Många industrier lever idag i en situation av ständig förändring, ökade krav med sänkta produktions- och leveranstider, detta går snabbare än någonsin. Det ställer höga krav på medarbetarnas kompetens och den produktionsutrustning som finns att tillgå. Ett samarbete mellan människa, datastyrda maskinsystem och mjukvara, blir mer och mer den enda framkomliga vägen för konkurrenskraftig produktion på en komplex och hårt konkurrensutsatt marknad.
Men grundläggande är att spindeln skall snurra och gå, det är det viktigaste för en verkstadsägares lönsamhet, att göra spån. Så trots alla budskap om digitalisering, automatisering och smarta fabriker, så är det givetvis fortfarande smartast om man kan producera så mycket spån per timme och dag som möjligt.
Vi ser just nu hur samhället förändras, förändringarna har blivit mycket tydligare nu efter Corona pandemin. Den stora trenden inom industrin med satsningar på en allt mer automatiserad produktion har förstärkts ytterligare då leverantörskedjorna blir kortare och företag flyttar hem delar av sin produktion vilket ökar efterfrågan på automatiseringslösningar. Man går ifrån massproduktion vilket gynnar den svenska industrin.
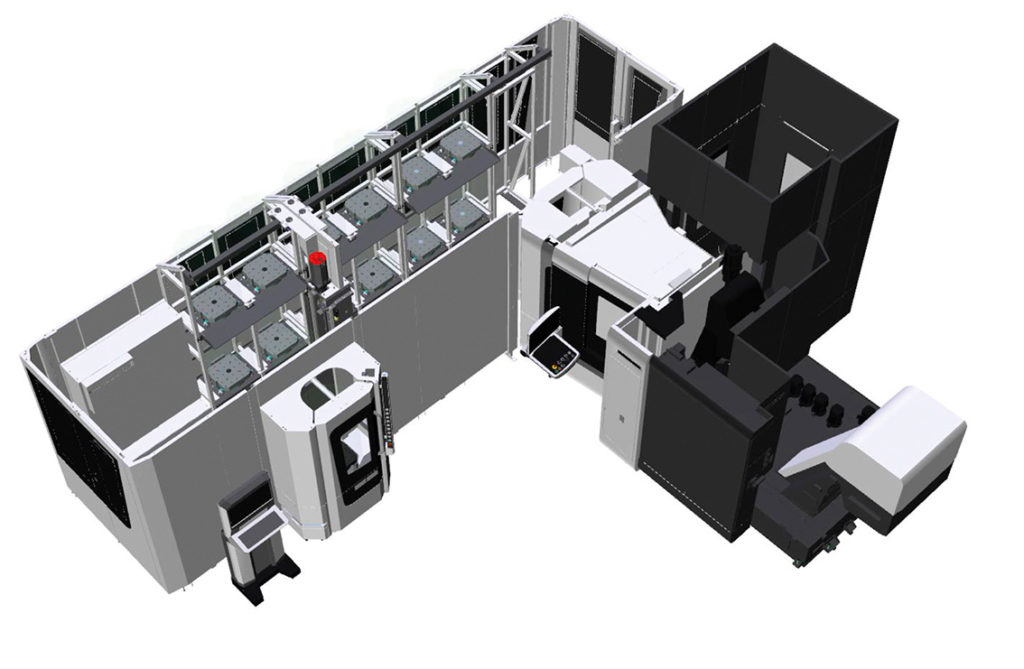
Men vi ser också mörka moln på himmelen med krig i Europa, höga räntor, elbrist och inflation. Detta måste företagen i svensk industri hantera på olika sätt. Tiden är förbi när det var som man sa förr, att sju dåliga år alltid följdes av sju goda år. Det var mer lätthanterligt på den tiden måste vi tillstå. Och det betyder att ett verkstadsföretag som BoMek måste arbeta med en ständig transformering av sin verksamhet. Anpassa, anpassa och anpassa, förbättra, förbättra och förbättra. Det ställer stora krav på kompetens och kunnande, mod och strategi, göra omvärldsanalyser på kort och lång sikt, arbeta i lag och samtidigt lita på sin inre kompass.
