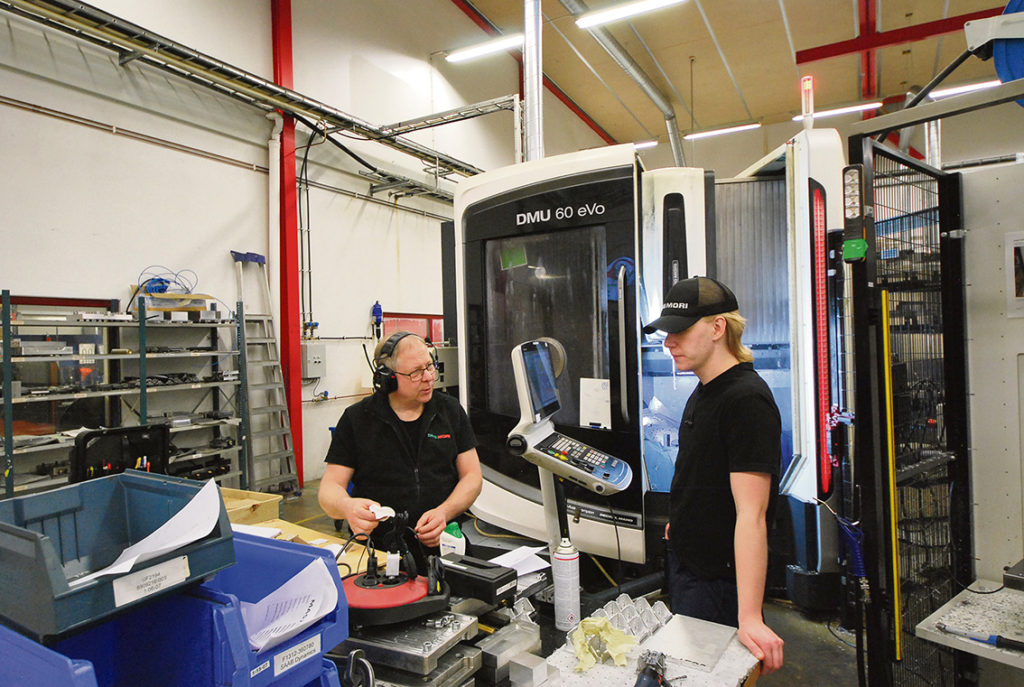
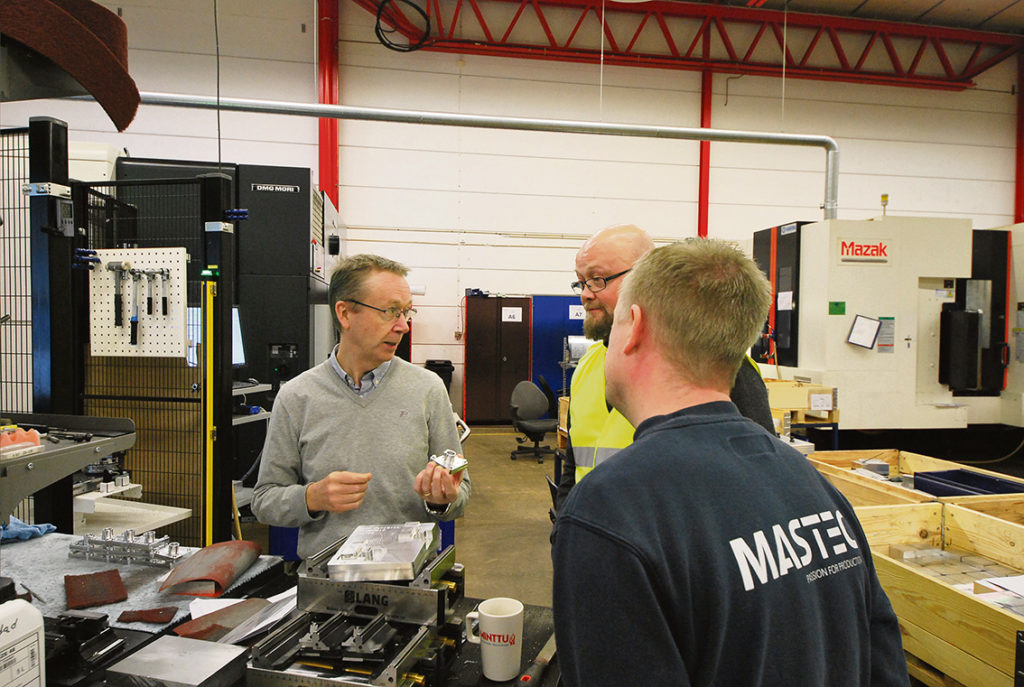
Efter noggrann analys av marknaden så fastnade man för en funktionell och flexibel helhetslösning som DMG MORI Sweden och System 3R presenterade tillsammans;
Mastec valde två stycken modell DMU 60 eVo, 5-axliga vertikala fräsmaskiner med samma optionsval på både och som står spegelvända mot varandra. Det ger en flexibel produktionscell där samma jobb kan köras är både maskiner.
