Wica Cold AB har investerat i ny fiberlaser från Salvagnini. Maskinen är installerad och tagen i full drift under mars-20. Företagets senaste tillskott i produktionen är en 4 kW fiberlasermaskin modell L5 med ett integrerat torn /materiallager LTWS samt Salvagninis patenterade helautomatiska staplings-/sorteringsrobot MCU, utvecklad av Salvagnini själva. Mer om maskintekniken och produktionstänket längre fram i artikeln.
WICA levererar kyl- och frysdiskar till färskvarubutiker. Ledord för WICA är ”long life design”, flexibilitet, snabbhet och närhet till kunden. Vid fabriken i Vislanda i hjärtat av Småland, finns produktion och utveckling samt teknisk support. Wica Cold AB etablerades i Vislanda redan 1957 där företaget grundades av Wilhelm Carlsson och den första produkten var så kallade frysfacksanläggningar.
Sedan 2005 ingår Wica Cold AB i Arneg-koncernen med gemensam produktutveckling och produktprogram. Produkterna som tillverkas i Vislanda bär namnet Arneg Nordic.
Wica Cold AB är idag 2020, 340 anställda varav 220 arbetar i produktionen i Vislanda. I bolagets plåtverkstad arbetar ett 30-tal personer, som producerar artiklar i en omfattande produktionsprocess sju dagar i veckan, dygnet runt. Arneg group representeras av ca. 3 300 anställda och finns i över 80 länder.
Med en konstant ökad orderingång sedan 2010 när Tidningen Maskinoperatören senast var på besök, så kräver det en ständig uppdatering av produktionsresurserna när det gäller ny teknik och maskinsystem för ökad produktivitet.
– Vi gör mer själva nu i fabriken med allt effektivare maskiner och arbetssätt. Vår policy och filosofi är att tillverka så mycket själva som är möjligt och med det incitamentet som vägvisare har vi även tagit hem en del jobb från externa leverantörer både från Sverige och andra länder, säger Gustaf Rosén.
Så företaget har under en längre tid varit och är inne
i ett mycket expansivt skede, vilket har gjort att man varit mycket aktiv ute på marknaden för maskiner och verktyg och aktiverat stora projekt för att göra produktionen så effektiv som möjligt.
– Vi på Wica Cold och med våra italienska ägare ser det som en styrka att ha kvar och utveckla produktionen här i Sverige och företaget satsar full fart framåt. Det uppskattas av våra kunder som ser resurssnål tillverkning och hållbarhet som viktiga incitament i sina inköp samt närhet till våra experter.
– Så vad jag menar är, att det ofta finns flera anledningar att fundera över att inte flytta produktion till ”låglöneländer” eller för långt bort. Vi tillverkar ”Made in Sweden” och det har gett oss en bra plattform för framtiden, säger Gustaf Rosén.
Dåtid
För många år sedan tillverkades företagets produkter med manuella kantpressar, excenterpressar och stansbord. Idag har maskinutvecklingen gett tillverkare stora möjligheter att med bättre maskinteknik få en helt kundanpassad produktion. Det är viktigt att minska produktionskostnader och med nya metoder kunna analysera, styra och effektivisera produktionsflöden inom tillverkningsindustrin. Företaget har lång erfarenhet av plåtbearbetning och de senaste maskininvesteringar ligger
i närtid och idag skall vi titta närmare på maskiner, system, automation och mjukvara- digitalisering från en av Wica Colds maskinpartner och leverantör Salvagnini.
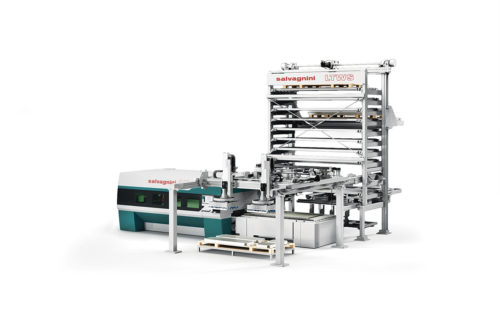
Fabriken i Vislanda
Är på imponerande 30 000 kvm. Här formas tunnplåt
i dimensioner 0,4 till 2,5 mm, oftast i spannet 0,4 – 0,7 mm.