Hos BoMek Verkstads finns denna kunskap och erfarenhet då företagsledningen arbetar utifrån kompetens från många års erfarenheter från industrin.
Tiden står inte still
Tid är en av vår viktigaste och mest värdefulla resurs. Ibland känns det som att tiden står still men oftast är det som om timmarna bara rusar förbi. I våra artiklar skriver vi om produktion och om produktivitetshöjande insatser i form av ny maskin- och verktygsteknik och förbättrade arbetsmetoder. Människan är i fokus och bestämmer i mångt och mycket hur mycket vi skall och kan hinna med på 24 timmar, en vecka eller en månad. Det är ju tiden som vi hela tiden handlar med. Har människan alltid haft ont om tid, nej men idag och vi pratar och fokuserar på tillverkning av produkter inom en viss tid och en viss leveranstid. Tiden är vad vi mäter med en klocka och med en sådan definition av tiden öppnas dörren för en hel rad olika scenario.
Så om produktionen skapar ett stort värde på få arbetstimmar innebär det att produktiviteten är hög. Och kapaciteten ökar dramatiskt om ett företag bestämmer sig för att öka automationsgraden i sina processer. Ledningsgruppen på BoMek Verkstad i Göteborg tog 2019 ett avgörande beslut om att starta en inköpsprocess, utmana sig själva och flera av världens ledande maskinleverantörer, hitta en optimal automationslösning för att på sikt i princip, kunna köra produktion dygnet runt alla dagar i veckan. VD Jonas Hedlund, produktionschef Robert Dahlsjö och teknikansvarige Johan Angelin, alla med en lång kedja av olika erfarenheter i branschen, kom nu att under flera år vara inne i en intensiv fas där slutmålet för arbetet var en optimal och högteknologisk produktionscell, teknikintensiv, flexibel och smart digitaliserad. Och allt arbete landade i en komplett automationscell, en helhetslösning från DMG MORI och som installerades under oktober månad i år.
Ett teknikkliv för framtiden – DMG MORI NHX4000 med automation LPP FMS anläggning, utrustad med ett 12 paletters system
Som reporter söker man alltid efter nyheter, gärna det där lite speciella och här är jag nu på Kalkbruksgatan 7 på Hisingen, där en spännande maskininstallation är på plats. Storleken spelar roll, det är det första vi kan slå fast. Och här finns också ett 5-axligt strategitänk mitt i en större automationsfas där underleverantören BoMek Verkstads i Göteborg nu tar nästa steg i sin utveckling för att möta morgondagens behov och gärna i en ökande intern digitaliserad produktionsmiljö. Det låter tekniskt komplicerat och det är det men vi tar det från början.
Det finns många fördelar och stora vinster att göra med automatiserade processer. Det kan handla om bättre arbetsmiljö, ökad produktivitet, högre konverteringsgrad och tidsbesparingar. Automation kan också ge möjlighet till ökad flexibilitet vilket gör det möjligt att ta fler typer av affärer.
– Smart automation gör produktionen enklare, säger maskinsäljare Peter Smith på DMG MORI Sweden, när vi slår oss ner vid kaffebordet.
Runt bordet sitter förutom Peter även Olof Gyllenoxe som är teknikansvarig på DMG MORI, Jonas Hedlund vd och Johan Angelin teknikansvarig på BoMek Verkstads.
Vi ber Olof Gyllenoxe och Peter Smith på DMG MORI Sweden att ge oss information om maskintekniken.
– Den nya maskinen heter NHX4000 Gen 3 med palletsystem LPP12. Det är det första LPP systemet i Sverige och är utbyggbart för att kunna addera flera maskiner, paletter och laddstationer. BoMek har för avsikt att bygga ut sitt system med en till maskin, laddstation och 12 paletter till.