DMU 60 eVo lämpar sig särskilt bra till automatisering tack vare palettladdning från sidan som betyder att robotcellen jobbar vidare vid riggning av en maskin.
Verktygsmagasin med 120 verktygsplatser ger möjlighet till en
permanent verktygsuppsättning som är likadan
i både maskiner. All programmering sker i ett CAM system och program
kontrolleras med en virtuell simulering.
Detta innebär NOLL riggtid vid maskinen.
Automationen består av robot System 3R Transformer med 150 kilo
lyftkapacitet, 2 palettstorlekar baserat på referenssystemet Delphin som har en
basplatta med
4 stycken chuckar i varje maskin som hanterar den stora paletten direkt och den
lilla via chuckadapter som roboten automatiskt laddar in vid behov. Varje
palett har ett ID-chip för identifiering. Varje chuck har 6 tons hållkraft och
systemet repeterar på 5 tusendelars millimeter.
Hela robotcellen körs med hjälp av System 3R:s mjukvara WorkShopManager som är utvecklat för maximal flexibilitet vid automatisering av få stycks produktion. Mjukvaran kan hantera både stora och små serier ända ner till en styck, man behöver inte köra en artikel i taget utan kan fritt blanda olika jobb lite som det passar.
– Vårt automationskoncept är modulärt och ger kunden möjligheten att bygga ut sin robotcell i flera steg om och när det blir önskvärt, säger Lars Westin.
Mars 2020
Ögonblicksbilden vi får idag är att Mastec nu har tre identiskt lika produktionsceller. Man investerade under våren 2018 i en cell till och under våren 2019 i ytterligare en cell, alla likadana – copy and paste !
På plats idag är Lars-Erik Larsson produktionschef och produktionstekniker Robert Lundgren från Mastec och Lars Westin försäljningschef System 3R. Som alla skall ge sin input om vad som har hänt sedan senast tidningen var på plats i Ulricehamn.
– Det har hänt mycket den senaste tiden och som sagts, idag har vi tre identiska dubbelceller. Och det är kopplat till vårt standardiseringsarbete kopplat till i och runt cellen. Och här har Robert Lundgren varit väldigt inblandad och drivande i det arbetet. Och det har resulterat i att vi idag har sex 5-axliga DMU 60 kopplat till 3 stycken System 3R celler och allting i maskinerna är identiskt lika och det handlar om att skapa en flexibilitet i vår fabrik, på en mycket hög nivå, säger Lars-Erik Larsson.
– Uppspänning, chuckar och verktyg allt är identiskt lika i de tre cellerna. Det gör att artiklarna som går i våra sex maskiner, kan faktiskt gå i alla sex maskiner utan att vi behöver göra programförändringar och processförändringar osv. Så stannar en maskin av någon anledning så kan vi med stor enkelhet flytta över till nästa maskin. Och i varje verktygsmagasin som har 120 verktygsplatser så har vi permanent riggat 65 – 70 standardverktyg, säger Robert.
– För oss handlar det inte så mycket om cykeltider utan det
primära är få ner ställtiderna och erhålla en optimal flexibilitet i våra
operationer där det ofta handlar om små serier runt 20 detaljer. Här har vi nu
fått en lösning som genererar fler order så vi kan växa. Och vi ser en helhet
i och runt automationen där vi jobbar med ständiga förbättringar och här ser vi
också hur våra operatörer växer i sin roll både kompetensmässigt och hur man
praktiskt sköter logistiken runt omkring cellerna. Praktiskt hur man förbereder
jobben med laddning av artiklar och plundring av färdiga komponenter, där vi
gifter ihop artikelnumret med ett maskinnummer och vi har fått ett riktigt lyft
tekniskt och kvalitén har förbättrats, säger Robert och menar att;
– Vi konstaterar också att företagets produktionstekniker som tidigare var upptagna med olika produktionstekniska problem och beredning/programmering, nu fått mer tid över till att ligga ett antal steg före, förhindra problem innan de uppstår vilket är en mycket positiv effekt och tillägger;
– Jag har jobbat här sedan år 2000 och idag är vi på en helt annan nivå när det gäller produktivitet och det kan vi tacka vårt standardiseringsarbete och vår satsning på helt automatiserad produktion. Alla har gjort ett jättejobb och vad som har hänt skall vi redovisa i nästa stycke av artikeln.
