Fräsmaskin XXL
5-axlig fräsmaskin DMG MORI, DMU 210 P duoBLOCK, modell större på plats. Bearbetningsområde: X = 2 100 mm, Y = 2 100 mm och Z = 1 250 mm. Max bordsbelastning = 10 000 kg. Spindelhastighet max. 12 000 varv.
Investeringen i fabriken i Örkelljunga ger snabbare verktygsreparationer och garanterar i nästa steg kontinuerligt hög leveransprecision av formsprutade detaljer.
På bilden ser vi maskinsäljare Anders Wikström DMG MORI, maskinoperatör John Rolf och sittande underhållschef Lars Pedersen.
Maskinen kan hantera max 10 ton på arbetsbordet och kortar ledtiderna betydligt.
XXL även på verktygen
Det största formverktyget väger upp till 38 ton. Och att laga och justera ett verktyg av den vikten och dimensionen kunde tidigare inte genomföras i fabriken men idag löser den nya maskinen detta galant. Ett verktyg av denna kaliber är konstruerat i delar och på så vis kan varje del tillverkas, lagas eller renoveras var för sig.
Svensk industri ligger ofta i framkant när det gäller modern industriell produktframtagning och trenden är att tillverka mer i egen regi. Nu ser allt fler svenska verkstadsföretag en uppsida i att ha produktion och sin försörjningskedja närmare sina kunder. Förändringar har skett de senaste åren och Covid 19 pandemin har gjort att tillverkningsindustrin tänker mer in än ut. Outsourcingspöket syns alltmer sällan. Hållbar produktion i olika former och miljötänkande blir allt viktigare och frågan som allt fler företag ställer sig är att produktion och marknad måste komma närmare varandra. Svaret är ja.
Så även för verktygsmakeriet på KB Components i Örkelljunga. Det är inte lönsamt att skicka tunga formverktyg för förebyggande underhåll, ändringar samt reparationer som transporteras kors och tvärs i Europa ur ett hållbarhetsperspektiv men också så är en annan faktor inblandad och det handlar om tidsaspekterna.
– Vi har stora volymkunder inom tung och lätt fordonsindustri och här är det ” Just-in-Time” som gäller för leveranser av våra tekniskt avancerade plastkomponenter som går direkt in i våra kunders monteringslinjer. Vi har ett visst veckolager men ofta ligger lagret på lastbilen, på väg till kundernas monteringsfabriker. Det får helt enkelt inte stanna, då är vi illa ute, allihop, förklarar underhållschefen Lars Pedersen på KB Components.
Produktionslokalerna har byggts ut för att hantera stora formsprutningsmaskiner, omfattande investeringar har också gjorts
i verktygsverkstaden för att på ett effektivt sätt kunna hantera stora verktyg. Så investeringarna är en del av satsningen i nya maskiner från DMG MORI och SODICK, en naturlig följd av företagets utveckling i det större segmentet av plastkomponenter.
– Vi strävar efter att produktionens- och verkstaden utveckling ska gå hand i hand. Den nya fräsmaskinen kan hantera formverktyg upp till 10 ton på sitt arbetsbord, vilket gör att vi nu kan ta hand om alla verktygsdelar internt. Räcker inte det till så har vi investerat i en sänkgnist som klarar av att bearbeta i verktyg upp till 15 ton, säger Per Möller, inköpare på KB Components.
Vi återkommer med mer information längre fram på sidorna 62 och 64 i artikeln om investeringarna, för här pratar vi fem nya maskiner för ett ordervärde på 35 miljoner kronor och vilka som är maskinleverantörer.
Bakgrund
Alla företag har en historia och Konstruktions-Bakelit grundades i skånska Åsljunga 1947 av Anders och Solweig Månson. Andra världskriget var över och det var ont av det mesta som kan behövas i ett samhälle i form av varor och material. Detta faktum blev starten för Anders och Solweig, då 22 år gamla att starta ett företag med fokus på produkter tillverkade av bakelit. Så med 15 000 kronor i startkapital och tillgång till ett garage vad allt som fanns att tillgå i starten av företaget.
Lite kuriosa är …att handlingen i Max Lundgrens böcker om Åshöjdens BK utspelar sig i Åsljunga, som
i böckerna fått namnet Åshöjden.
