Hakfelt Produktion AB är legotillverkaren i Bräcke kommun som arbetar strategiskt, offensivt och långsiktigt. Med produktion och maskinpark inom gas- och laserskärning, skärande bearbetning samt svets.
Det går bra nu. Orderböckerna är fyllda och aldrig tidigare har företaget haft så många anställda. Just nu jobbar 60 personer på det familjeägda företaget i Bräcke.
Företaget ser som sagt en ökad orderingång. Man växer med sina befintliga kunder och när vi hälsar på i fabriken, får vi information om att företagets nyckelkunder aviserar om fortsatta ökningar framöver. Här kommer vi längre fram i artikeln att belysa att vägen fram till att kunna tillverka och leverera de ökande volymerna är att automatisera.
– Vi ska och måste fortsätta arbeta hårt för att behålla det goda ryktet som Hakfelt Produktion har byggt upp sedan starten av företaget 1991.
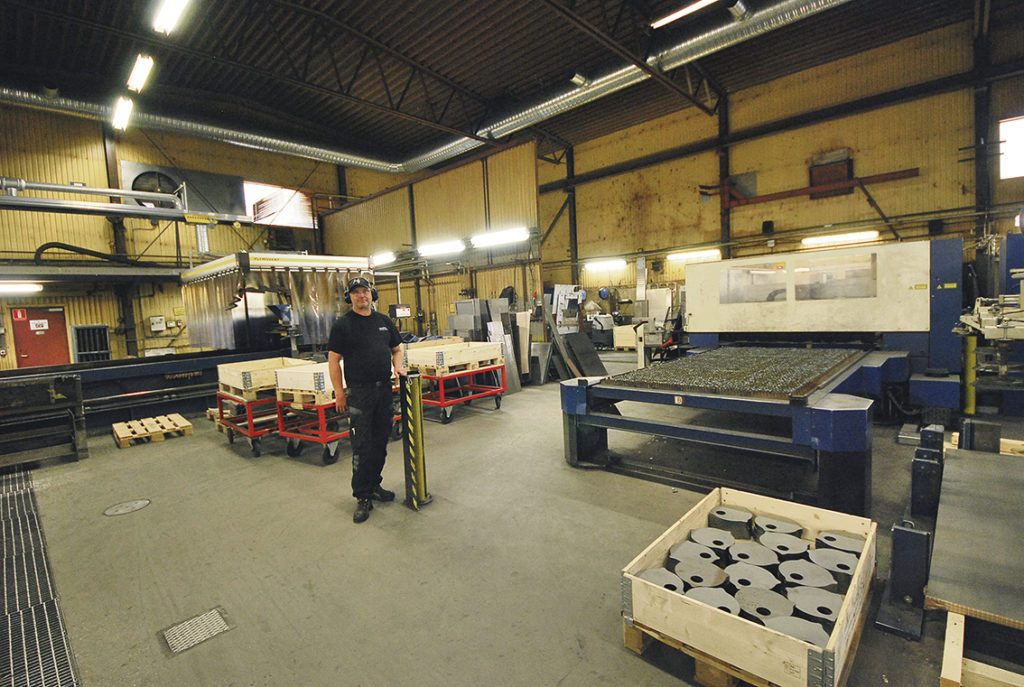
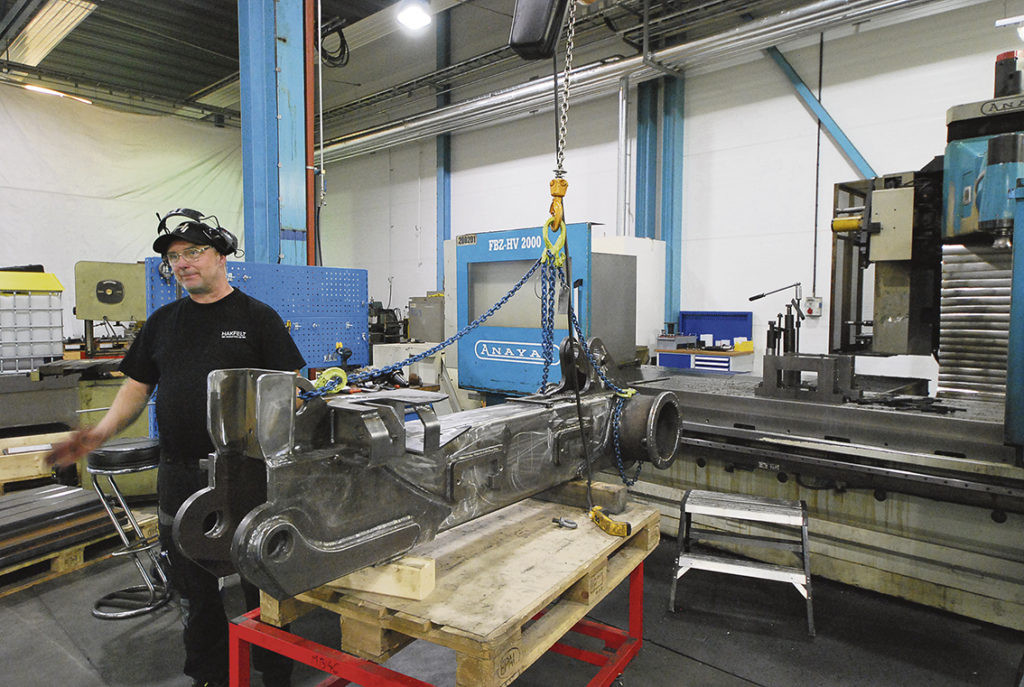
I produktionen har man flera laserskärmaskiner med kapacitet för 16 mm svartplåt, 8 mm rostfritt och 5 mm aluminium. Det som sedan ska bockas går vidare till kantpressarna som bland annat är utrustad med vinkelmätning. I gasskärmaskinen skär man upp till tjocklek 170 mm i plåtdimensionen 3 000 x 2 000 mm.
Avdelningen för svetsning består av svetsrobotar samt utrustning för alla normalt förekommande svetsarbeten. Alla svetsare är certifierade enligt SS EN-287. Avdelningen för skärande bearbetning består av fleroperationsmaskiner och konventionella maskiner. Man har även egen pulverlackering.
På foto till höger ser vi arbetsledaren flerop, Tommy Birgersson.
– Med den bristande arbetskraft som råder här i Bräcke och Jämtland i stort, måste vår bransch få upp intresset för den moderna industrin, hos framförallt den yngre generationen. Företaget fortsätter oförtrutet resan, att satsa på nya maskininvesteringar, effektiviseringar och optimering i produktionen, för att följa med i våra kunders utveckling.