– Vi investerar mer än gärna i maskinparken, säger fabrikschefen Gustaf Rosén och det är verkligen ett understatement, alla maskinaffärer har en bakgrund i ren expansion. Ibland fattas beslut snabbt och ibland tar det lång tid men alltid med en noggrann kalkyl bakom beslutet.
– När en maskinnyhet kommer ut på marknaden vill vi gärna vara bland de första på marknaden med utrustningen. Det höjer värdet till kunderna och personalen med arbetsledare, teamledare och operatörer blir inspirerade och får de bästa verktygen som finns på marknaden för att bli bättre i sina roller och det ger produktivitetshöjningar som ger oss bättre lönsamhet. Och har vi en bra lönsamhet så har vi trygga jobb.
Produktion möter sälj/teknik
Samarbete mellan företag är också samarbete mellan människor. Björn Ahlqvist säljande VD på Salvagnini Scandinavia och Gustaf Rosén teknikintresserad fabrikschef på Wica Cold ”bollar” synpunkter och tekniska fakta runt ett antal maskininvesteringar som gjorts de senaste åren på fabriken i Vislanda som ökat produktiviteten rejält. Vi tar det i kronologisk ordning.
– Från Salvagnini har vi sedan 2007 den första helautomatiska produktionslinje S4 stans- & klippcenter med integrerad P4 panelbockningsmaskin och sedan dess har vi investerat i en P1, en kompakt panelbockmaskin 2012, ytterligare en helautomatisk S4 stans- & klippcenter, panelbockningslinje 2018 och nu 2019 en cell bestående av en fiberlasermaskin med ett kompakt materialtorn med integrerad plockrobot för automatisk stapling av skurna detaljer. Allt finansierat här i Vislanda och enligt vårt måtto – ”Made in Sweden”, säger Gustaf.
Vi ber Björn ge oss teknisk input om maskinerna.
– Den elektriska panelbockningsmaskinen modell Salvagnini P1, är ”lillebror” till Salvagninis breda panelbockningsprogram, en kompakt maskin och ett komplement till befintliga panelbockningsmaskiner samt ett alternativ till traditionell bockning. Utvecklad för att få plats på liten yta, designad för att producera med en snittförbrukning på c:a 3 kW och utrustad med patenterad bocknings kinematik. P1 är en mycket bra lösning för verksamheter som arbetar i cellproduktion. Bred och blandad produktion och bockar en bock på mindre än 2 sekunder.
– Nästa investering 2018 handlade om en nästan identisk linje som 2007, helautomatisk stans-, klipp och panelbockningslinje; S4Xe.40 + P4L-3816.
– Det är ett 35 meter långt S4Xe.40 stans- och klippcenter (stanskapacitet till en längd upp till 4 200 mm), med ett MBT dubbeltorn med plats för upp till 52 fack med material, berättar Björn. Det är ett integrerat SMD som separerar och laddar plåt för plåt till själva stansmaskinen från det fack som ligger i kö i själva produktionslistan, vilket på så sätt möjliggör en flexibel körning av material/format/tjocklekar på ett optimalt sätt enligt behov. Efter stansningen har man även möjlighet att vända plåten före bockning som så erfordras, alternativt mellanstapla eller direkt matning till själva panelbockningsmaskinen P4L-3816, som bockar ämnen upp till 3 850 mm, som då automatiskt ställt in sig efter den detalj som ligger i produktionslistan.
Den nya produktionslinjen har många nya fördelar jmf med den gamla, då det hela tiden kommer nya idéer på utrustningar och körsätt, inte minst från våra högt krävande kunder, som hjälper till med utvecklingen, fortsätter Björn.