Mer kuriosa… Diamanter är för evigt är ett talesätt och Bakelit varar också för evigt, det påstod Leo Baekland, en belgisk kemist som utvandrat till USA. 1907 uppfann han bakeliten, världens första helt syntetiska plastmaterial. Ett material som genom sin tålighet och formbarhet i många sammanhang var bättre än naturmaterialen.
Källa: Wikipedia.
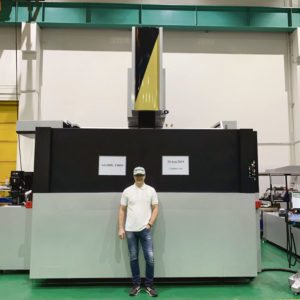
Den första maskinen var en manuell Bakelit press tillverkad av ett företag i Hässleholm. De första produkterna var muggar till termosar som Termoverken i Jönköping tillverkade. Nu är vi inne på 50-talet och man är 10 anställda och produktsortimentet växer.
1967 kom ett av de stora genombrotten för företagets produkter, då man började tillverka värmesystem till nya SAAB 900. Det gjorde att man behövde expandera sin verksamhet och 1971 flyttade Konstruktions-Bakelit in
i en helt ny fabrik i Örkelljunga på 11 000 kvm.
Framgångarna fortsatte och under 70-talet datoriserades företaget och allt fler produkter tillverkades nu till SAAB 9000 och Volvo 700 modellprogram.
Under 80-talet utvecklade man en egen produkt som fick namnet KB Elsystem. Och 1983 fick man besök av kungen och drottningen under deras Eriksgata.
Den första riktiga motgången kom när SAAB såldes till GM 1989, då var det slut på affärerna. GM hade sina globala partners. Men in på 2000-talet ökade samarbetet och volymerna med Volvo som lanserade nya modeller bl.a XC90 SUV. Företaget KB utvecklades och fann nya metoder och produkter som gjorde att man expanderade. Ett nytt bromssystem från Haldex blev ett nytt samarbete och en ny kund.
Under 90-talet transformeras KB från komponentleverantör till att bli en systemleverantör. Företaget utvecklar och tillverkar klimatsystem för fordonsindustrin. Andra produkter var komponenter för mobiltelefoner och radiatorlock.
Finanskrisen 2008 satte sina djupa spår i all affärsverksamhet över hela världen och det resulterade i att KB fick nya ägare i BRA Invest och företagsnamnet ändrades till KB Components.
Under 2010-talet har KB en snabb tillväxt med nya kunder som FM Mattsson, Thule och Kinnarps. Man etablerar fabriker i Mexico, Kina, Slovakien och Canada. Man startar även samarbete med lastbilstillverkaren Scania. Och idag 2020 har man nu gjort stora investeringar i sin fabrik i Örkelljunga både i byggnader och maskinutrustningar.
Så från lokalt till globalt, utvecklingen har varit och är enorm om man tittar de 70 åren tillbaka fram till dagens företag.
Idag är KB Components är ett globalt växande företag inom utveckling, produktion och försäljning med en rullande omsättning på ca 1 200 MSEK med ca 800 anställda, där visionen är att vara världsledande avseende tekniskt avancerade polymera produkter.
Företagets tre övergripande målsättningar är tillväxt, lönsamhet och trivsel, inom vilka man aktivt arbetar för att bli ett av världens bästa plastföretag. Huvudsakliga kundsegment finns inom sju olika affärsområden som fordonsindustri, möbelindustri och belysningsteknik m.fl. Där KB Components tillverkar ett brett urval av komponenter för både interiöra och exteriöra applikationer.
Man är idag en blågul världsspelare
– Under de senaste åren har vi upplevt en mycket positiv utveckling och vi står i en stark position att möta framtiden. KB Components har en hög teknisk kompetens och en bred erfarenhet från många olika branscher. Företaget behärskar de flesta tekniker och material inom det polymera segmentet, vilket gör oss till en pålitlig och ansvarsfull partner. Genom organisk tillväxt och förvärv, har vi uppnått en väl avvägd produkt- och kundportfölj, vilket gör oss mindre konjunkturkänsliga.