– Vi ser ljust på framtiden, vi har en stark kundkrets, otroligt kompetent och trogen personal som vill fortsätta utvecklas, säger Pontus Hakfelt, som tillsammans med sin bror Fredric tog över företaget från sina föräldrar sommaren 2019.
Tidningens redaktör är på plats i Bräcke hos Hakfelt Produktion av en anledning. Aviseringar om ökade volymer för legoföretaget betyder att maskinkapaciteten inom den skärande bearbetningen behöver utökas.
– Det är avgörande för oss att våra kunder känner sig trygga i att vi kan leverera beställningarna på utsatt tid, berättar Fredric Hakfelt.
– Vi började bygga upp vår avdelning för skärande bearbetning för tio år sedan. Före det köptes all bearbetning externt. Den består nu av fem fleroperationsmaskiner från OKUMA varav flera är utrustade med palettsystem som går i skift. Vi kände det ökade trycket från våra kunder och hade inte svaret på hur vårt maskinutnyttjande såg ut och hur mycket kapacitet som fanns tillgängligt, säger Fredric.
Här finns ett stort mörkertal hos flera legotillverkande företag som säkert känner igen sig i bilden av att man ”tror” att man är effektiv i sina processer men när man väl tar tag i frågan så visar det sig att man ligger man på 50 – 60 % kapacitetsutnyttjande eller i värsta fall ännu lägre. Detta är ett stort problem för industrin men som tur är så finns det lösningar – automatisera i någon form.
Hakfelt Produktion gjorde så att man gick med i ett projekt som IUC Z-GROUP Jämtland/Härjedalen anordnar som heter Smart Industriell Modernisering. Projektet innehåller konsulthjälp där analyser görs direkt på plats hos företagen för att stärka konkurrenskraften med kunskapshöjande insatser.
– Här fick vi bra hjälp, fick dokumenterat många av de åtgärder som vi behövde planeras in och vad som behövde lösas direkt.