Förr och nu
Tittar vi tillbaka 7 – 8 år i tiden så handlade det om att man tillverkade detaljer i singelmaskiner, övervägande 4-axliga, ett jobb en maskin och där gick det alltid i samma maskin, mer eller mindre.
– Det fanns ingen standard runt varken verktyg, uppspänning eller fixturering. Det är klart att det fanns ett system som fungerade utifrån de förutsättningar som gällde då, säger Lars-Erik och Robert fyller i;
– Om man hade just den operatören som gjorde stället varje gång och man hade ”sin” maskin. Det handlade mycket om den enskilde operatören och dennes färdigheter som helst skulle ha fem års erfarenhet för att kunna lösa uppgifterna. Vi hade svårt att rekrytera personal med rätt kompetens men idag ser vi med vårt standardiseringsarbete att vi lättare kan få rätt kompetens kopplat till de arbetsuppgifter som en operatör måste klara av. Alla operatörer gör nu likadant, varje gång, t.ex när det handlar om fixtureringen. Alla vet vad som gäller och jobbar på samma sätt.
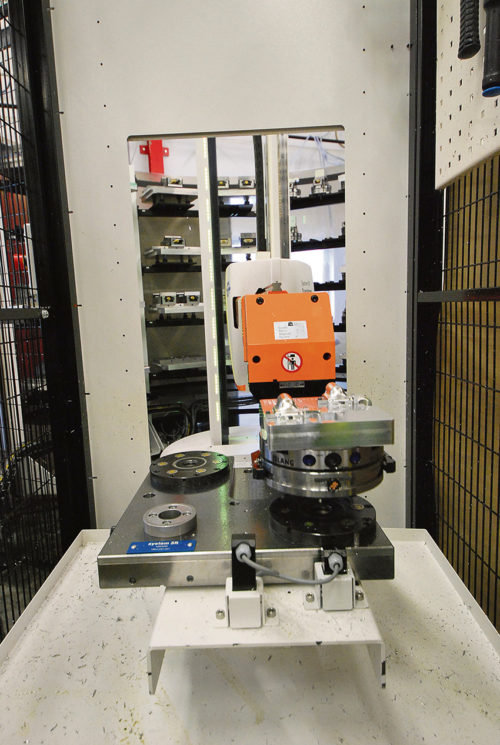
Vad har det gett i slutändan?
– Vi har som sagts infört en enkelhet i allt arbete vid maskinerna vilket gett en trygghet för våra medarbetare. Det har också gett oss en mycket högre maskinutnyttjandegrad, då maskinerna går hela tiden utan avbrott. Med hjälp av vårt standardiseringsarbete och våra stora satsningar på automation ser vi att vi i snitt har en maskinutnyttjandegrad som är uppemot 90 %, vilket är världsklass. Och risken att göra fel har minimerats.
– Det betyder en dubblering av produktiviteten i fabriken på fem år. Och här har företagsledning skapat förutsättningarna och personalen gjort ett jättejobb och skapat en referensanläggning som väckt stor uppmärksamhet utanför företaget. Vi brukar ibland ta med kunder hit till Mastec för att kunna visa och inspirera andra till att automatisera och standardisera, säger Lars Westin försäljningschef System 3 R.
Att automatisering skulle minska behovet av personal slår Lars-Erik och Robert snabbt hål på även om bemanningsfaktorn sänks så behöver man rekrytera personal tack vare ökade volymer.
– Vi har full fart och våra kunder finns främst inom Medical och försvarsindustrin. Vi skapar med detta upplägg ledig kapacitet för framtiden vilket ger en stor trygghet och tillfredsställelse.
– Nu jobbar vi vidare med vårt koncept och nästa steg är nu att börja jobbet med att standardisera våra svarvar, det blir en ny utmaning och mina arbetsuppgifter den kommande tiden, avslutar Robert Lundgren produktionstekniker på Mastec i Ulricehamn.
Slutligen vill Lars-Erik Larsson berömma System 3R för sin support och sin service.