– Vi har produktionsanläggningar runt om i världen. Idag är vi en av Skandinaviens största aktörer inom avancerad plastproduktion och erbjuder tillverkning i moderna och högteknologiska produktionsanläggningar. Vår strategi är att vidareutveckla vårt samarbete med våra kunder, både när det gäller befintliga och nya marknader. KB Components ser ljust på framtiden, sa vd Stefan Andersson i ett pressmeddelande nyligen.
Och som man från företagsledningen betonar; ”Med vår nya fantastiska maskinpark som är unik, kan vi nu erbjuda svensk verkstadsindustri ledig kapacitet inom legotillverkning. Vi söker nya kunder. Hör av er så kan vi se vad vi kan erbjuda”.
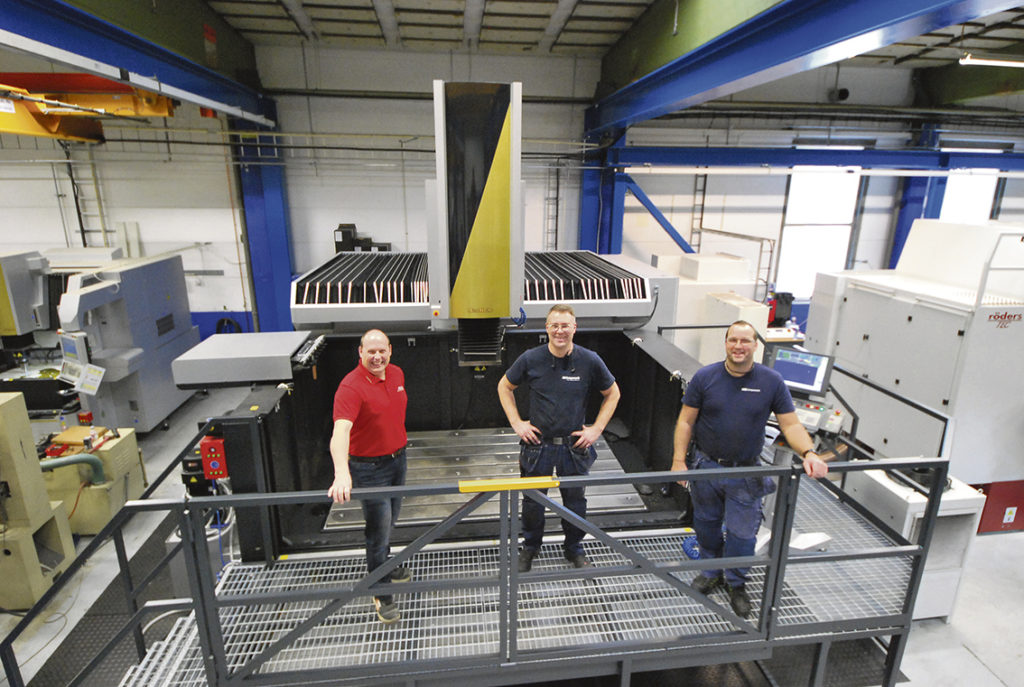
Sänkgnist XXL
En av Europas största gnistar står på plats i Örkelljunga sedan hösten 2019. SODICK AG200L är den största sänkgnisten som man har byggt och maskinen med serienummer T-0001 står nu i Sverige, det är häftigt och ger avtryck i hela världen. Det betyder att KB Components beställde maskinen när den endast fanns på ritning.
På bilden ser vi Roger Jansson maskinsäljare Auran Industries, verktygsmakarna Christian Nilsson och Mikael Jansson KB Components.
På SODICK AG200L är allt XXL. Vattentanken 5 000 liter. Bearbetningsområde: X = 2 000 mm, Y = 1 250 mm och Z = 800 mm. Max. bordsbelastning 15 000 kg! Och maskinen är större än man ser då den är nedsänkt ½ meter i marken.
Och idag skall vi titta närmare på verktygsverkstaden i Örkelljunga.
KB Components verktygsmakeri är med de senaste maskininvesteringarna en toppmodern anläggning som utför förebyggande underhåll, ändringar samt reparationer av formverktyg både för interna organisationen samt för externa kunder.