– Det blev som en ”käftsmäll” när vi förstod hur relativt ineffektiva vi var på flera plan, säger Fredric och Pontus.
– Så när det var dags att ta tag i ”problemen” så kom Covid-19. Vi drabbades som många andra men relativt snabbt (några månader), så kom kunderna och beställningarna tillbaka och fler order än före Covid-19 och det berodde säkert på att AB Sverige aldrig stängde igen som andra industriländer gjorde.
– Så den stående frågan var: Hur kan vi öka kapaciteten i fabriken inom den skärande bearbetningen? Göra nyinvestering i en maskin vilket blir väldigt dyrt eller hitta en annan lösning? Problemet är också att det är mycket svårt att hitta kompetenta maskinoperatörer, säger Fredric och fortsätter:
– Då är någon form av automationslösning en väg att gå, den vägen som vi visste var effektiv, då vi automatiserat både vår plåtbearbetning och vår svetsning i många avseenden.
Vår senaste investering gjorde vi 2018 i en OKUMA 630 som hade ”endast” ett 2-palettsystem. Vilket inte klarade av den volymökning som vi ser på lite större detaljer till våra trogna kunder som Bräcke Forest, Engcon, Komatsu Forest, Bucher Emhart Glass, Oilquick och Sund Birsta.
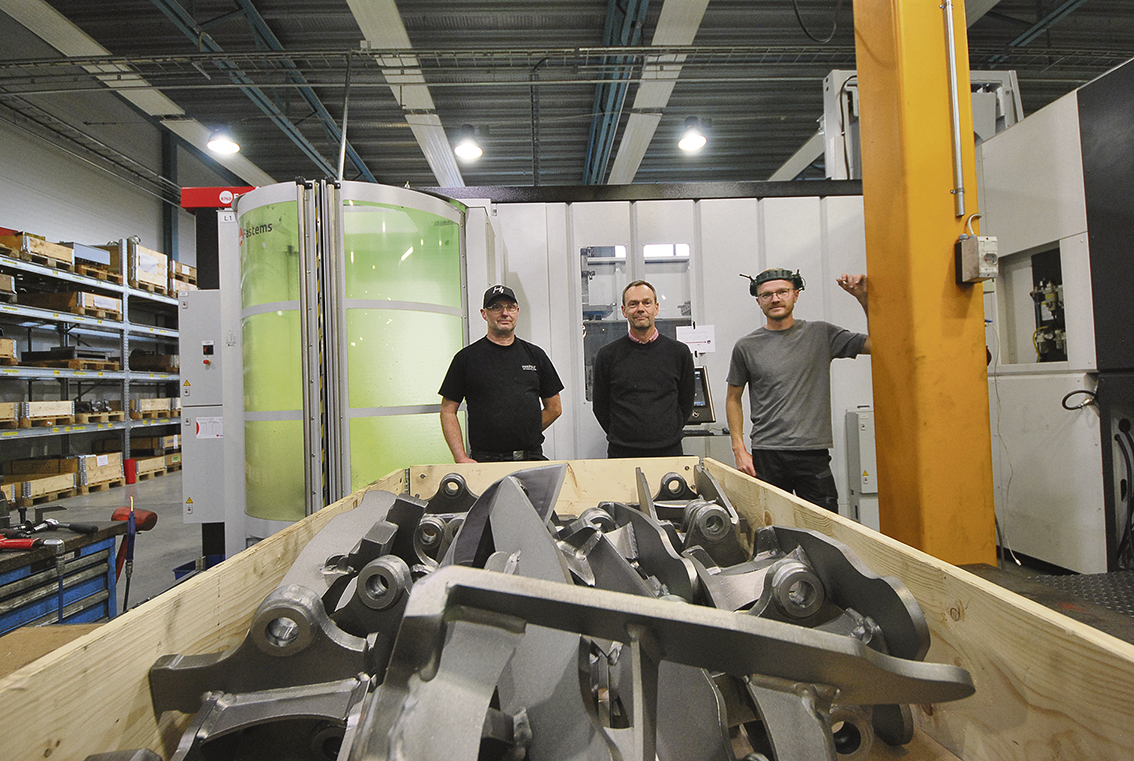
– Vi började sondera efter någon form av automationslösning och vi hade hört talas om och kände till att Fastems hade olika lösningar. Jag hade däremot inte varit i kontakt med dem. Vi pratade med vår maskinleverantör Stenbergs som rekommenderade oss att ta kontakt med Henrik Brodén på Fastems. Och det slutade i en lite unik men väldigt effektiv lösning på vårt problem där vi fick en mycket kostnadseffektiv och ”enkel” automation där vi ”dockade” vår OKUMA med ett Fastems containersystem som har plats för tio paletter, en helautomatiserad mindre FMS.