– Vi har nu två helautomatiska stans-och klipp panelbockningslinjer från den italienska maskintillverkaren Salvagnini och att valet föll på Salvagnini nu igen 2018, beror delvis på Wicas / Arnegs goda erfarenheter utav dem som maskinleverantör både här i Sverige och i Italien, samt deras kompetens inom fiberlasertekniken och den skandinaviska sälj- och serviceorganisationen, säger fabrikschef Gustaf Rosén.
Gustaf förklarar affären;
– Det fanns tre anledningar till att vi kopierade tidigare linje/cell och investerade i en till.
Dels att kapaciteten inte räckte till och att ingen annan legoleverantör kunde hjälpa oss med panelbockning av 4 meters plåt och tredje skälet är säkerhet. Om det blir stopp i produktionen så behöver vi backup då vi har en hög utnyttjandegrad i vår maskinpark. Vi kör dag, kväll, natt och helg och då finns det inga möjligheter att köra ikapp, dygnet har bara 24 timmar, eller hur.
– Vi gillar att uppdatera vår maskinpark till högsta och senaste tekniken som maskinbyggarna runt om i världen konstruerar och tillverkar och tar fram. Dessutom är det uppskattat av både vår personal och våra kunder. Visa upp att vi har egen produktion, det säger mycket om man ser mellan raderna, hur vi vill positionera oss på marknaden och vi säljer faktiskt ganska mycket på detta sätt att ha all utveckling, konstruktion och utveckling i eget hus, säger Gustaf Rosén.

Och tidningens redaktör tänker direkt på en stor tillverkare i Markaryd som verkar i värmebranschen, vars vd och koncernchef tänker på exakt samma sätt. Detta tänk är svensk produktions framtid.
– Vi har varit där på besök och man måste säga att de gör det bra, riktigt bra, säger Gustaf.
Och idag när vi på tidningen kommer på besök har man precis installerat och kört igång sin nya fiberlaserskärmaskin Salvagnini L5. Tekniska fakta överlämnar vi till Björn Ahlquist att berätta om;
– Salvagnini var först i branschen med att lansera fiberlaser (2D laser) på EuroBlech 2008, med olika former av automatisering, samt vår patenterade staplingsrobot MCL, numera uppdaterad till MCU, med nu ännu mer plockningsfunktioner, säger Björn Ahlquist.
– Idag ser vi en vidareutveckling i flera steg från 2008, där vi har en ny generation fiberlaser, både för L3 och L5, vilken är den högdynamiska fiberlasern från Salvagnini som vi nu installerat här på Wica. Den har extremt snabba förflyttningar tack vare en ”kompass” struktur med en dynamik upp till 5G vid körning av tunnplåt upp till 1,5 – 2 mm.
Den utrustning som Wica investerat i är med ett kompakt torn/materiallager LTWS med 10 fack, som är helt integrerat i maskinen och med Salvagninis patenterade plockutrustningen MCU, för automatisk stapling av de skurna detaljerna med de självprogrammerade plockrobotarna. Vidare är systemet anpassat för att skära med ”compressed air” vilket håller ner skär kostnaderna väsentligt, då energimässigt en Fiberlaser har extremt låg energi- och även gaskonsumtion. Vid körning på tunnväggigt material så lite som 10-14 kW/timma i snitt. Systemet i sig själv kräver ingen annan gas för kylning utan detta sker elektriskt med vår patenterade ”Dry cooling” teknik.
L5 hanteras med en helt ny mjukvara STREAM för att maximera produktivitet och Nesting, men också för att förbättra flödet i efterkommande operationer.
Plockroboten klarar av att hantera detaljer upp till 130 kg per styck utan några begränsningar gällande plåtarnas storlek. Allt detta på en yta mindre än 10 x 10 m här på fabriksgolvet hos Wica Cold.