KB Components i Örkelljunga har växt rejält de senaste åren och har idag formsprutor ”XXL” med 2 300 till
2 700 ton i låskraft och här pratar vi investeringar i en ny produktionshall, maskiner och automation på närmare 80 miljoner.
Det största formverktyget till dessa väger 38 ton. Att laga och justera ett verktyg av den dimensionen kunde tidigare inte genomföras i egen verkstad men med den nya maskinparken i den nya lokalen, löser företagets verktygsmakare detta galant.
– Vi är starka idag och få knäpper oss på näsan. Som företaget skriver officiellt, så vill vi försöka att bli en av världens bästa plastfabriker, säger Lars Pedersen stolt.
Ribban är satt högt må jag säga, fantastiskt roligt för svensk verkstadsindustri.
Anders Wikström maskinsäljare på DMG MORI berättar;
– Att hitta rätt maskin för rätt applikation kräver långsiktiga investeringsplaner. KB Components tog kontakt med mig någonstans runt omkring 2016. Först handlade förfrågan om lite mindre maskiner. – Jag var på flera möten med inköpsavdelningen och vi gjorde flera referensbesök i Sverige och då framförallt ner till Tyskland och fabriken i Pfronten. Dels efter mycket förhandlingar valde man då en fräsmaskin DMG MORI DMU 75 monoBLOCK och en DMG MORI DMU 210 P duoBLOCK och den sistnämnda efter att ha ångrat sig då man först valde en DMU 160 P, alltså modellen mindre.
– Kravet var utöver de vanliga kraven att maskinen kunde ta 10 ton på bordet. Vi studerade marknaden noggrant och tittade på flera fabrikat som utmanade DMG MORI men efter resan till fabriken i Pfronten så var vi nästan så säkra vi kunde vara, fabriken var mycket imponerande, säger Lars Pedersen som tillsammans med maskinoperatören John Rolf var med på referensbesöket.
– Verktygsverkstaden här på KB Components hade tidigare fräsmaskiner äldre sådana från Deckel och dem var man mycket nöjda med så tysk maskinbyggarkvalitet var ett stort argument för maskininvesteringarna som skedde.
– Jag har alltid gillat Deckel efter mina många år som fräsare. Speciellt nu 210:an som är stor och häftig, bra ergonomi för oss operatörer och väldigt fin design, säger John Rolf.
Underhållschefen Lars Pedersen som är den som håller ordning och reda på verktygsmakeriet. Med anställningsstart 1993, så förstår vi att Lars kan företaget på sina fem fingrar.
– Dessutom arbetar jag just nu, även som verkstadschef. Tittar vi i backspegeln så var det så att när jag började arbeta här så byggde vi verktygen till oss själva och hjälpte även andra företag, så vi har varit ett verktygsmakeri här på platsen i snart 30 år. Äldre maskinpark då givetvis och vi var många fler på den tiden, närmare 25 verktygsmakare.
– Nu är snart verktygsmakare en utdöende art, skrattar Lars och jag förstår vad han menar. Tekniken har tagit över mer och mer men noggrannheten och finishen finns kvar, toleranserna blir allt snävare, så nog behövs verktygsmakaryrket alltid. För han tillägger;
– Vi söker fler verktygsmakare till vår maskinverkstad.
Maskinleverantören DMG MORI;
Vi får mer tekniska data av maskinsäljaren Anders Wikström på distrikt syd.
DMG MORI DMU 75 monoBLOCK, X/Y/Z=750/650/560 mm. Styrsystem CELOS/Siemens. 20 000 rpm Speedmaster spindle 35 kW/130 Nm. 60 stycken verktygsplatser HSK-63. 40 bar genom spindel och 600 liter pappersbands filteranläggning. MPC (Machine Protection Control). Mätprob PP60 och Blum laser för verktygsinmätning. 3D quickset. Operation mode 4.
DMG MORI DMU 210 P duoBLOCK, X/Y/Z=2100/2100/1250 mm. Styrsystem CELOS/Siemens. 20 000 rpm Speedmaster spindle 35kW/130 Nm. 60 stycken verktygsplatser HSK-100. Förhöjd bordsbelastning 10 000 kg. 40 bar genom spindel och 600 l pappersbands filteranläggning. MPC (Machine Protection Control). Mätprob PP60 och Blum laser för verktygsinmätning. 3D quickset. Operation mode 4. Maskinen väger 43 ton.