Och allt avslöjas i nästa stycke av artikeln där Henrik Brodén och hans medarbetare med världsledande produkter och mjukvara från Fastems, bakom sig och med kreativitet och engagemang fick till en lösning som inte är av det vanliga slaget, MEN mycket intressant…
Fastems löste ett problem igen…
Automatiserad produktion är avgörande för att svenska verkstadsföretag skall kunna hävda sig nu och i framtiden. Använder man automation och robotteknik på rätt sätt kan svensk tillverkningsindustri konkurrera med i stort sett vem som helst på den globala marknaden.
Här hos finska Fastems har vardagen ett fokus på produktivitetsförbättringar genom att helt automatisera tillverkningsindustrins hanteringsprocesser med målet noll i ställtid. Och i bakgrunden finns företagets yttersta mål, mantrat – 8760 – antalet timmar på ett år.
Fastems är ett företag som arbetar med att effektivisera processer och hitta lösningar när det gäller maskinbetjäning inom verkstadsindustrin, något som man har i sin stora produktportfölj.
– Med en effektiv automation kan vi tillsammans med våra kunder skapa välutvecklade automationsprocesser som skapar unika möjligheter, säger Henrik Brodén försäljnings ansvarig på Fastems AB.
– Vi kan idag erbjuda industrin en komplett lösning där FASTEMS tar ett totalansvar för automationen. Med egenutvecklad mjukvara kan vi styra hela processen med robotbetjäning, palett och fixtursystem via kran i små och stora FMS system, tillsammans med olika Tool Management (externa verktygsmagasin), AGV truckar, robotar, transportbanor osv. Allt styrs av vår egen mjukvara MMS som blir själva ”nervsystemet” i produktionen, ofta länkat till kundens ERP system och TDM system. Det kan handla om en stand-alone maskin som här på Hakfelts till att vi kopplar ihop flera maskiner i en cell, upp till att vi kan integrera hela fabriker. Där har du vår breda kompetens, säger Henrik Brodén och tillägger att man nu satsar resurser på sina lite enklare modulära system som skall ge även mindre applikationer en effektiv automation med implementerad mjukvara för hög produktivitet.
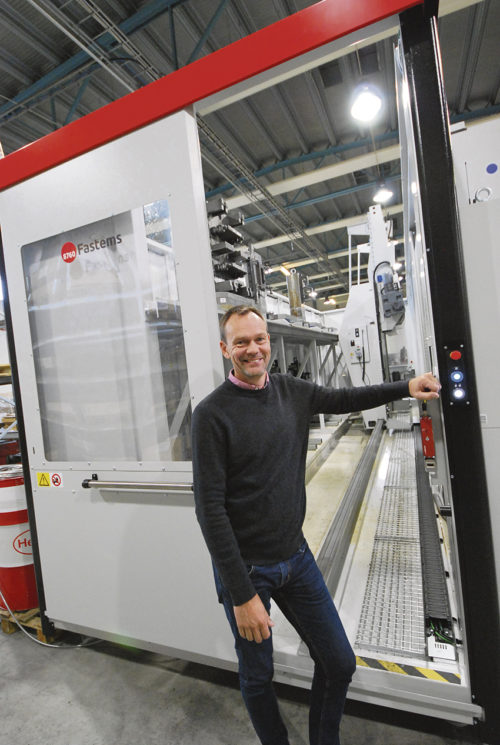
Och historien på Hakfelt Produktion i Bräcke, började egentligen med ett mejl i februari 2021
Henrik Brodén är givetvis med på mötet i Bräcke och han får berätta om den automationslösning som man tillsamman fann blev det optimala för Hakfelt Produktion.
– Kundens krav och målbild har vi fått redovisat av Fredric Hakfelt och det grundläggande var att hitta en lösning där man kunde effektivisera en redan befintlig fleroperationsmaskin med ett effektivt palettsystem. Och här var det viktigt att tänka till, säger Henrik.