I maskinen finns ett verktygsmagasin med 240 platser, där verktygen är identifierad med Tool ID chip som läsas av vid verktygsbyten. Spindeln är en 20 000 rpm DMGMORI SpeedMaster motorspindel, med 3 års garanti oavsett drifttimmar.
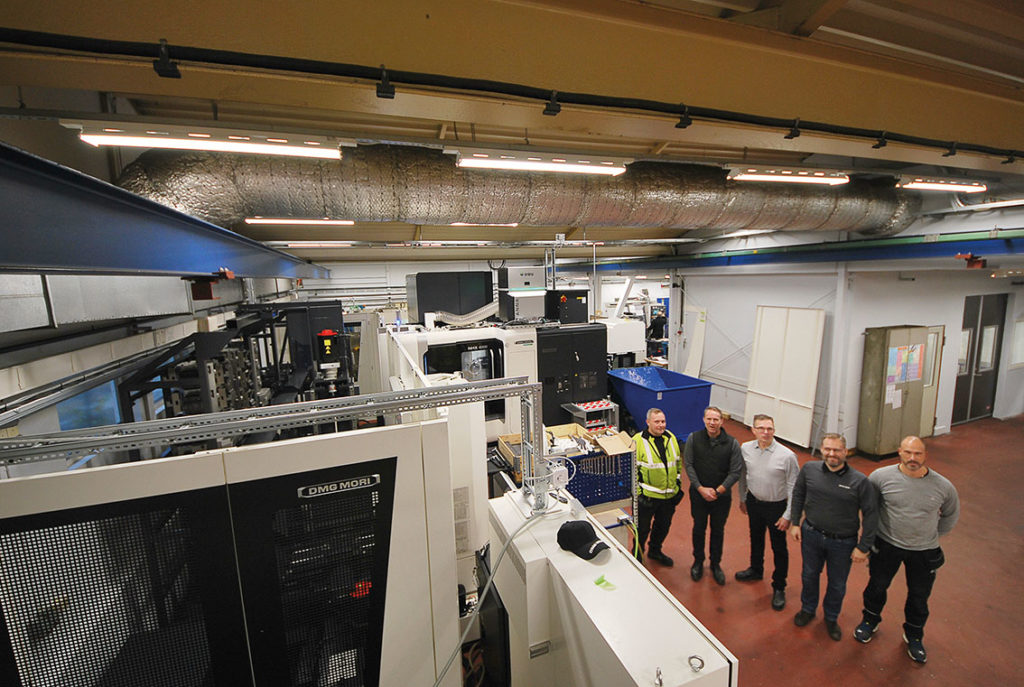
NHX-serien Generation 3 erbjuder förbättrad ”cost per part” prestanda genom att drastiskt minska antalet delar och är designad för att spegla aktuella marknadsbehov och 3 000 feedbackkommentarer från kunder. Den är fullspäckad med omfattande funktioner inklusive (1) hög hastighet (2) hög styvhet, (3) hög noggrannhet, (4) energibesparing, (5) CELOS med Fanuc.
– NHX4000 och NHX5000 har en snabbgång på 60 m/min. NHX4000:s palettindexeringstid är 1,0 sekund (1 grads indexering), och NHX5000:s är 1,49 sekunder (90 graders indexering). Båda modellerna erbjuder dramatiskt ökad produktivitet.
NHX-serien uppnår hög styvhet och stabil bearbetning genom att använda en tung, styv bädd med X- och Z-axelns linjärstyrningar placerade i ett högt läge, spindel med ett lager med stor diameter och ett bord och paletter med en kraftfull låsningskraft. NHX-serien erbjuder förbättrad positioneringsnoggrannhet genom att minska vikten av rörliga delar. Dessutom använder den mätskalor som standard för att säkerställa hög noggrannhet.
– NHX-serien är utformad för att minska miljöbelastningen och driftskostnaderna. Med en hydraulpump som används i den konventionella modellen roterar hela tiden för att bibehålla trycket, kan pumpen som används i NHX-serien stoppas under standby eftersom en ackumulator är ansluten till hydraul enheten. Dessutom har antalet motorer minskat. NHX-serien har uppnått en minskning av den totala strömförbrukningen med cirka 40 % jämfört med den konventionella modellen.