Allt sammankopplat med CELOS
– Eftersom KB sedan tidigare jobbade med NX CAM- system, så var valet enkelt att välja Siemens. Och då såg man såklart fördel med DMG MORI:s CELOS som är standard i maskinerna. Dels att man har möjlighet att få information i soffan där hemma genom Messenger funktionen, och statistik hur effektiva man varit med sina jobb.
Hur uppfattar du affären ur ett tekniskt och svenskt produktionsperspektiv?
– Detta var ju ett spännande projekt med en kund som investerar i bearbetningsmaskiner för att kunna bli bäst på sin kärnverksamhet formsprutade plastprodukter. KB har mycket stora verktyg till formsprutning upptill 2,1 meter i diameter och behövde klara av att lägga upp tunga verktygs halvor eller delar av de största verktygen. Så först beställde de en DMU160 men ångrade sig några veckor senare till en DMU210 istället med 10 tons bordsbelastning. Sedan var vi på referensbesök hos Tooltech AB och deras DMU210 och såg fördelen med att sänka ner maskinen nästan 1 m i golvet, vilket även KB gjorde.
– Det är roligt att ett svenskt företag satsar så här hårt för att bli bäst i världen inom sitt område och nästan lite osvenskt tänkande.
Intressant är att maskinerna kan gå fristående men kan också komplettera varandra då stora verktyg ofta är i flera delar.
– Med DMG MORI:s styrsystem CELOS/Siemens så är det väldigt enkelt att flytta jobben emellan maskinerna trots storleksskillnaden på maskinerna. En annan fördel är ju såklart att om man kör ett större verktyg i 210:an som kan ta upp till 80 timmar, så kan man alltid köra mindre detaljer i 75:an under tiden.
– Slutligen kan man säga att båda maskinerna är väldigt ergonomiska att jobba i, vilket är en stor fördel, då det skall gå mycket snabbt när ett verktyg gått sönder, behöver lagas eller ändras, säger Anders Wikström DMG MORI.
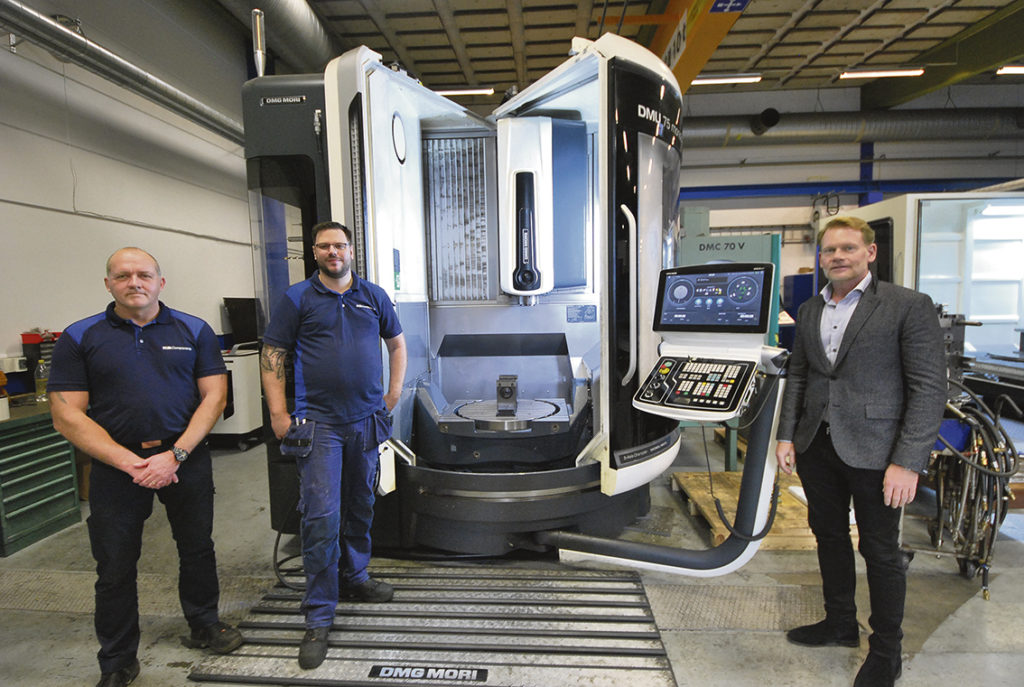
Sänk- och trådgnistning, nya maskinmodeller, det kan inte bli bättre förutsättningar för ett verktygsmakeri.