Ofta när du och jag besökt och skrivit om Fastems produkter, så har det handlat om helt nya maskiner och lösningar där man investerat i en komplett bearbetningscell med högt automationsinnehåll på samma gång. Här hittade man en lösning som är lite annorlunda. Vi pratar om en befintlig OKUMA fleroperationsmaskin ute i produktionen från 2018.
– Produktionen har ökat med fler antal order och man behövde fler spindeltimmar per dygn och då kom vi på Fastems in i bilden. Vi tog efter ett gediget grundarbete med Fredric Hakfelt och hans team fram en lösning med att koppla på vår containerlösning för effektivare produktion, mindre ställtid och framförallt fler spindeltimmar per dygn, säger Henrik Brodén.
– Och givetvis kom helt naturligt fler frågor upp till ytan, är det genomförbart, maskinen är köpt som en stand-alone osv. Vi tog reda på vad som krävdes för att bygga ihop maskinerna till en automationscell. Mekaniskt var det ”bara” att häkta av dörrarna på fleroperationsmaskinens APC – 2-palettsystem och tillverka en ny frontplåt så att vår kranarm kommer in i maskinen, samt komplettera med ett elektriskt gränssnitt, säger Henrik.
Vi får lite tekniska fakta i och kring automationen
– Containern är en FPC 1500 (Flexible Pallet Container) med plats för 10 paletter. FPC är utbyggbar upp till 30 palettplatser och 3 maskiner, vilket gör att man kan växa med systemet i sin egen takt. Systemet styrs av Fastems mjukvara MMS, en mjukvara som bl.a planlägger jobben, ser till att utnyttja maskinen på bästa sätt, ligger ”steget före” och talar om när tex. verktyg skall underhållas – allt för att bli mer effektiv och inte tappa värdefull maskintid.
– Det roliga i sammanhanget här är vi i princip kontaktade varandra samtidigt, jag för att förhöra mig om intresset kring automation och Hakfelt för att få hjälp att hitta en lösning, det hela gick sen väldigt fort, från första kontakt till överlämnande på ca 4 månader, förklarar Henrik Brodén.
Resumé
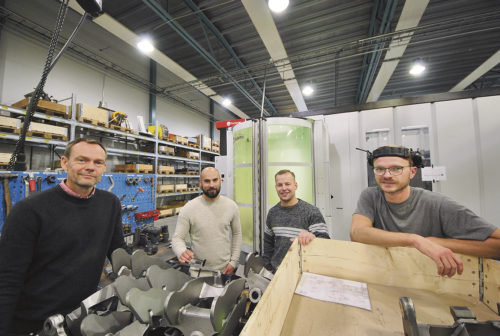
Så idag kan vi titta tillbaka på ett mycket lyckat projekt där alla parter är mycket nöjda.
– Vi litade fullt och helt på Henrik och hans medarbetare på Fastems under hela projektets gång, från planering, uppstart, installation och igångkörning. Vi rekommenderar verkligen ”tänket” med att komplettera en befintlig maskin med en containerlösning. Även ekonomiskt blev det ”mycket billigare” så här än att köpa en helt ny maskin till. På detta snillrika sätt kan vi öka vår konkurrenskraft, hålla våra leveranstider stabila och behålla jobben i Sverige, säger bröderna Fredric och Pontus Hakfelt.
Avslutningsvis frågar vi maskinoperatören Oskar Löfgren vad han tycker;
– Mycket effektivt och mjukvaran som styr automation är enkel med samtidigt smartare och mer avancerad än tidigare maskinstyrningar som jag träffat på. Det var lätt att lära sig. Detta blev verkligen rätt automationslösning för våra kommande behov. – Vi har halverat våra ställtider, får ut fler spindeltimmar och artiklar per bemannat skift men också ett bra utnyttjande, när det handlar om obemannad körning, nätter och helger.