CELOS-Fanuc F31iB med MAPPS V. NHX-serien använder CELOS – ERGOline Touch. Det är en maskinmanövreringspanel med 21,5-tums multipekskärm, som gör det bekvämt att använda. Den dokumenterar, visualiserar och hanterar order-, process- och maskindata centralt, vilket möjliggör nätverk med CAD/CAM och även funktionsutvidgning med applikationer. Det användarvänliga, högproduktiva MAPPS-systemet är installerat.
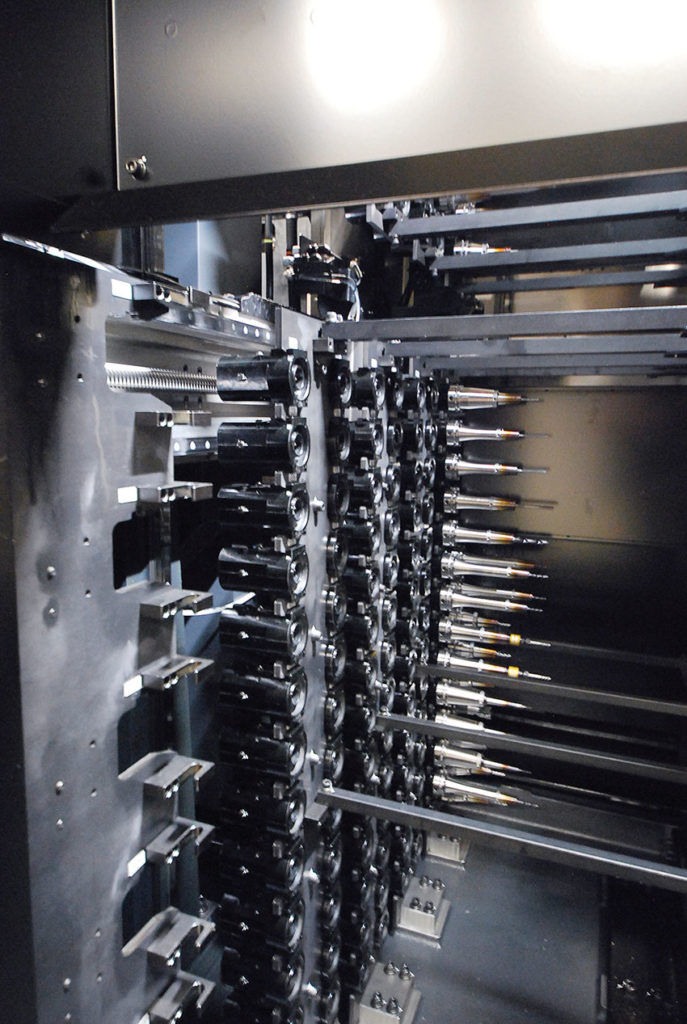
Automationen
LPP-systemet (Linear Pallet Pool) kan utrustas med pallställ i flera nivåer, vilket ger en hög grad av automatisering. Systemkonfigurationen kan anpassas för att passa kundens behov. Överlägset och avancerat högproduktivitetssystem som minskar omställningstid genom att kunna placera flera fixturer på paletterna i förväg när du får återkommande beställningar. Minskade personalkostnader eftersom systemet tillåter långvarig automatisk drift kan minska bemanningsgraden och köra obemannad operation på natten.
DMGMORI egen kontroll MCC-LPS 4 låter kunden hantera produktionsscheman flexibelt och är kopplad till verktygshanterings mjukvara MCC-TMS som håller uppsikt på vilka verktyg som är tillgängliga i magasinet.
En av de enskilt största åtgärderna för att öka tillgänglighet och lönsamhet är enligt Peter och Olof på DMG MORI, att investera i stora verktygsmagasin så att operatören slipper onödig och tidskrävande verktygshantering. Nummer två på listan är hantering av fixturer. Nummer tre på listan handlar om effektiva CAM- och berednings lösningar.