Vi på redaktionen har vetat om denna maskininvestering sedan vårt besök på Elmia Produktionsmässor i Jönköping 2018, då skrev vi så här i vår rapport:
”Svensk produktion växer. Vi skall nu informera om en mycket uppmärksammad maskinorder som togs på mässan.
Roger Jansson på Auran Industries som är agent för den japanska maskintillverkaren SODICK i Sverige berättar.
– Igår var det lite speciellt i vår monter på mässan, då KB Components i Örkelljunga hälsade på och lade en order på tre maskiner från SODICK.
– Ambitionen de har är att tillverka stora verktyg och framförallt kunna reparera och ändra i verktygen på fabriken i Örkelljunga utan att behöva skicka dem till Kina, Italien eller Portugal som man gör idag. Nu har man kommit överens med sina kunder att kunna ta hand om hela kedjan med tillverkning, reparationer och ändringar av stora formverktyg på hemmaplan, sa Roger Jansson
– Då man bestämt att investera i två stora fräsmaskiner från DMG MORI, har man nu valt att investera i SODICK gnistmaskiner. KB Components har i första läget köpt en medelstor sänkgnistmaskin som heter AG 60L. Och en medelstor trådgnistmaskin modell ALC 600G (se foto sid 64). Men nu kommer vi till det som är mycket speciellt och det handlar om ytterligare en investering i en riktigt stor sänkgnistmaskin XXL, som heter AG 200L. Den maskinen har en riktigt stor tank på 3 x 2 meter och nästan 1 meter i z (se foto sid 60).
– Den här maskinen kommer att hjälpa till att gnista och ändra i de större verktyg som behöver åtgärdas och man kommer att kunna lägga upp verktyg med en max vikt på 15 000 kg (15 ton) i maskinen, alltså riktigt stora verktyg. Maskinen kommer att landa i Örkelljunga under våren 2019.
– Det jag vet, så finns maskinen bara på ritbordet idag och att KB Components är det första verktygsmakeriet i världen som köper den nya modellen AG200L och vi lär återkomma i ämnet för ett besök på plats hos KB när maskinerna är installerade och igångkörda.
OCH NU ÄR VI HÄR och vi skriver 25 november 2020.
Maskinleverantör SODICK
Expert Roger Jansson ägare till Auran Industries som är generalagent för den japanska maskintillverkaren förklarar skillnaden mellan tråd – och sänkgnistning.
– Både tråd- och sänkgnistning avverkar allt material som leder ström med hjälp av ström. Trådgnisten som namnet beskriver använder en tunn tråd som elektrod, tråden är oftast 0,25 mm i diameter. Det fungerar att använda tråd som är mellan 0,03 och 0,33 mm i diameter i en trådgnist.
Från tråden skickar vi gnistor som avverkar materialet i arbetsstycket framför tråden. Tråden vidrör aldrig materialet utan det finns alltid en spalt mellan tråd och arbetsstycket (GAP).
Beroende på vilken tolerans och ytfinhet som vi önskar så gnistar vi flera gnistskär där vi justerar offset mellan varje skär samt sänker strömmen så att gnistorna blir kortare och svagare. Normalt 2 eller 3 skär men upp till 8 skär är det vissa som använder sig av.
Tack vare det så kan vi skapa väldigt noggranna mått och bra ytfinhet i en trådgnist. Vi når idag en nästan spegelblank yta i en bra gnistmaskin. Vanliga delar som tillverkas i en trådgnist är stansar och dynor till klippverktyg. Det blir fler och fler som använder sig av serietillverkning där det är viktigt med hög noggrannhet, exempelvis delning av svarvade ringar samt kedjelänkar.