– Den är och har varit fantastisk under denna tid på alla nivåer. Som exempel så hade vi ett stopp i produktionen på midsommarafton, vi ringde till Lars och felet blev avhjälpt samma dag, så vi kunde köra våra jobb under helgen, världsklass…
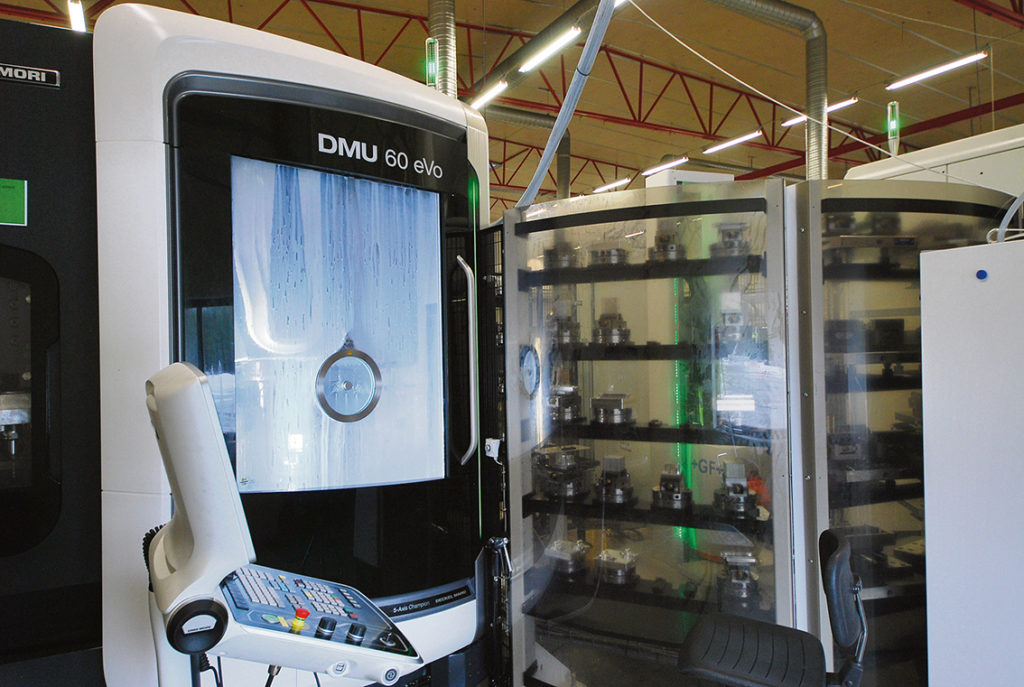
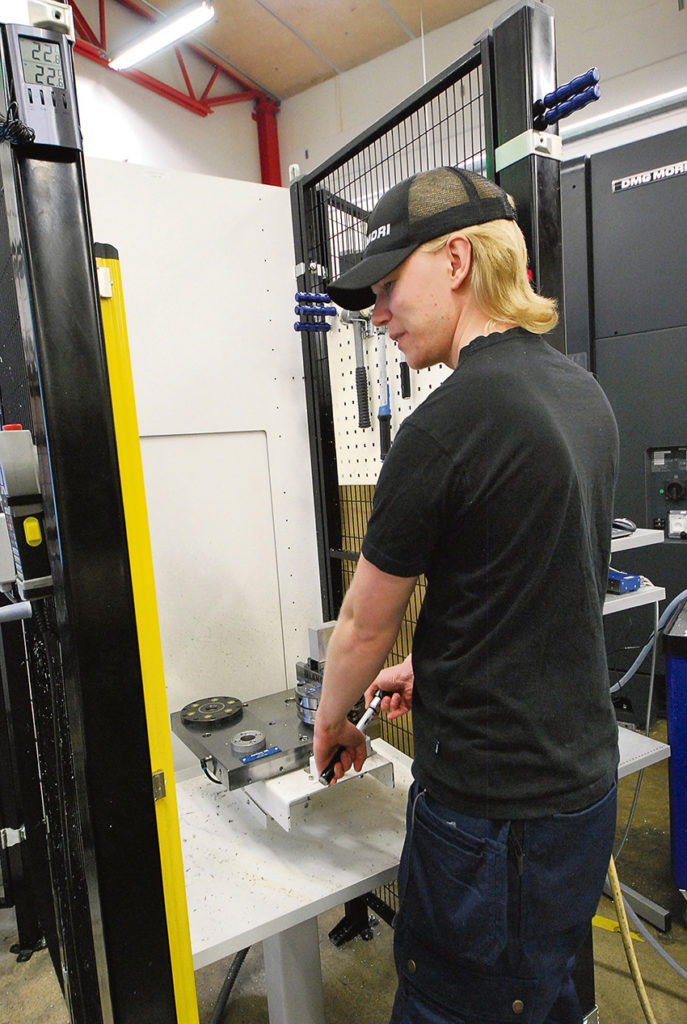