Kommentar från Gustaf Rosén;
– Vi har nu sedan en tid tillbaka förstått fördelarna med fiberlasertekniken och vem skulle om inte vi ha en sådan här maskin?, ler Gustaf och nu var det dags att investera.
– Jag vill förtydliga till tveksamheten runt fiberlaser då vi tyckte att fiberlaser gick sakta om man tittar i backspegeln jämfört med stansning men vi såg nu stora fördelar på vissa detaljer när det gällde materialutnyttjande vilket är en stor bonus och givetvis så går tekniken allt snabbare och snabbare, plus att staplingen blivit allt bättre med åren.
– Dessutom är våra maskinoperatörer glada att man slipper skaka skelettet efter skärning, det är en arbetsuppgift som ingen vill jobba med.
Noll ställtid – Det gillar vi… som tillverkar produkter som skall formas i olika maskinsystem inom laser, bockning och klippning, säger Gustaf Rosén och utvecklar;
– Att ta steget in på laserskärning med fiber som är ett helt nytt område för Wica Cold så innebär det ett stort kliv mot en mer flexibel och kostnadseffektiv tillverkning. Och vi kan gå mer mot ”kit-produktion” (enstyckstillverkning). På så sätt kan vi hålla nere kostnader för lagerhållning och fokusera på att tillverka rätt detalj i rätt tid. För numera är all tillverkning i princip orderstyrd.
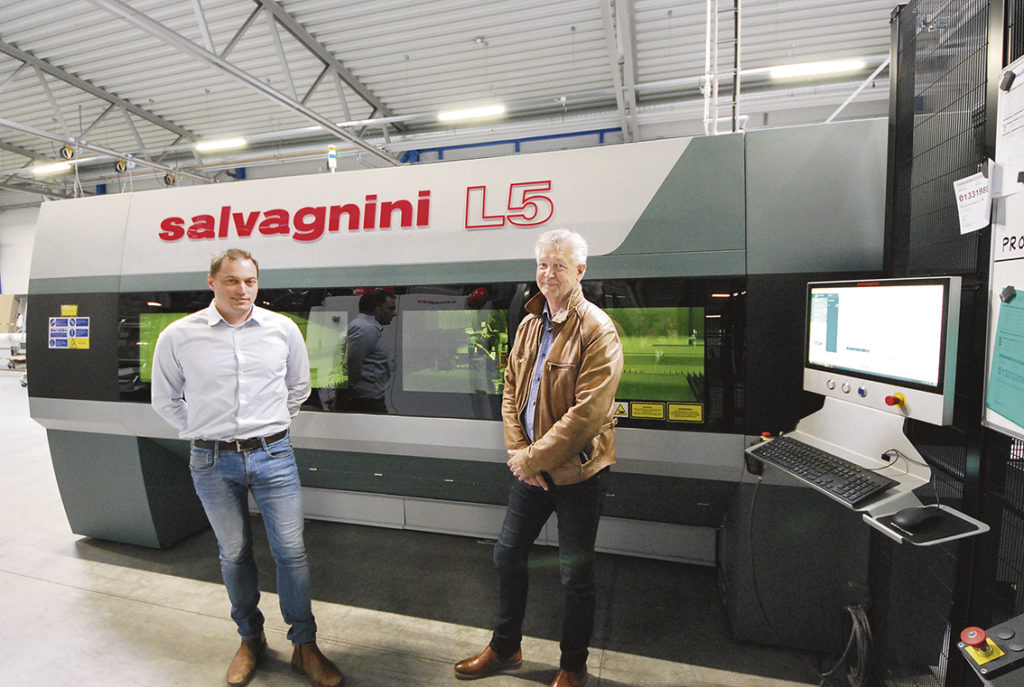
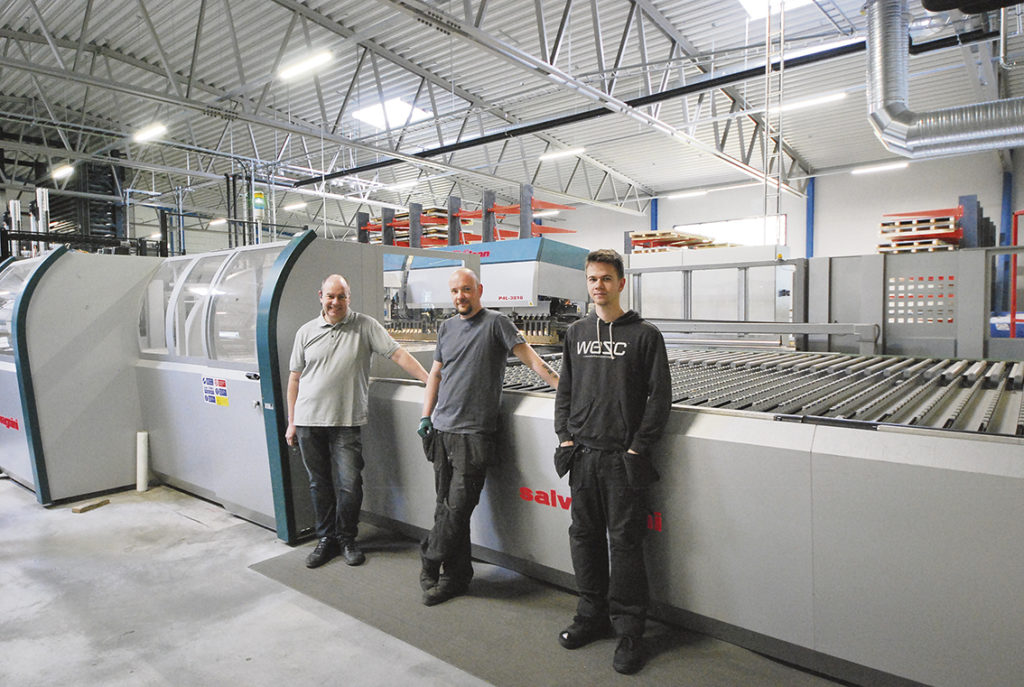
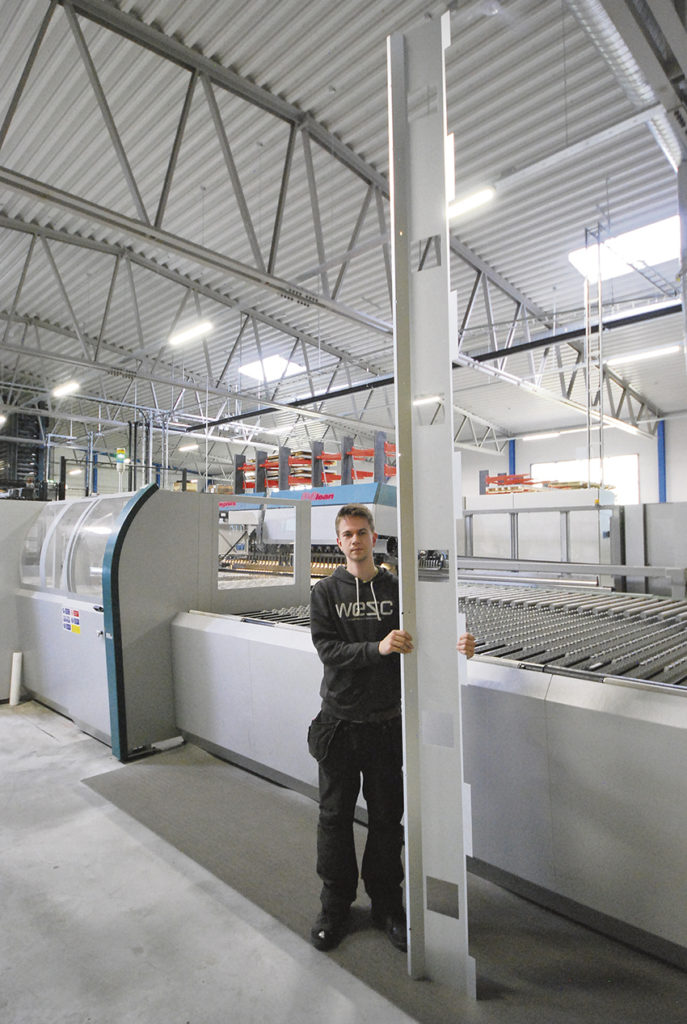
Produktionstekniskt tänk