Sänkgnistning använder en elektrod som oftast besår av grafit eller koppar, det går i princip att använda allt som leder ström som elektrod. Fördelen med grafit och koppar är att det är lätt att bearbeta till rätt form.
Vi sänker därefter elektroden mot arbetsstycket, när vi kommer så nära att det finns en möjlighet att en gnista kan uppstå mellan elektrod och arbetsstycke så startar gnistningen. Varje gnista avverkar en liten del av materialet i arbetsstycket och på så sätt skapar vi en kopia av elektroden.
Vanliga delar som tillverkas i en sänkgnist är insatser till formverktyg. Det blir även här fler och fler som använder sig av serietillverkning där det är viktigt med hög noggrannhet, exempelvis turbiner till flyget eller andra kraftaggregat.
Tekniska fakta;
Sänkgnistmaskin SODICK AG200L
Vattentanken 5 000 liter. Bearbetningsområde: X = 2 000 mm, Y = 1 250 mm och Z = 800 mm. Max. bordsbelastning 15 000 kg!
Trådgnistmaskin, SODICK ALC600G.
Bearbetningsområde: X = 600 mm, Y = 400 mm. och Z = 350 mm. Max. Bordsbelastning 1 000 kg.
Sänkgnist 2, SODICK AG60L.
Bearbetningsområde: X = 600 mm, Y = 420 mm och Z = 370 mm. Max bordsbelastning 1 500 kg.
Japanska maskintillverkaren SODICK är en av få specialister och leverantörer av gnistmaskiner och utrustning. Företaget är sedan starten ett familjeföretag och är det fortfarande idag. Sonen till grundaren är vd och fortfarande aktiv i den dagliga verksamheten.
Företaget tillverkar mer än 7000 avancerade maskiner per år och av dessa är flertalet gnistmaskiner. De stora förändringarna är givetvis det som hänt under huven på maskinerna.
– Den största är att vi idag har linjärmotorer för drivning av axlarna i alla maskiner som vi producerar i egen regi, på våra fabriker runt om i världen, säger Roger Jansson.
Vad är trenderna, vilka är kunderna?
– Gnistning är och kommer att förbli en bearbetningsmetod som vi behöver för att klara de ökade kraven. Kunderna idag är allt från traditionella verktygsmakare med verktyg samt mindre serier 1–20 detaljer ofta med hög precision. Till stora produktionsbolag med större serietillverkning med stor precision och/eller svåra material.
Och Roger kommenterar affären med KB Components.
– Det är alltid trevligt att få chansen att sälja 3 maskiner på ett bräde och dessutom vara den första i välden som lyckas att sälja maskin nummer ETT. Just nu så känns marknaden lite tilltufsad när vi står mitt i en pandemi. Men alla står inte och väntar, vi fick just en större order på 2 sänkgnistar och rälsrobot från Erowa som vi ska göra ett trevligt reportage om nästa år, avslutar Roger Jansson.
– Gnistbearbetningsmetoder är en stor del i tillverkningsprocesserna i ett verktygsmakeri. Allt det att man tillverkar, förändrar eller reparerar ett formverktyg, går inte att fräsa utan det kräver precision och noggrannhet utöver det vanliga, säger Lars Pedersen.
Och Lars förklarar varför det blev SODICK.
– Vi var ett team på KB som fann att SODICK hade det vi ville ha och efter flera kontakter med andra fabrikat, så fastnade vi för den japanska maskintillverkaren som är specialister på gnistning.
Varför blev storleken en XXL maskin?
– Vi förstod att med en fräsmaskinsmodell XXL så klara de vi 10 ton på bordet men vi behövde säkra upp eventuella större verktyg upp mot 15 ton. Därför föll valet p.g.a. de fysiska måtten på våra stora verktyg, på en rekordstor trådgnistmaskin för att klara våra framtida krav på riktigt stora formverktyg, säger Lars Pedersen.
– Till slut blev det två tillverkare som ställdes i varsin ringhörna för flera andra tillverkare föll bort då man inte hade den bredd som SODICK har. Spanien mot Japan och valet föll på Japan. Jag var med under hela inköpsprocessen och med min långa erfarenhet som verktygsmakare sedan 1993 så fann jag att SODICK kunde presentera det bästa alternativet, säger verktygsmakare Christian Nilsson.