– Med högpresterande och automatiserade verktygsmaskiner, ofta standardlösningar med smarta fixtureringar och gemensamt interface mellan mjukvara och snabbväxlingssystem står du inte och knackar på fixturen i en halvtimme utan kan snabbt köra igång, förklarar Peter Smith och Olof Gyllenoxe på DMG MORI.
Trenderna är många och teknikutvecklingen går rasande snabbt. Tidningens redaktör ser trender där man nu inom DMG MORI lägger ett stort fokus på digitalisering och automatisering.
– Det handlar om att lägga pussel inom kompetens och applikation”, säger Johan Angelin på BoMek Verkstads.
Verktygsmaskiner som skall klara allt mer moment som fräsning, svarvning, borrning, gradning, hening, slipning, märkning samt utföra kvalitetskontroller i en och samma uppspänning och maskin, är numera helt och fullt möjligt. Automatiseringen går framåt med förenklade system där man inte behöver specialistkunskaper längre utan med hjälp av CNC kontrollen CELOS och olika appar kan styra produktionen på ett enkelt och effektivt sätt.
– Men vi måste bli bättre på att kommunicera med maskinerna och här har DMG MORI det numera etablerade styrsystemet CELOS med alla appar som Messenger och Connectivity samt de större digitala systemen som WERKBLiQ och TULIP, säger Olof Gyllenoxe.
– Vårt uppdrag är att anpassa och skräddarsy automationssystem från det enkla handhavandet som robot till ett fullt helautomatiska FMS system som vi ser här idag på BoMek, säger Olof Gyllenoxe.
– Vi kan idag erbjuda en framtidsorienterad produktion med standardiserade och individuellt anpassade automationslösningar direkt från vårt moderbolag DMG MORI, säger Olof.
Kärnan i förlängningen är digitalisering
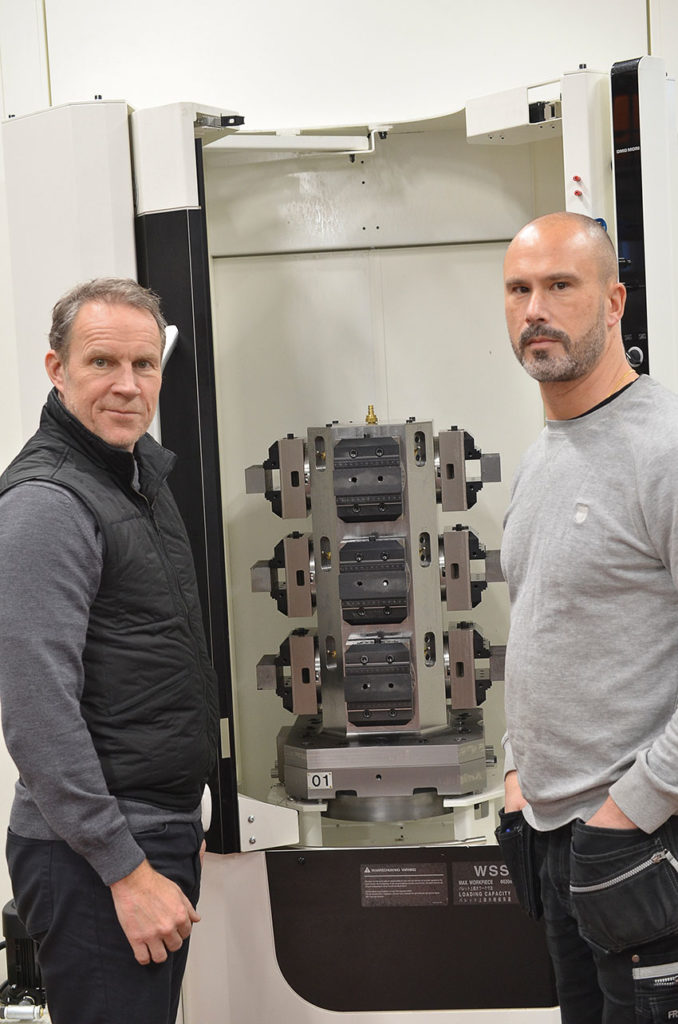
DMG MORI driver digitaliseringen inom verktygsmaskinstillverkning framåt och en kärnkomponent är automatisering. CNC-teknologin måste integreras i en sammankopplad produktionsmiljö där operatören kan övervaka och hantera bearbetningen medan maskinerna arbetar självständigt genom orderlistan i prioriteringsordning. Det är vad som kännetecknar en digital fabrik.