– Vi kallar det internt för ”LEAN light” som betyder att vi gör inte LEAN bara för ”att”, i plåtverkstaden utan vissa plåtar kör vi enstycks direkt till monteringen (enstycks tillverkas mellan en till fyra timmar innan de behövs), (nu pratar vi just-in-time mina läsare, redaktörens kommentar.) och vissa kör vi i veckosatser. Från början när jag började arbeta här tillverkade vi halvfabrikat på diskar men med de italienska delägarnas intåg, så är allt som kommer ut från fabriken kundorderstyrt, allt vi tillverkar är sålt, säger fabrikschefen Gustaf Rosén.
– Trots all datostyrdstyrning i våra automationslinjer, så krävs mycket jobb, planering och tankearbete av våra medarbetare och utan duktig personal kommer vi inte framåt. Till min hjälp i produktionsplaneringen har jag sex arbetsledare som jobbar med beredning, programmering och leveranstider. Sedan är vi ett antal ”teamledare” som är som ”spelande tränare” som ser till att jobben flyter på och att det t.ex. finns material att forma och sedan har vi maskinoperatörerna som sköter maskinerna, säger Gustaf och fortsätter;
– Alla vi jobbar med ständiga förbättringar, jobbet blir aldrig klart.
Och i på jakten på det perfekta, så gör man alltid olika nesting hela tiden, oavsett om man kört detaljerna tidigare
Fabriksbesöket går mot sitt slut
Och avslutningsvis så ser vi den ”röda tråden” som är flexibilitet, styrkan i Salvagninis produktionstänk genom hela tillverkningsprocessen – med stort inslag av digitalisering/mjukvara och i förlängningen i princip noll ställtid.