– Jag och mina medarbetare arbetar dagligen med hundradelars toleranser. Och augusti 2019 installerades maskinerna. Idag har gnistning fått en renässans som bearbetningsmetod och är allt viktigare för att erhålla rätt tolerans och rätt finish på produkter och komponenter.
– SODICK var ett helt nytt fabrikat för mig men jag är mycket imponerad av fabrikatet och tillverkaren i stort och smått, jag är nöjd med valet av ett nytt fabrikat här på verktygsverkstaden, säger Christian Nilsson med nästa 30 års erfarenhet som verktygsmakare, så han vet vad han pratar om.
Vi på redaktionen på Tidningen Maskinoperatören tackar för besöket och man kan inte annat än imponeras av svenska företags framåtanda att bli ledande tillverkare inom sin nisch i Sverige, Europa och kanske Världen. Vårt besök hos KB Components följde alla restriktioner som folkhälsomyndigheten satt upp som krav för att resa över regioner och träffas under säkra former.
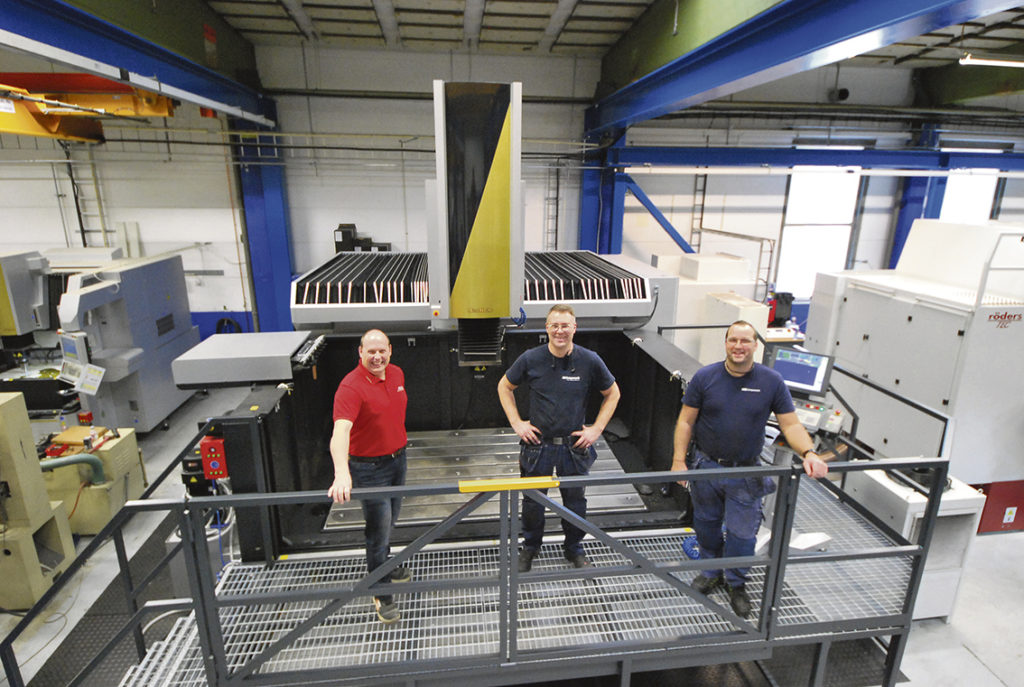
Bakom verktygsmakare Christian Nilsson, Mikael Jansson, Lars Pedersen underhållschef och Roger Jansson Auran Industries ser vi till höger; Trådgnistmaskin, SODICK ALC600G. Bearbetningsområde: X = 600 mm, Y = 400 mm och Z = 350 mm. Max. Bordsbelastning 1 000 kg.
OCH
Sänkgnist 2, SODICK AG60L. Bearbetningsområde: X = 600 mm, Y = 420 mm och Z = 370 mm. Max bordsbelastning 1 500 kg.
Maskininvesteringen i fabriken i Örkelljunga ger snabbare verktygsreparationer och garanterar i nästa steg, kontinuerligt hög leveransprecision av formsprutade detaljer.