– De nödvändiga komponenterna är helt maskinstyrda och automatiserade. Och jag ser ingen annan väg för oss som verkstadsföretag än att förbereda, påbörja, standardisera, utveckla flerfunktion med automatik och så småningom fortsätta processerna med en utbyggnad av palettsystemet och en fleroperationsfräs till, säger Johan Angelin, teknikansvarig projektledare.
Vi återvänder till frågan om 24 timmars produktion och om det är möjligt. Ett finskt automationsföretag har ett mantra – 8760 – där ”fyra siffror” på ett mycket pedagogiskt sätt beskriver antalet produktionstimmar som finns tillgängliga under ett år. Att kunna utnyttja alla timmar under ett år för produktion, ses idag lite som en utopi i sig.
– Det vi ser nu här hos BoMek är en nödvändighet idag och framförallt imorgon, för att överleva som verkstadsföretag, framförallt som underleverantör. Vi möter många företag som anser att man vill avvakta att automatisera i större utsträckning men då kan det vara försent. Svensk och global industri automatiserar nu för fullt och det betyder de företagen som inte automatiserar sin verksamhet får svårt att konkurrera, ja det blir så stor skillnad att det blir i princip omöjligt att överleva på lång sikt, det är min personliga erfarenhet efter 20 år som maskinsäljare, säger Peter Smith.
– Vi ser att vi måste få ut många fler timmar på en produktionsdag och med en allt mindre bemanning. Plus att detaljerna behöver vara helt färdiga när de lämnar maskinen. All efterbearbetning och handpåläggning måste minimeras som exempelvis gradning och kontrollmätning, säger Jonas Hedlund, – Och det kräver stora satsningar på CAM-beredning.
– Vi har som mål att få ut 5 000 spindeltimmar per år från vår nya maskininvestering men då pratar vi på ett års sikt. För att uppnå detta, så måste vi skapa en trygghetskänsla för operatörerna. Alla måste lita på program och rigginstruktioner som vi får ifrån Edgecam. Paletterna riggas sedan utanför cellen och kuber samt nollpunktssystem från Schunk gör att det blir lätt att duplicera riggningen. Vid inkörning av jobbet tar vi hjälp av 3D Interference check som är DMG MORI’s antikollisionssystem. Verktygshållarna är chippade vilket minskar risken för felinmatningar av ställdata samt underlättar för oss att ha koll på verktygets livslängd. Vi har vid tidigare automationsprojekt insett hur viktigt det är att dimensionera skärvätskehantering samt spåntransportörer så att de skall klara dygnet runt produktion, säger Jonas och Johan.
– Den svagaste länken i kedjan kommer hela tiden att sätta begränsningen, så allt måste intrimmas och fungera som en helhet, säger teknikansvarige Johan Angelin som också är projektansvarig för maskininvesteringen.
Gränsen för maskinutnyttjande
– Tittar vi nyktert på det så har vi alla höga mål men kan vi nu så snabbt som möjligt och om man tittar på andra liknade automationslösningar nå 3 000 spindeltimmar per år, så är det riktigt bra. Pratar vi produktion i 45 veckor så handlar det om c;a 65 timmar i veckan. – Och vill man vara bäst i världen, ja då hamnar man på 100 – 125 spindeltimmar i veckan men då krävs väldigt mycket planering och att man har olika digitala lösningar som hjälpmedel, räknar Peter Smith.