– Maskinbyggaren Salvagnini är i grund och botten kända för sina stora produktionslinjer och idag erbjuder vi våra kunder allt smartare maskiner (även ”stand-alone”) med snabba automatiska omställningar, vilket lämpar sig för kit-produktion, det vill säga enstyckstillverkning med hög volym i små serier och snabba omställningar.
– Företag i tillverkningsindustrin brottas oftast med dyra omställningar – långa ställtider och seriestorlekar som har krympt i antal, men antalet order har ökat, vilket då ställer krav på mer automatiska inställningar, säger Björn Ahlquist.
Och här sätter Björn fingret på något viktigt;
– Vår filosofi har alltid varit mer automatik/robotik i processen och med våra produktionslösningar kan företag göra snabba omställningar som är så viktigt idag. Med våra unika mjukvaror kan vi synka ihop maskinerna som automatiskt genomför varje steg till färdig detalj. Ett exempel på det kan vara med vår ”Flexcell” bestående av en fiberlaser-panelbock-kantpress, där fiberlasermaskinen skär fram en plåt som sedan med lampsystem visar var detaljen ska bockas. Allt sker automatiskt och operatören behöver bara förflytta plåten, smart…
Ett smörgåsbord av teknik
STREAM
Den industri vi lever i idag, har förändrats: flexibilitet och effektivitet är grundläggande krav för att hantera allt mindre seriestorlekar och snabba ställtider. Salvagnini har de senaste åren av dessa anledningar utvecklat mjukvarupaketet STREAM som ett svar på detta.