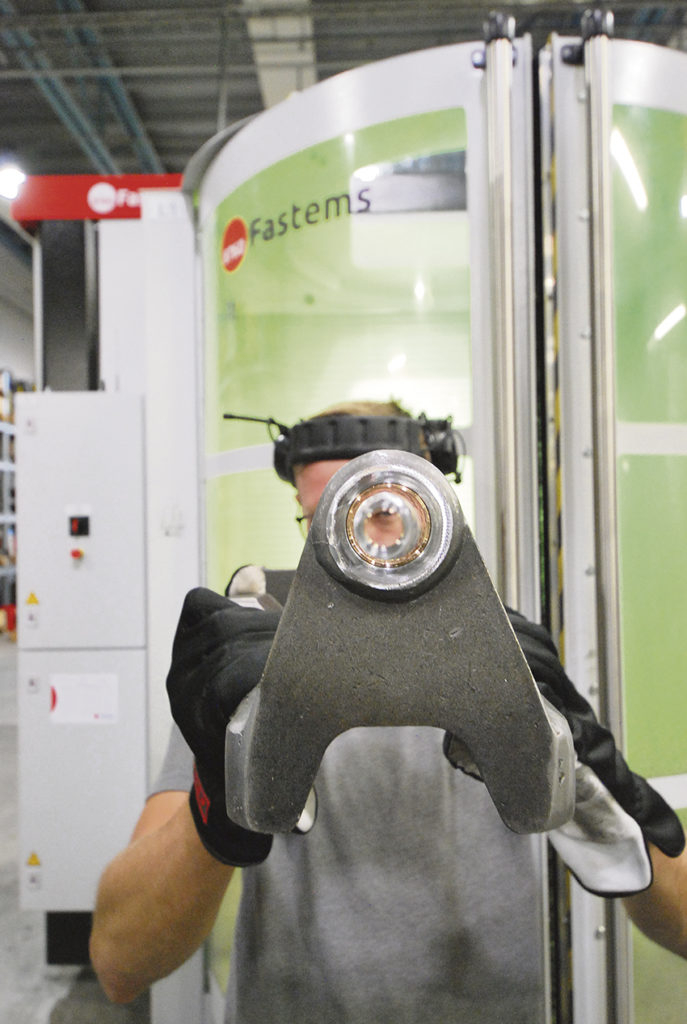
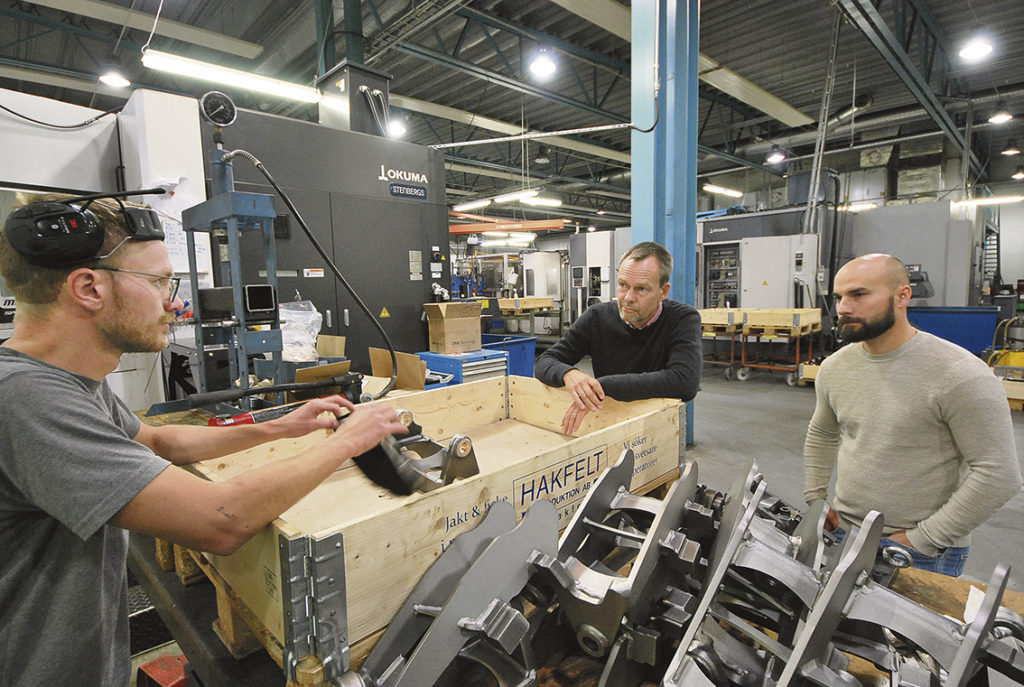