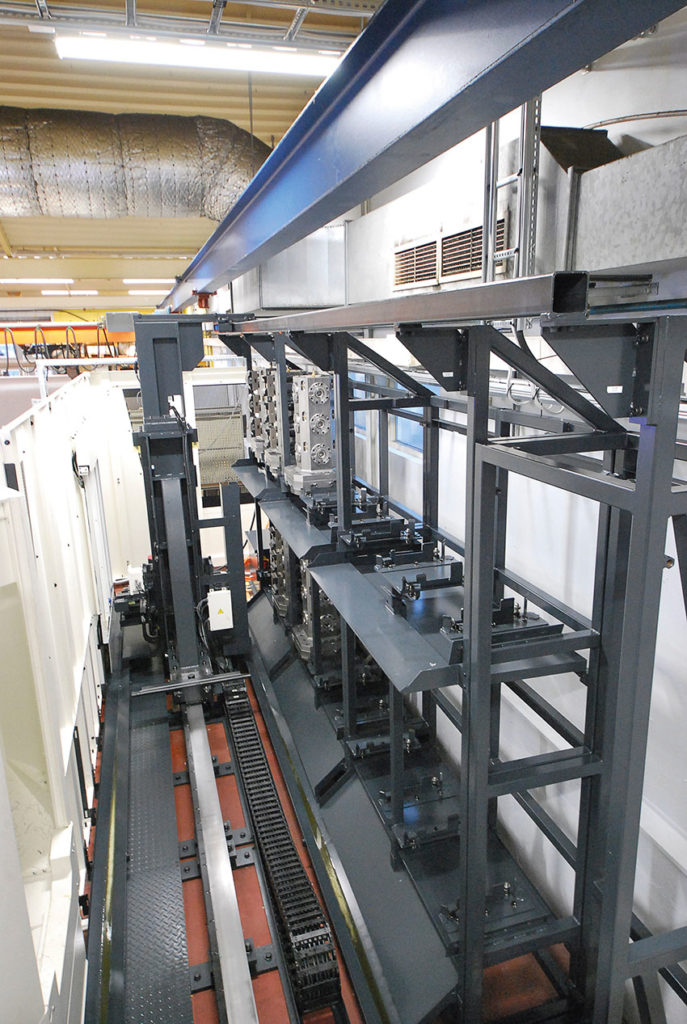
Återigen handlar det om tid.
– Vi har flera och olika automationslösningar idag men detta är en unik maskin som ger oss enorma möjligheter att öka vår produktionskapacitet. Vi måste fortsätta vår automationsresa med den senaste tekniken som finns på marknaden. Då kan vi känna oss trygga i att fortsätta att vara konkurrenskraftiga och hålla våra leveranstider, säger Jonas Hedlund
Vi vill veta mer om vårt företagsbesök idag;
Göteborgsbaserade BoMek Verkstads AB är en legotillverkare som grundades 1972. Deras inriktning är skärande bearbetning. De är för närvarande 48 medarbetare och omsätter 56 miljoner kronor.
– Hos oss har varje operatör inte bara ansvar för sin maskin utan också för varje bit hen tillverkar. Det bidrar till inställningen att vi tillverkar produkter och komponenter, och inte bara fräser och svarvar bitar, säger Jonas Hedlund.
BoMek tillverkar detaljer till optikindustri, laserindustri, medicinindustri, bilindustri, maskinbyggare, rymdindustri med mera. Företaget arbetar med allt från enstaka prototyper och reparationsarbeten till medelstora serier. Det här sker i alla förekommande material. Specialiteten är svarvningi rostfritt och Duplexa material samt fräsning och svarvning av finmekanik i Aluminium. BoMek tillverkar även komponenter i stål, mässing, koppar, nickellegeringar och plast, – Och då måste vi ha en anpassad maskinpark för framtiden.
Och vi ställer en sista fråga;
Går det bra?
– Ja, riktigt bra. I princip så ökar alla våra kunder sina beställningar och därför vet jag inte vad vi hade gjort om vi inte investerat
i vår nya maskincell från DMG MORI. ■