STREAM är en programmeringssvit som förbättrar reaktiviteten, minskar programmeringskostnaderna, minskar driftsfel och ökar processeffektiviteten.
STREAM möjliggör en integrerad hantering på produktionsgolvet med samma interface oavsett teknik (stansning, panelbockning, laserskärning eller kantpressning). Planering-, programmering-, produktion-, ledning-, kontroll- och optimeringsbehov för hela produktionsprocessen tillgodoses från en enda plattform. Dessutom kan STREAM användas för att beräkna kostnaderna för produktionsprocessen även inkluderat uppströms- och nedströms processer om så önskas.
Salvagnini presenterade “Light out factory” redan 1985 då man var först ut med detta inom process system inom plåtbearbetning och man är fortfarande pionjären inom detta.
Med sin moduluppbyggnad av både maskiner och utrustningar med efterföljande system, har man möjlighet att med mjukvaran integrera olika maskiner successivt, för en optimal flödesprocess.
Vi jobbar nära våra kunder för att alltid hitta det optimala för varje enskild kund, där både kundens och Salvagninis visioner är målet för en framtida produktion, vi är inte bara säljare utan en “Doktor business” och långvarig samarbetspartner.
Salvagnini har och alltid haft högt ställda krav på sig själv och hela tiden kommer det nya innovationer och möjligheter, både vad gäller utrustningar till varje maskintyp, men även mjukvarustyrningar för dessa, så varje rörelse blir optimerad till det som skall utföras.
Inom panelbockningen är följande några exempel, bevis på detta och det är bl.a. Salvagninis patenterade MAC 2.0 (automatisk vinkelkompensering i realtid), CLA-SIM (flik bockning genom att bocka med en del av bock verktyget) vilket gör den till 100% helautomatisk och inte behövs ställas manuellt, detta ett måste för att klara av att producera ner till enstycksproduktion. ”CUT-option” som är industriell klipp/sax helt integrerad i bockningen, vilket är ytterligare ett exempel där man nyttjar även för extremt små eller smala detaljer, som annars är omöjliga att bocka med denna teknik.
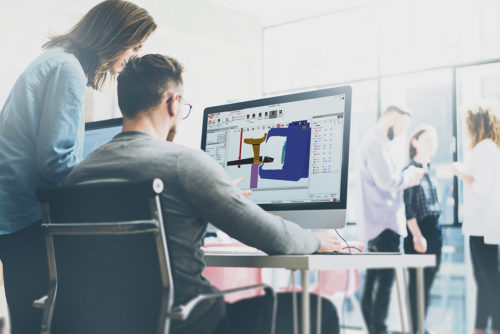
Salvagninis maskiner är idag med mer elektrisk och pneumatiskt utförande, där energiförbrukningen ligger i fokus. En panelbockningsmaskin idag med riklig utrustning, ligger på en energiförbrukning i snitt på c: a 4-9 kW, vilket är jämförbart med maskiner som levererades för 13-15 år sedan, som då förbrukade upp till 35-40 kW, beroende på utrustningsnivån. Här har tekniken tagit väldiga steg och vi ligger rätt till i tiden med vårt energi och miljötänk.
Allt enligt Salvagninis vision inom digitalisering om att skapa den smarta fabriken allt enligt Industri 4.0.
Mer information:
www.salavagnini.se
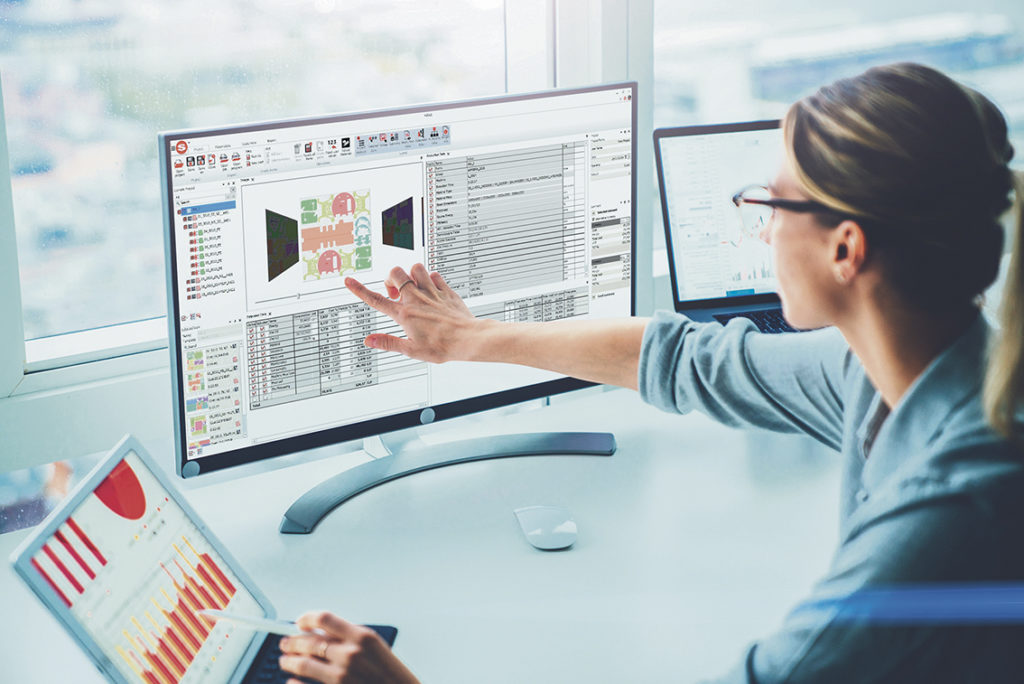
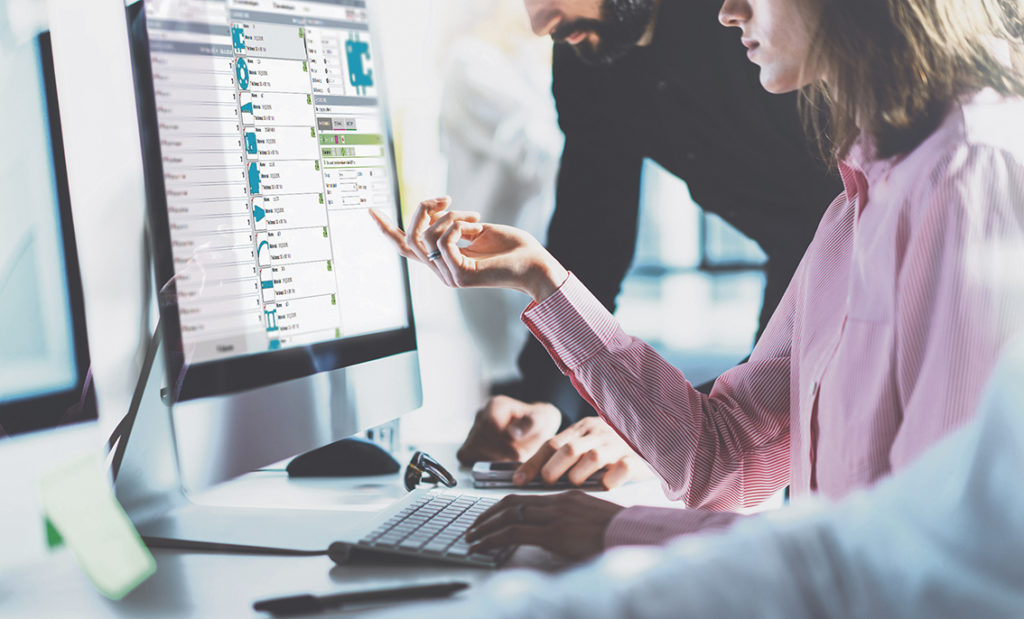